Glossary
NESPERT CAM terminology
Part
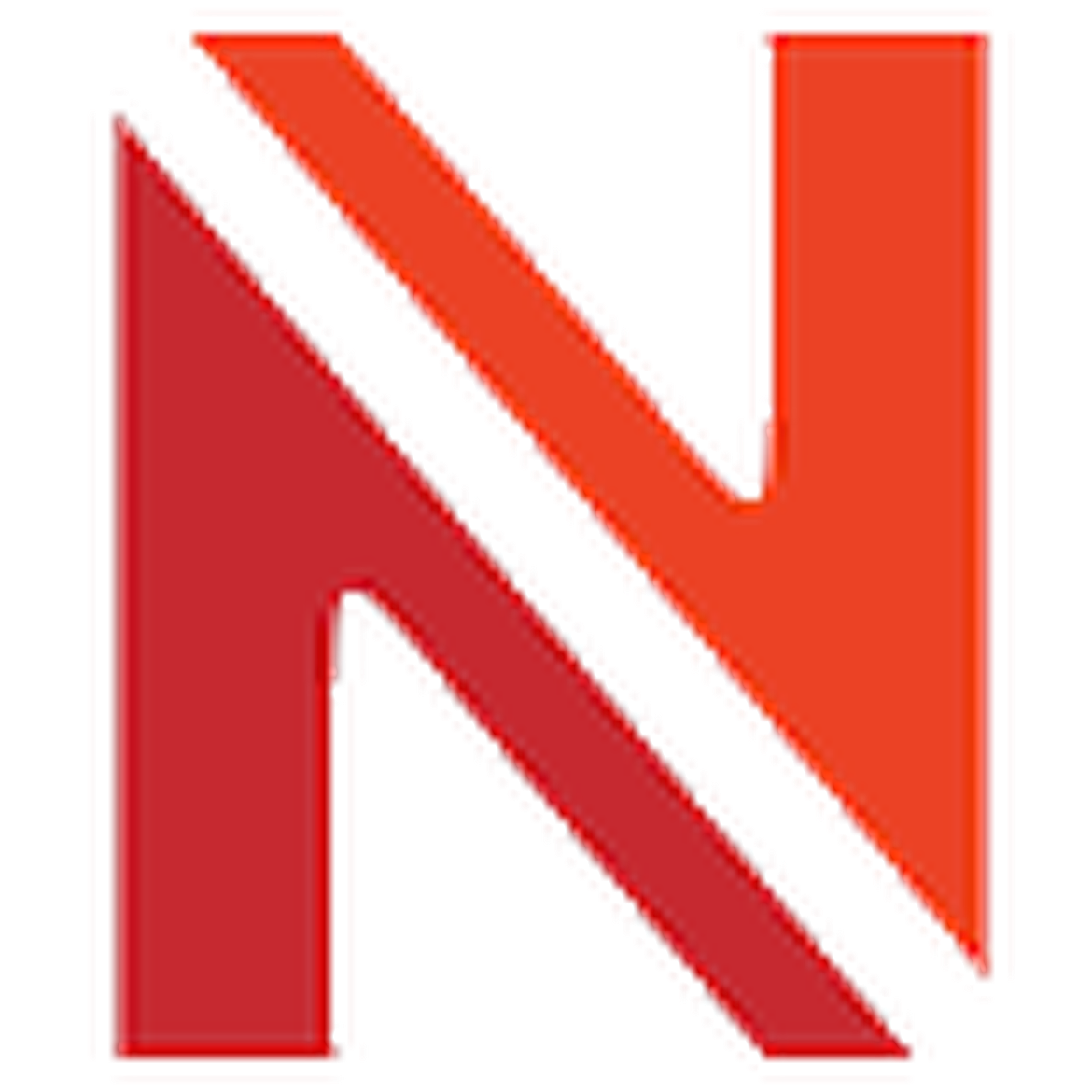
A part is a group of geometric contours with attributes that correspond by size and shape to the true shape part or to its inter-operational condition.
The geometry should not include equidistant offset for reading the processing radius/kerf.
A part can contain a single closed outer contour, multiple closed inner contours, multiple open contours with different uses and point sets.
The outer contour must enclose all inner closed contours of the part.
The closed contours must not self-intersect or to be on layers named "42" or "43".
At certain conditions texts may be included in the part as well.
During the design process, NESPERT CAM does not change in any way the geometry of the part.
Multi-part
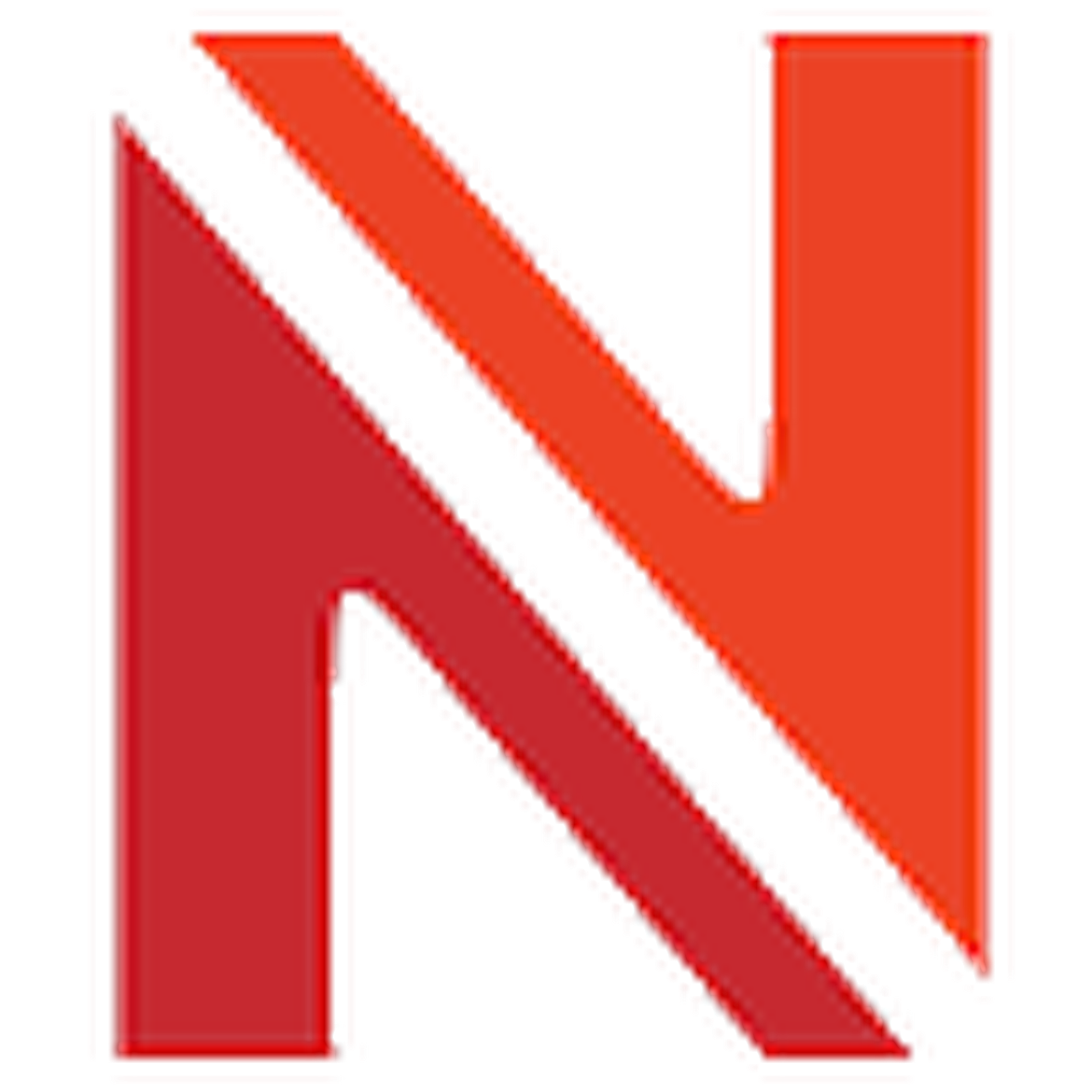
Multi-part is an object containing the geometry of more than one part.
When importing a multi-part, NESPERT CAM keeps the mutual placement of the individual parts. The control of nesting and creating a multi-part cutting technology is performed with the standard functions of the system.
NESPERT CAM provides the option to automatically break down a multi-part into separate parts.
CAD geometry of a part
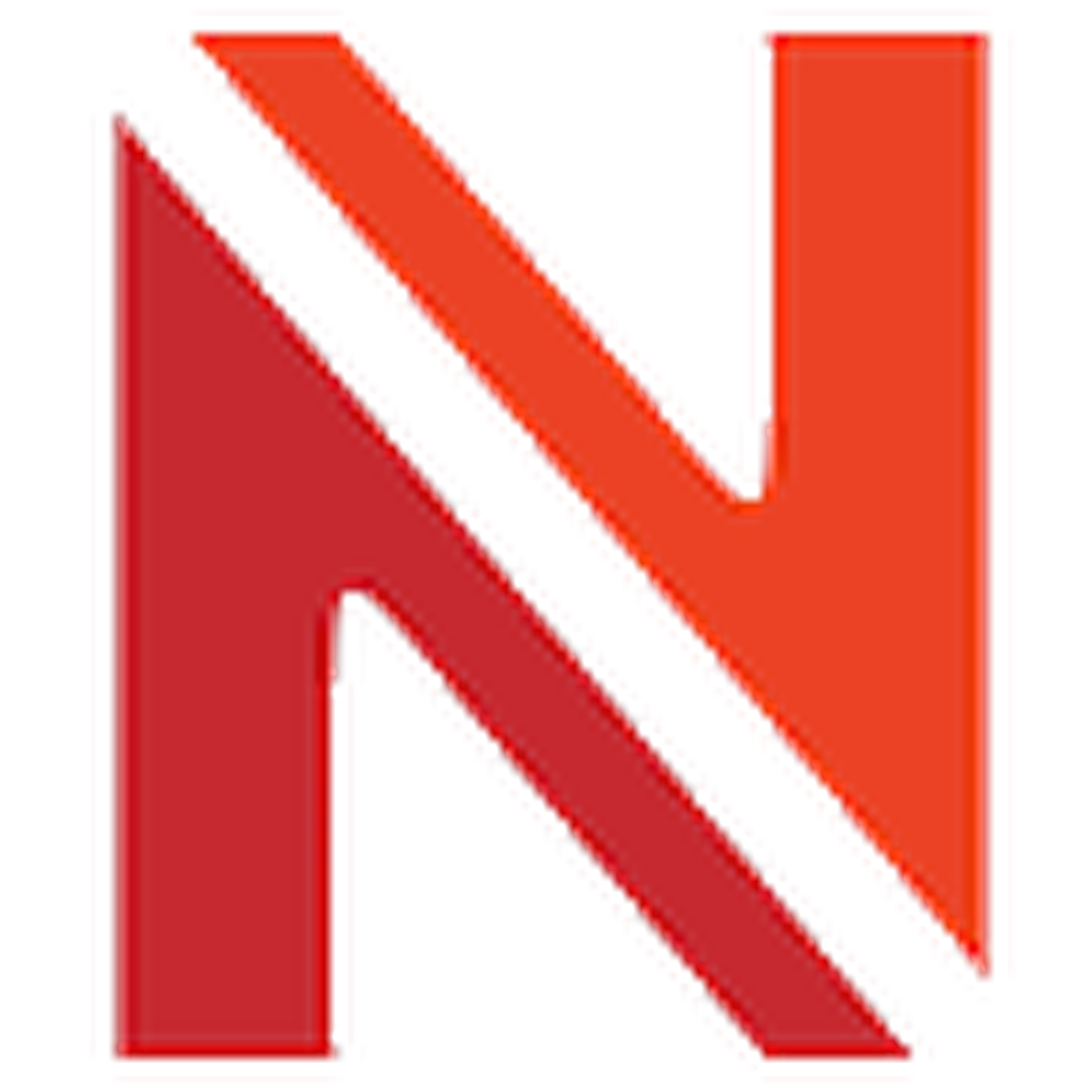
NESPERT CAM creates a geometry of a part by importing from CAD geometry.
The CAD geometry could be a 2D geometry or the projection of a 3D wire-frame geometry in the OXY plane.
NESPERT CAM import the following geometry primitives from CAD files: lines, circular and elliptic arcs, polylines, NURBS splines, points and texts.
When importing, the CAD primitives are transferred to contours consisting of lines and arcs. At certain conditions points and texts are added to the part for their subsequent processing.
Geometry import
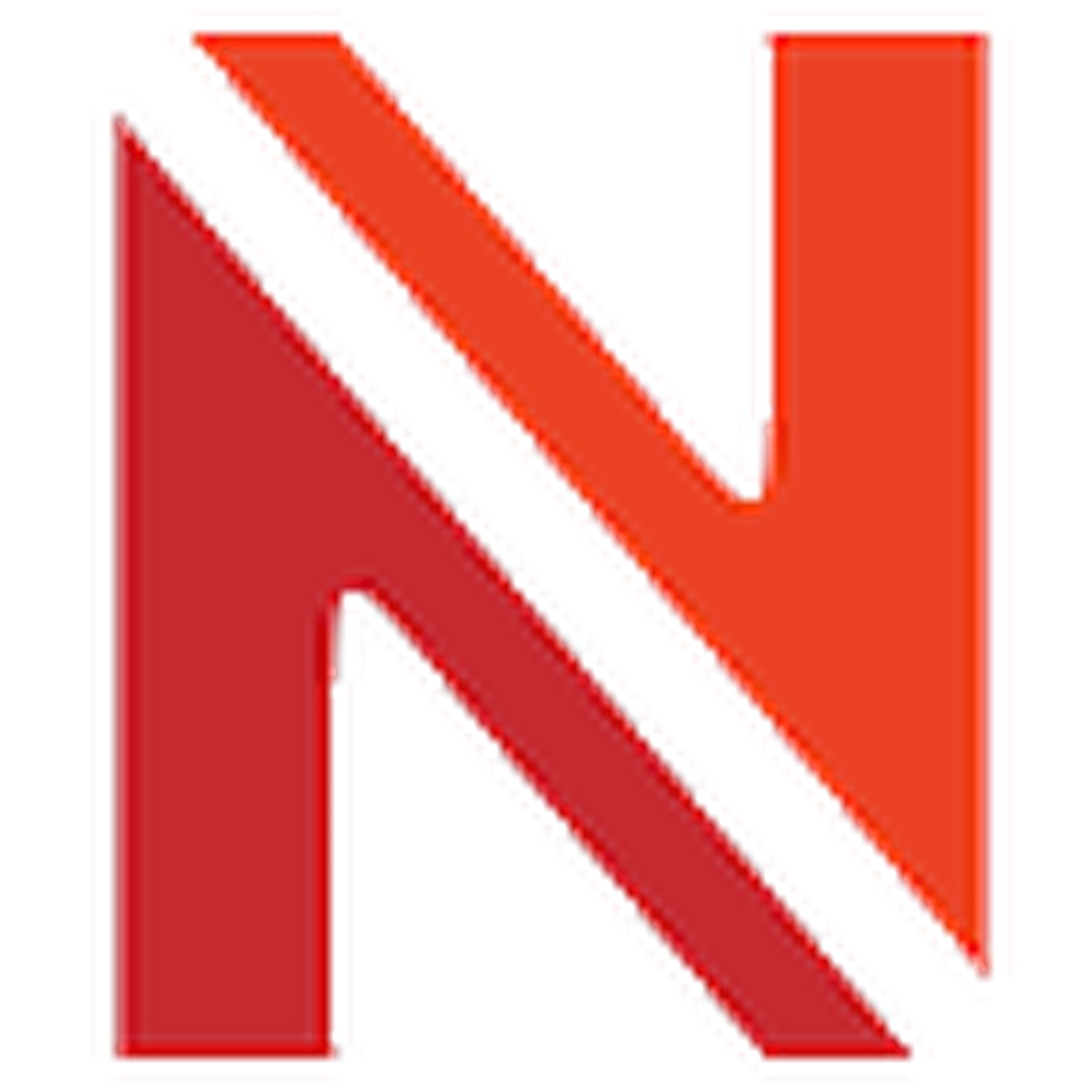
NESPERT CAM imports CAD geometry of parts and multiparts from CAD files in DXF, DWG, SVG, ESSI or DSTV format.
When SolidEdge is installed NESPERT CAM imports CAD geometry of sheet parts from PSM format, and when KOMPAS-3D/KOMPAS-Graphic is installed imports CAD geometry from CDW format.
During import NESPERT CAM:
- reads geometry of CAD file,
- when the file contains multiple AutoCAD blocks, the system loads parts of selected blocks,
- when CDW file contains multiple macro-parts, the system loads parts of selected macro-elements,
- When the file name or the AutoCAD block contains quantities, the system automatically fills in the quantities of the parts in the nesting Job.
During import of CAD geometry the system creates contours for processing a part and in the same time corrects the defects of the CAD geometry without changing the size of the part and:
- allows changing the units of measurement of the input geometry,
- the system intelligently corrects geometric defects and marks the locations of the remaining errors,
- defines the contour type in the part as: outer and inner closed, three types small holes, slot, marking geometry and point set
Parametric parts
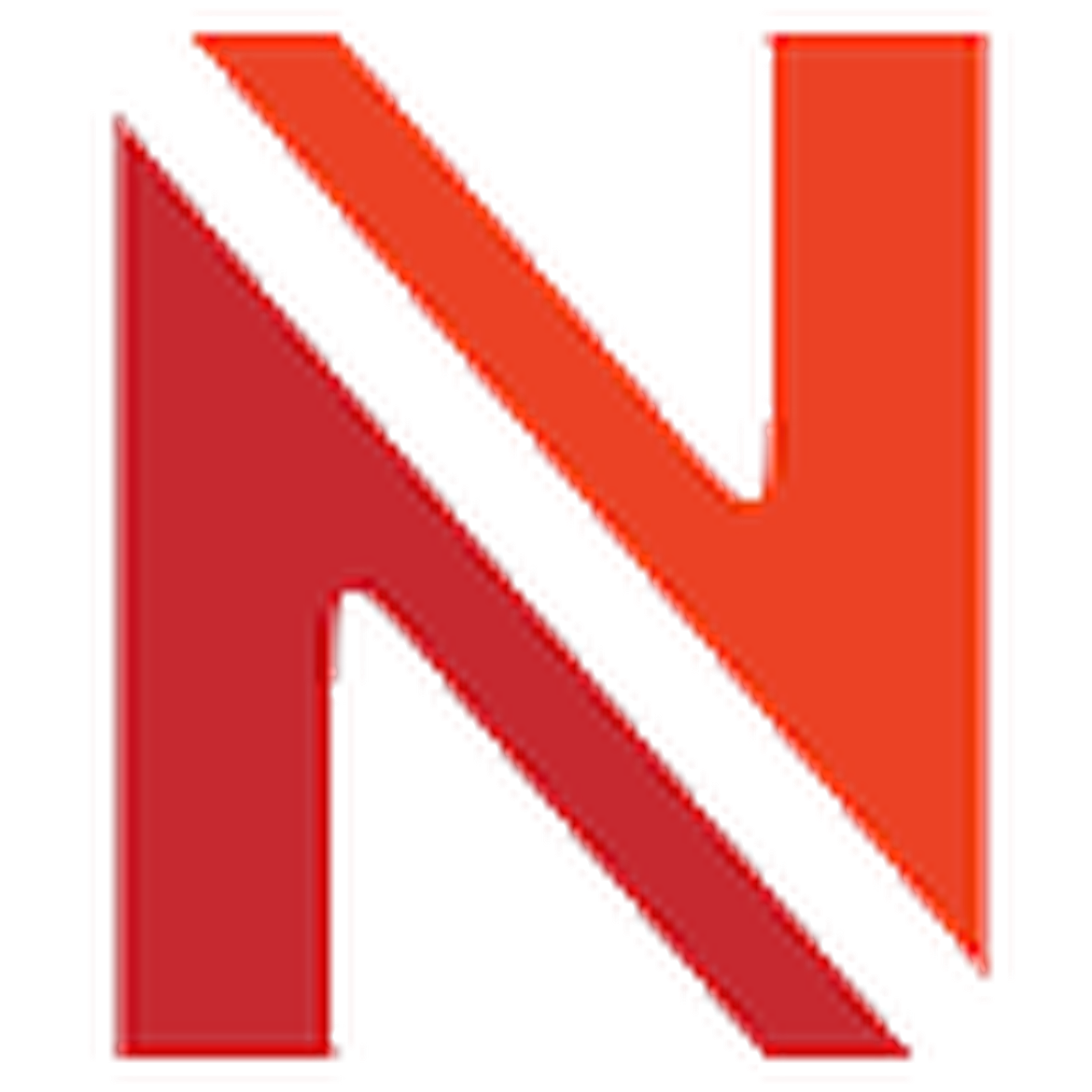
The parametric parts are Python programs, organised in libraries.
Their execution in the NESPERT CAM environment creates parts in the system.
Nesting order
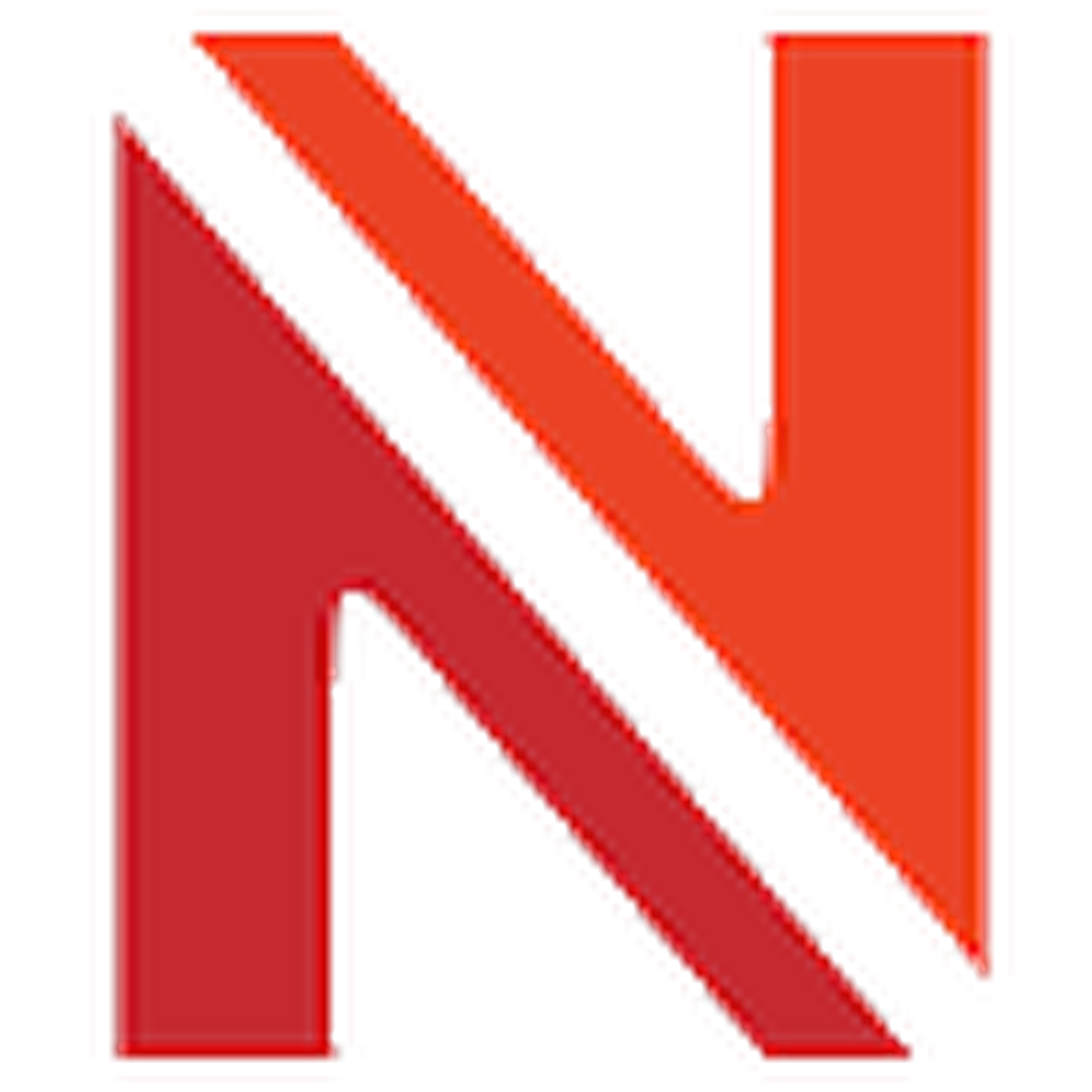
The nesting order in true shape nesting is a list of parts of different material grade and thickness and different type of thermal cutting.
Nesting job
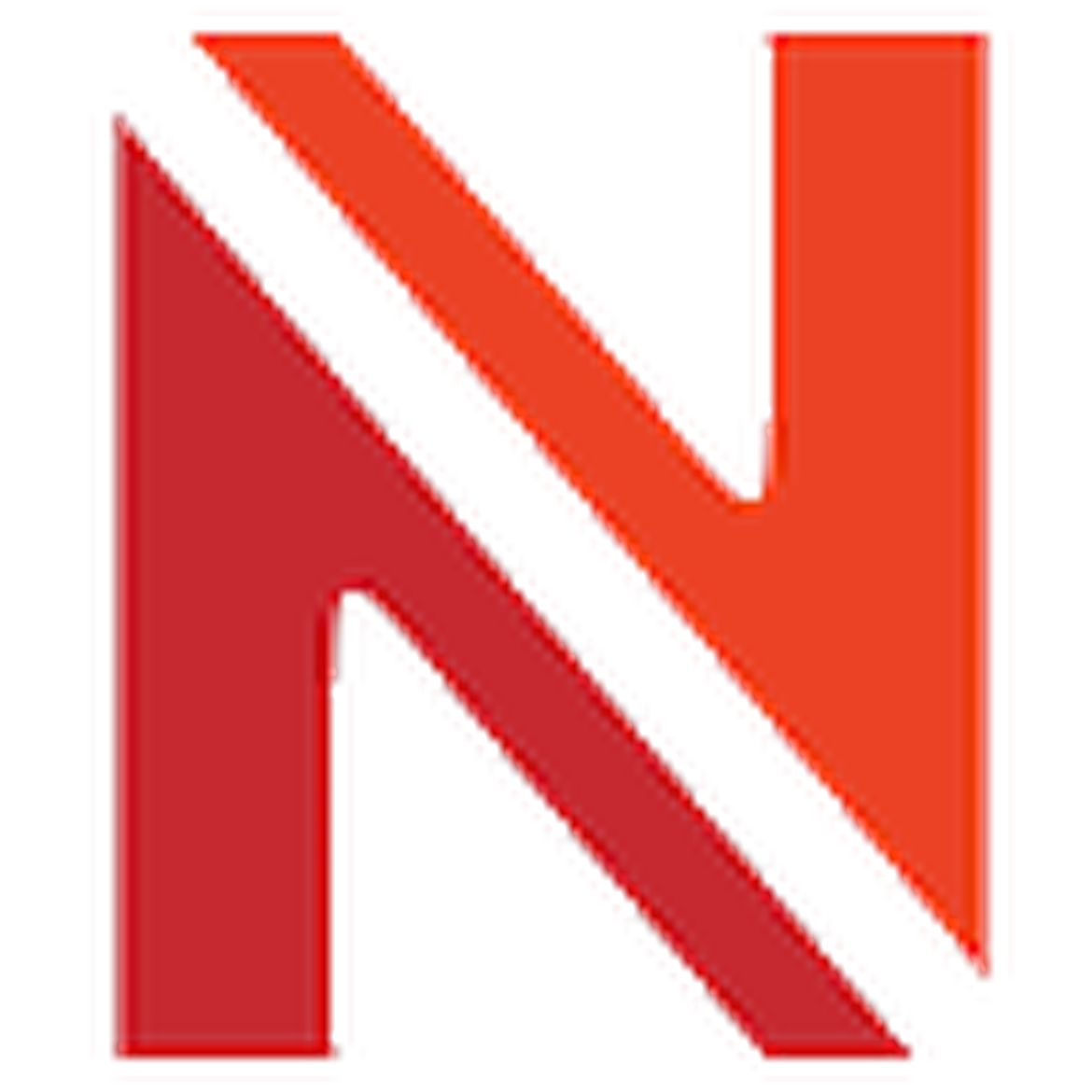
Nesting job is a list of parts with quantities for each type, which will be nested on plates from the same material grade, thickness and quality. A single nesting job is performed in a nesting project.
NESPERT CAM nests parts that are included in the Job, and the number of parts in it is the maximum allowable for nesting in the project.
Nesting Design
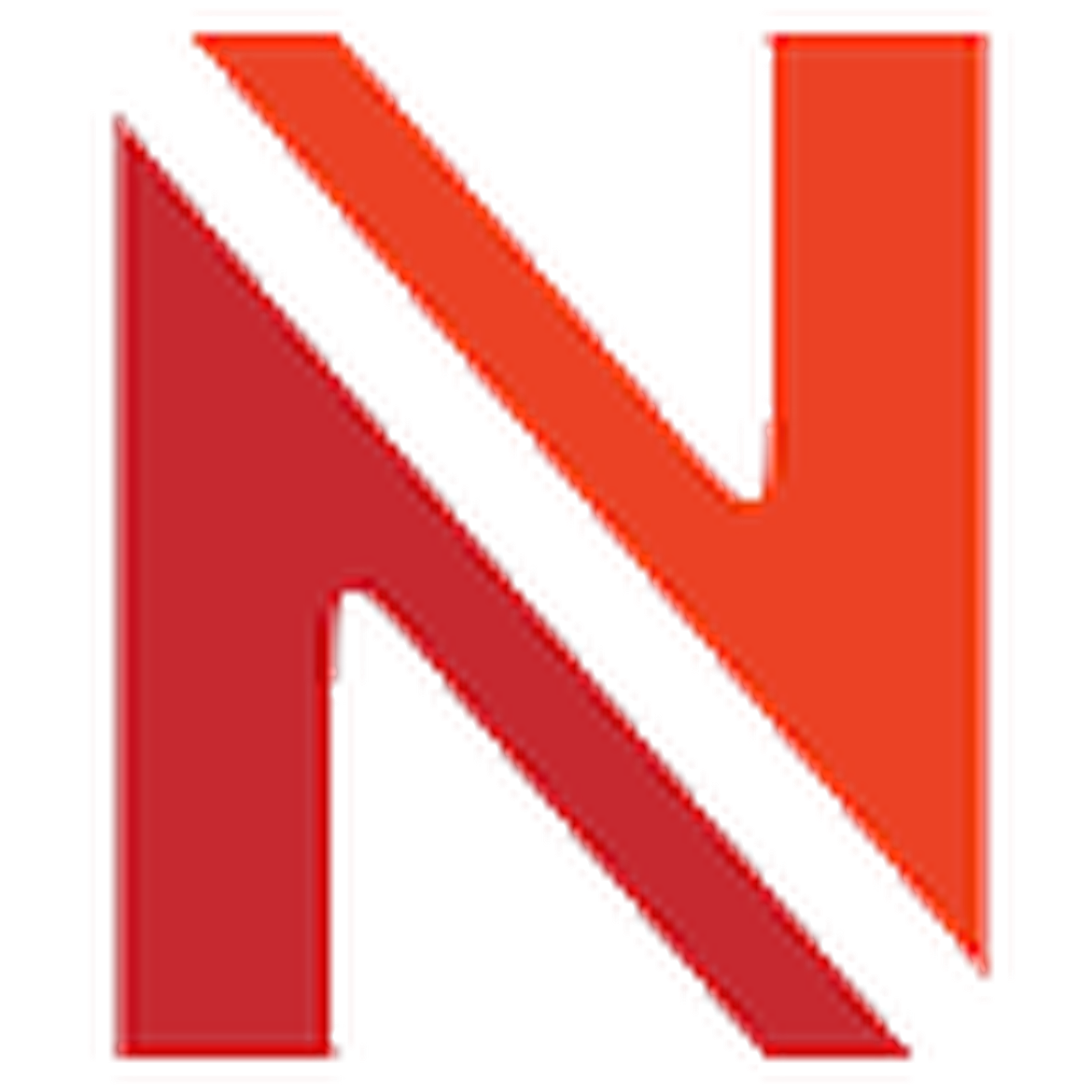
NESPERT CAM nests plane parts on plates.
The system creates a technology and NC programs for contour processing with cutting jet that may be thermal – laser, plasma oxy-fuel or water-jet.
NESPERT CAM programs:
- processing with vector or raster marking (engraving),
- processing with a torch whose cutting shape is a short segment with or without orientation,
- bevel cutting,
- drilling, boring of holes,
- milling of some types of contours.
NESPERT CAM does not nest and does not create a technology for coordinate punching.
The process of nesting design includes nesting preparation, nesting, creating a technology for processing and generating results.
Nesting preparation
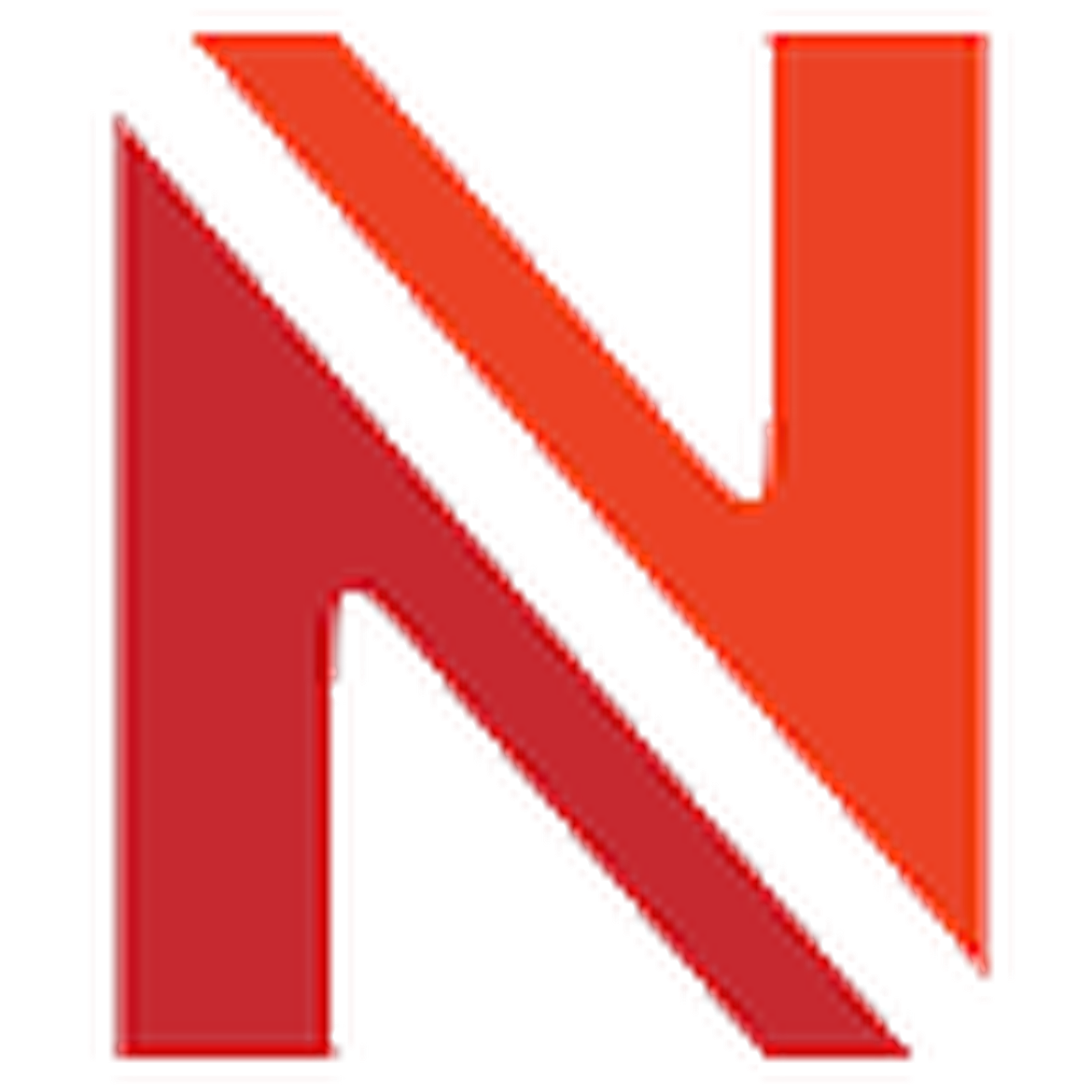
The nesting preparation in NESPERT CAM requires:
- choosing a machine from dataset,
- choosing a material grade from dataset,
- specifying material thickness,
- choosing a cutting station/carriage and processing regime from dataset,
- specifying plates on which the nesting will be performed,
- importing parts’ geometry,
- specifying a nesting job.
Project

The NESPERT CAM project is a system set of data, that follows the nesting process and allows saving and reading data to/from file. The project files in NESPERT CAM have extension RCAM.
The project provides tools for:
- nesting parts on plates and creating nesting layouts,
- applying a Processing technology based on the physical process of cutting,
- generating NC programs and processing documents,
- pricing and offering.
Plate

A plate is a planar plate with rectangular or custom shape, with a specified thickness, grade and material quality.
Multiple plates with the same thickness, grade and quality of the material can be used in a single NESPERT CAM project. Not only multiple identical plates can be used in the project, but also plates of various sizes and shapes.
Plate limit
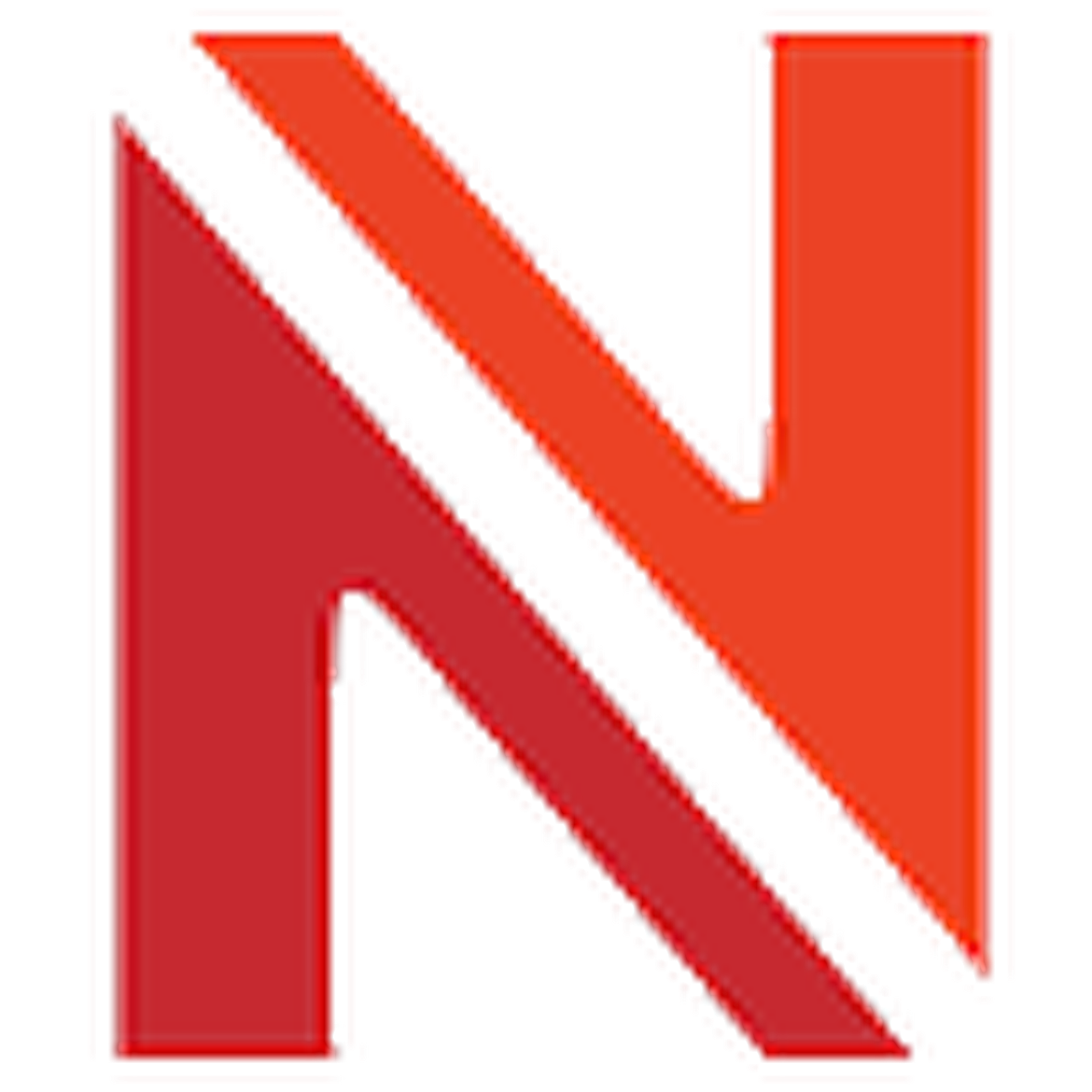
A limit is the maximum number of plates (quota) from the same dimension type and quality.
The value of the limit can be edited at any time during the work on the project.
Multiplicity
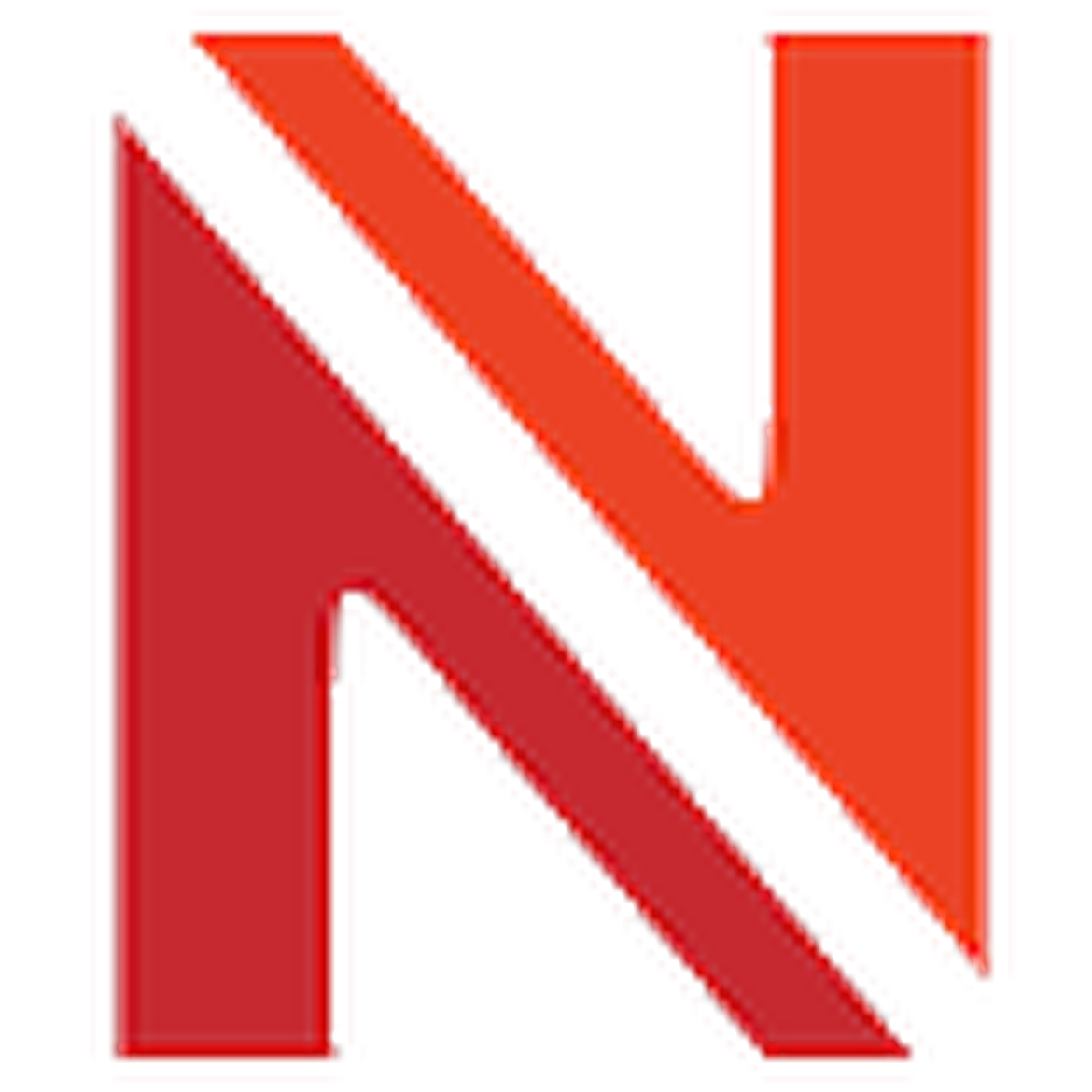
Multiplicity is the number of plates of a single nesting Layout.
The multiplicity of the plate is a parameter which enables designing true shape nesting in which a single NC program is used for cutting many times identical plates and the quantity of parts is controlled strictly by the Job.
Zone
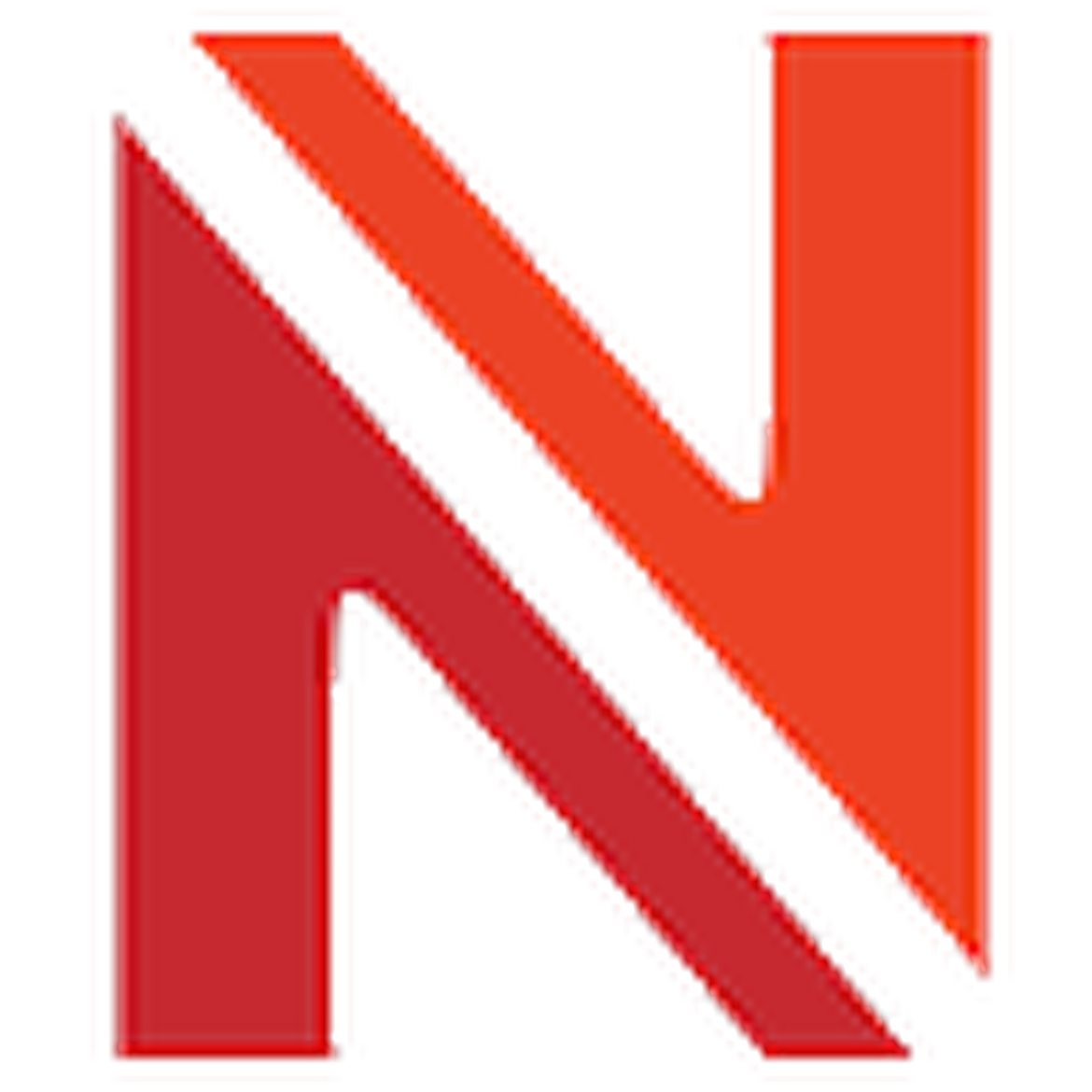
Zone is a rectangular area of a Plate, where nesting is performed. There can be many zones on a single plate, but only one of them can be active at a given moment.
A single Processing Technology is assigned for all zones of the plate. The Processing technology of the Zone is inherited from the Processing technology in the project, when the Zone is created.
The size and parameters of the Zone can be edited at any time.
Each Zone contains:
- nested blocks of parts, of cutting moves or block-matrixes,
- cutting paths,
- route of rapid moves.
The Zone can be for a single torch or parallel – for work with parallel torches.
Parallel zones
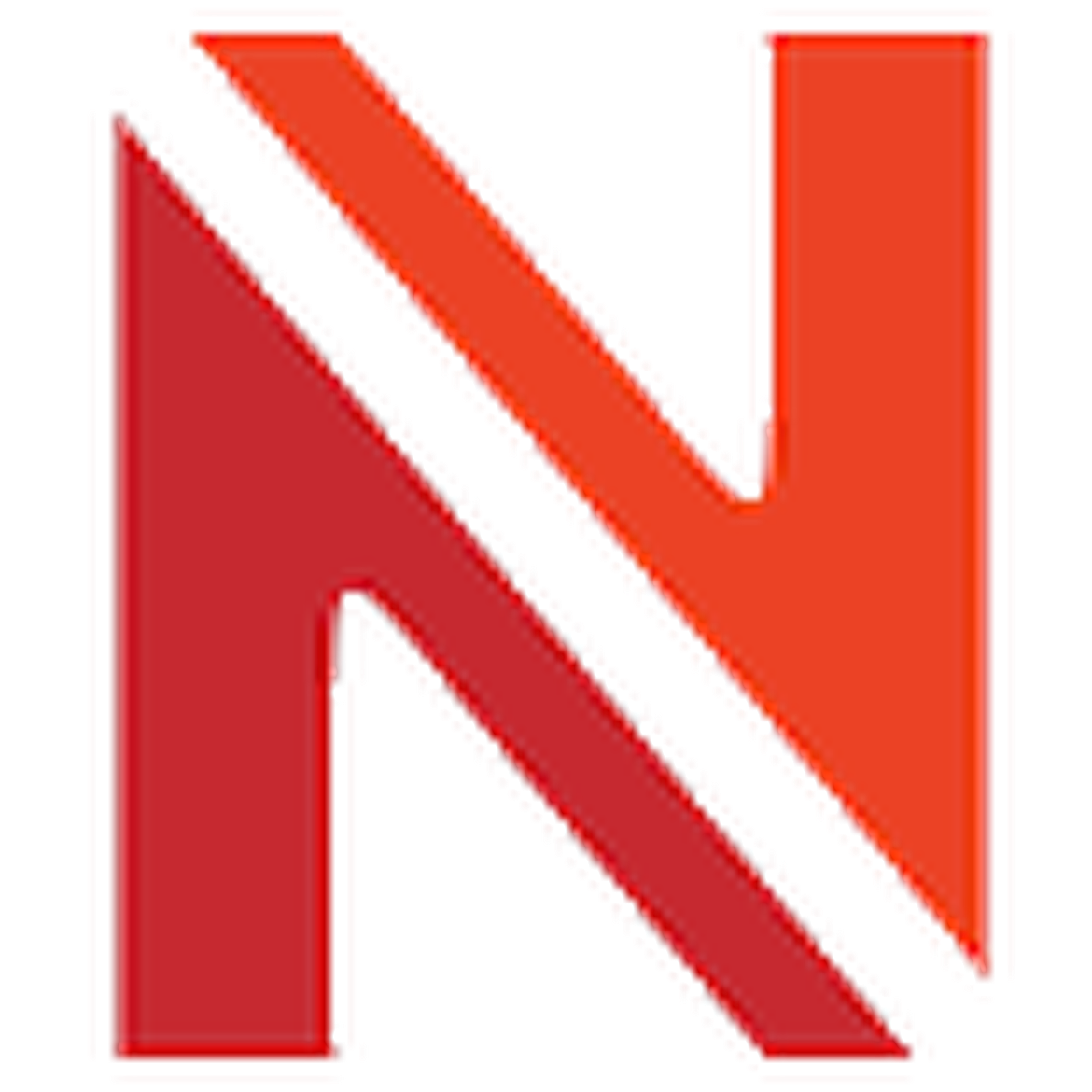
Parallel zones are two or more zones, which are processed at the same time with parallel working torches. The torches perform identical or mirrored movements along X (or Y) axis, if the used machine allows mirroring.
NESPERT CAM creates NC programs for two or more parallel working torches, that are on a certain distance from one another, when the CNC machine does not have the functionality to position the parallel torches by a program.
When the CNC machine is able to control turn-on/turn-off and position each of the parallel cutters by a program, NESPERT CAM is able to create nesting layouts by АМТ (Advanced Multi Torch) technology – with variable number and distance between the torches.
Block
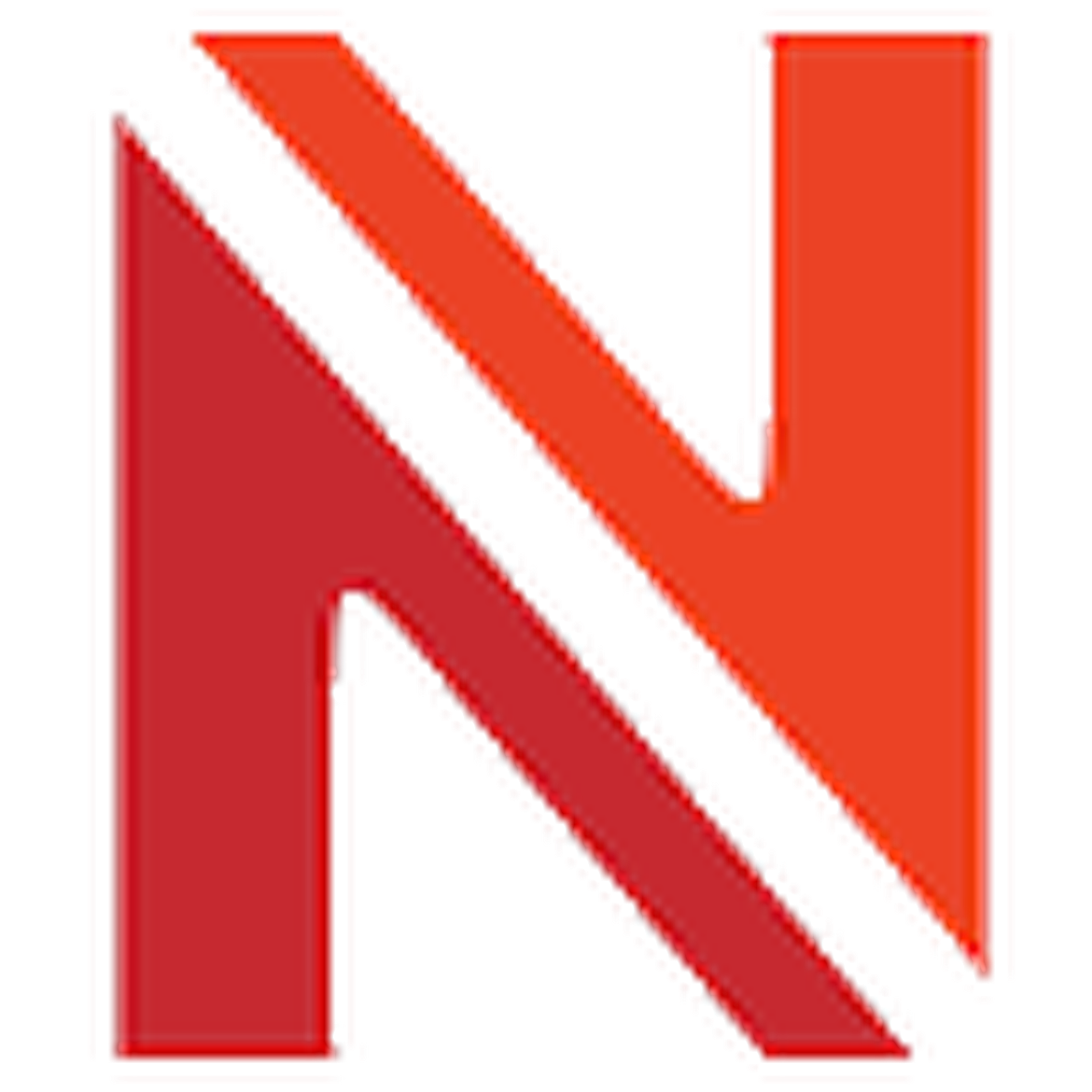
NESPERT CAM automatically or interactively creates blocks as a named arrangement of parts with their envelopes and/or blocks, with or without paths and markings, with or without rapid moves. The block can contain multiple blocks, and the nesting levels of the blocks are unlimited.
Each block can be edited before and after nesting.
Nesting queue
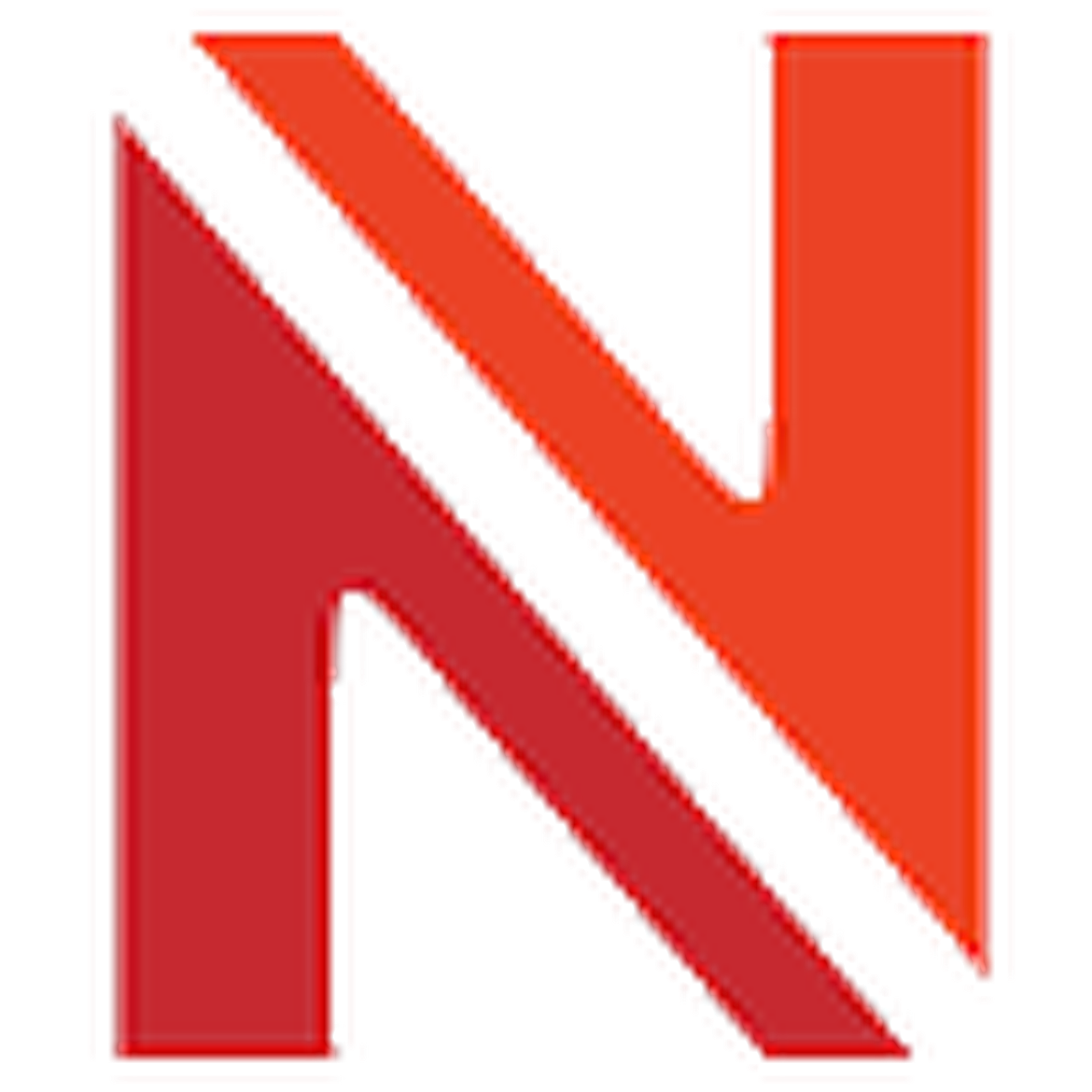
The nesting order of the blocks in NESPERT CAM is specified in a queue. A nesting method and criteria for controlling the nesting algorithm are specified for each block.
The nesting Queue can be created automatically. Blocks can be added at any time.
NESPERT CAM nests by the selected method for each block in the Queue. After a block is nested, the number of the parts of each type, that remain for nesting, is calculated. The nesting of each block type continues until the quantity is exhausted.
Since there can be a custom number of parts in a block, and the Queue controls the number of the nested blocks, in order to achieve accurate control of the quantities, NESPERT CAM precisely controls not only the nesting process but also the creation of the Queue.
Nesting layout
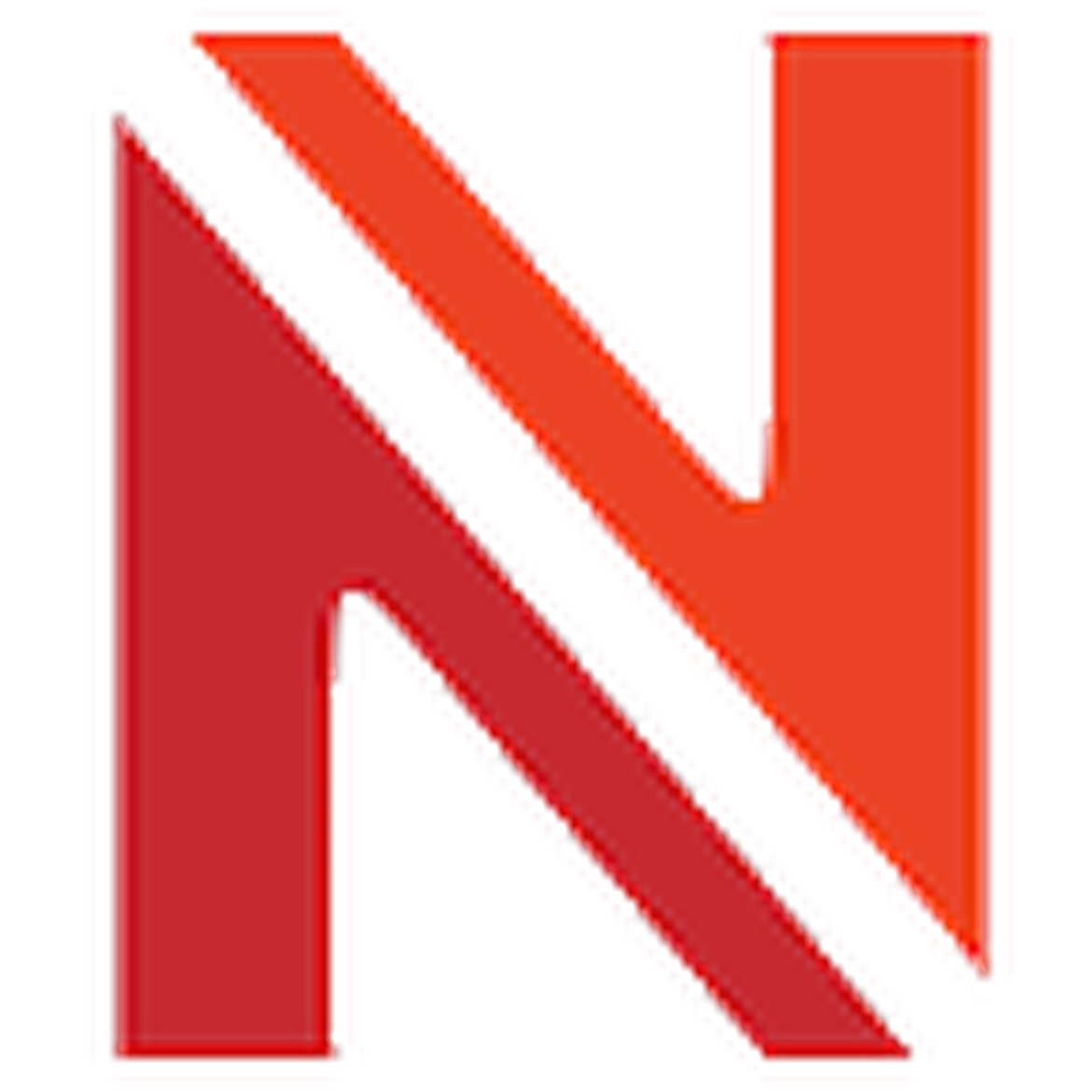
The nesting layout is the main result of the true shape nesting with NESPERT CAM.
It accurately and completely visualizes the sequence of processing. The nesting layout includes information about the plate, parts, paths with directions, rapid moves, turn-on and turn-off points, other path elements.
Using the nesting layouts the system generates NC programs, reports and valuation documents.
Sequence of creating nesting and processing technology
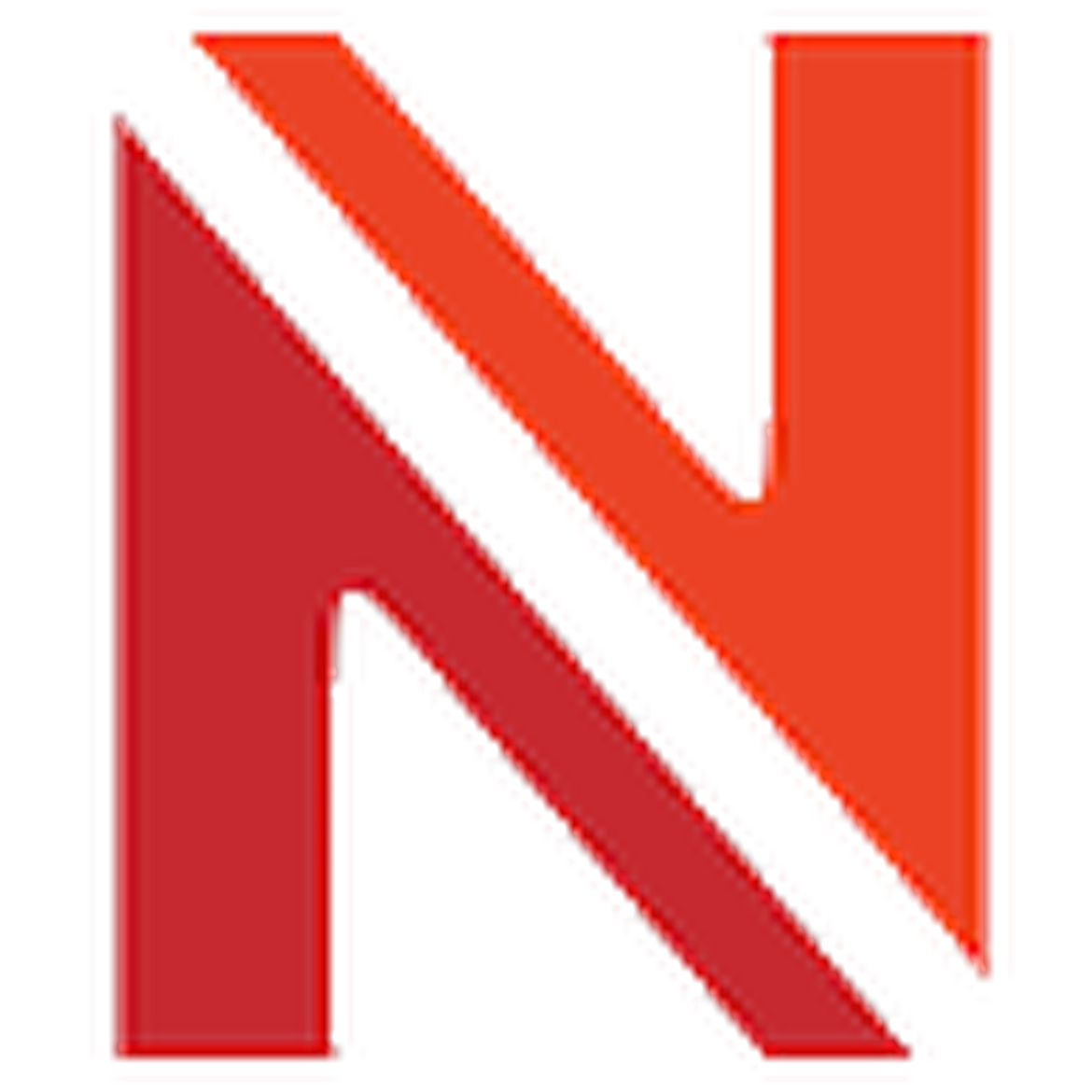
There is no requirement on a compulsory sequence of creating a technology for processing of parts and for nesting in NESPERT CAM.
The user can nest parts:
- only with contours, without processing technology,
- with partial technology,
- with partial or fully complete paths and without route,
- with paths and partial routes,
- with complete technology,
- with paths and route.
Nesting
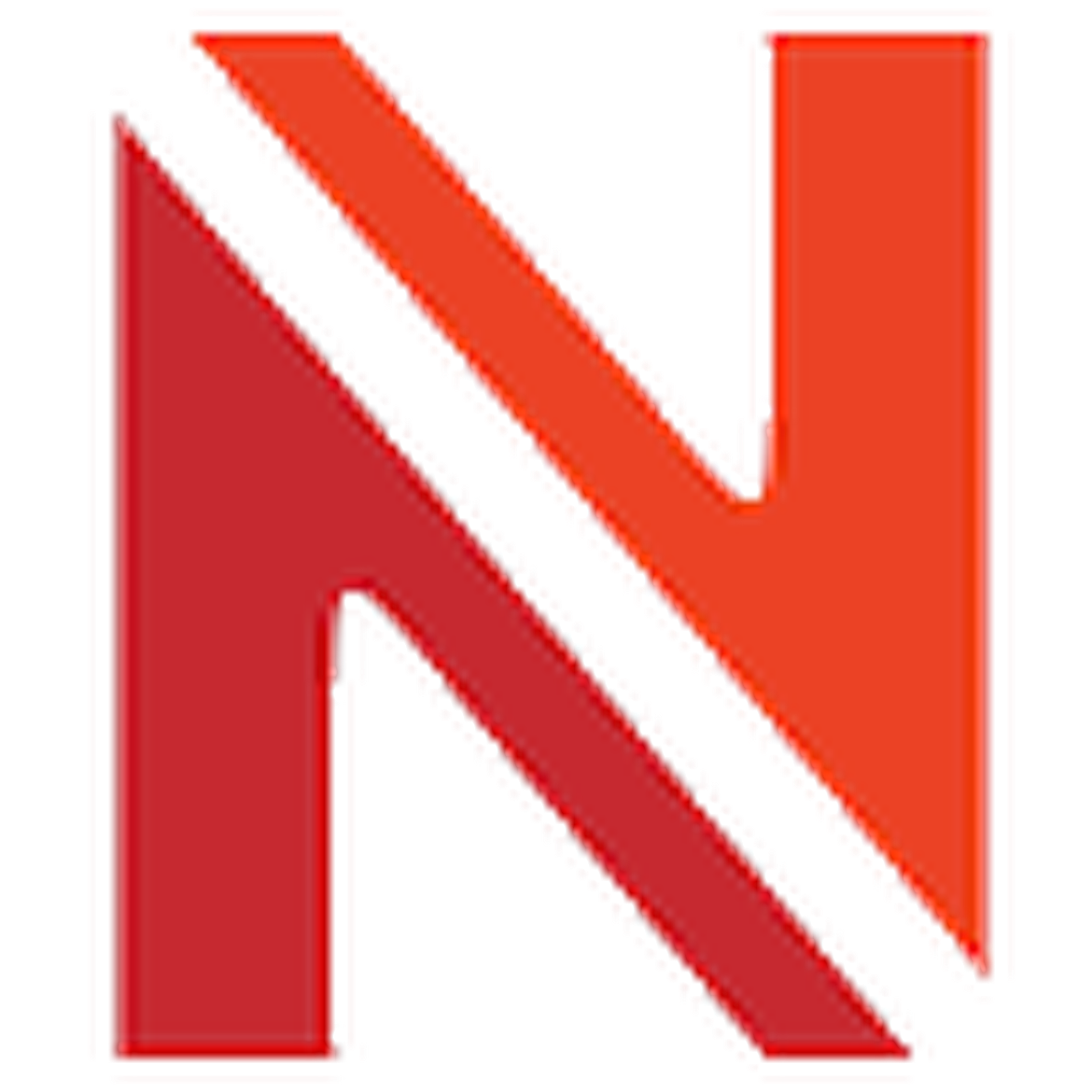
NESPERT CAM automatically and interactively nests. The manual nesting is possible as an exception.
NESPERT CAM step-by-step and tightly nests plane objects on plates with on-line control against overlapping and interface for control of the nesting process.
The objects can be single parts or groups of nested parts – blocks.
Automatic nesting
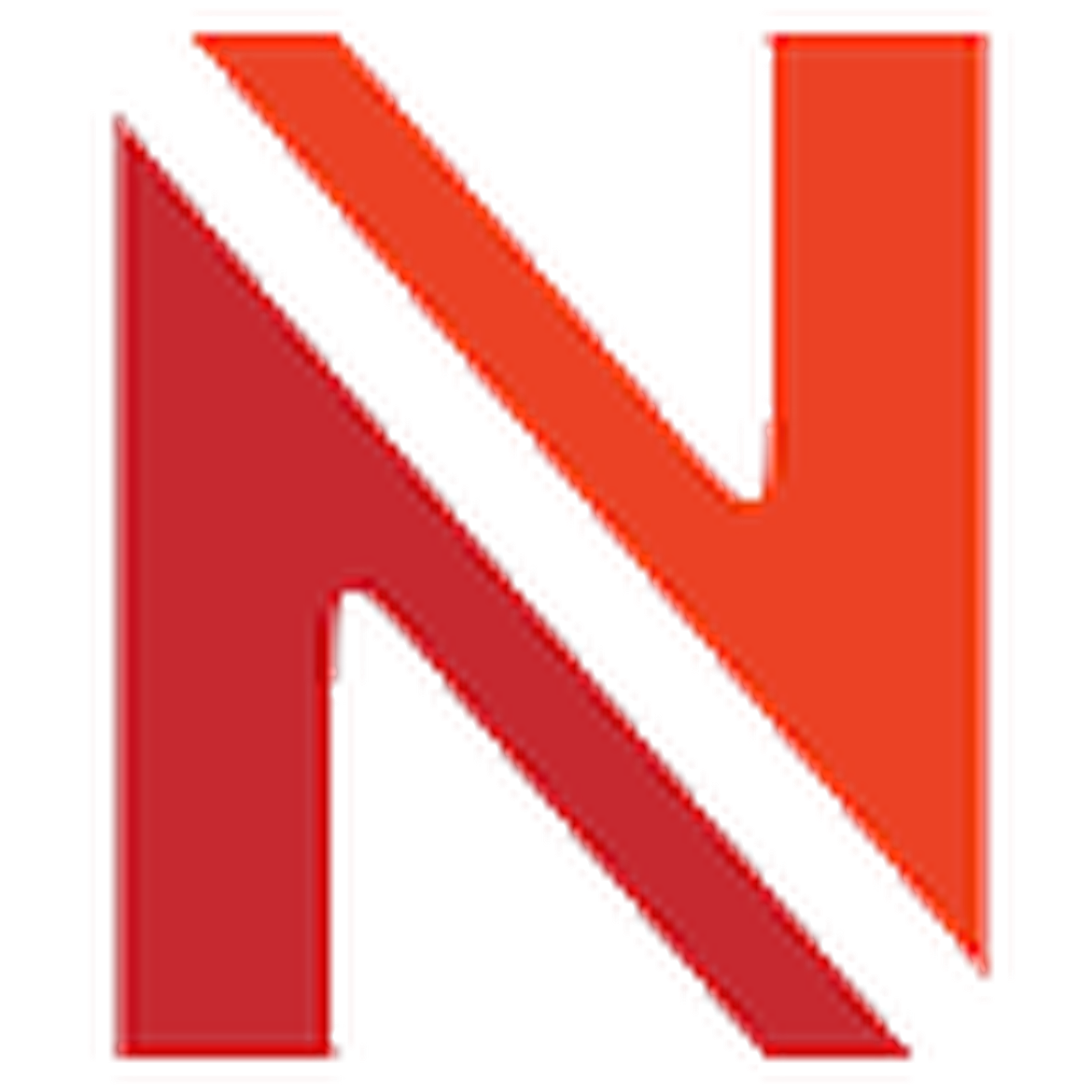
NESPERT CAM automatically nests and calculates the possible places of the given orientation of the nesting object, optimises and finds place on the plate. The system nests the object tightly to other already nested objects.
NESPERT CAM performs on-line control against overlapping all the time to avoid placing an object on other already nested objects.
The sequence of the objects for automatic nesting is specified in the nesting Queue. The quantities of the objects for nesting is calculated according to the quantities of the parts, specified in the nesting Job.
The automatic nesting can be performed on single or multiple plates, until the plate limit (the number of the permitted plates by type) or the parts in the Job are expended.
After nesting each object it is possible to interrupt the automatic nesting, then perform interactive functions and continue with the automatic nesting after that.
Interactive nesting
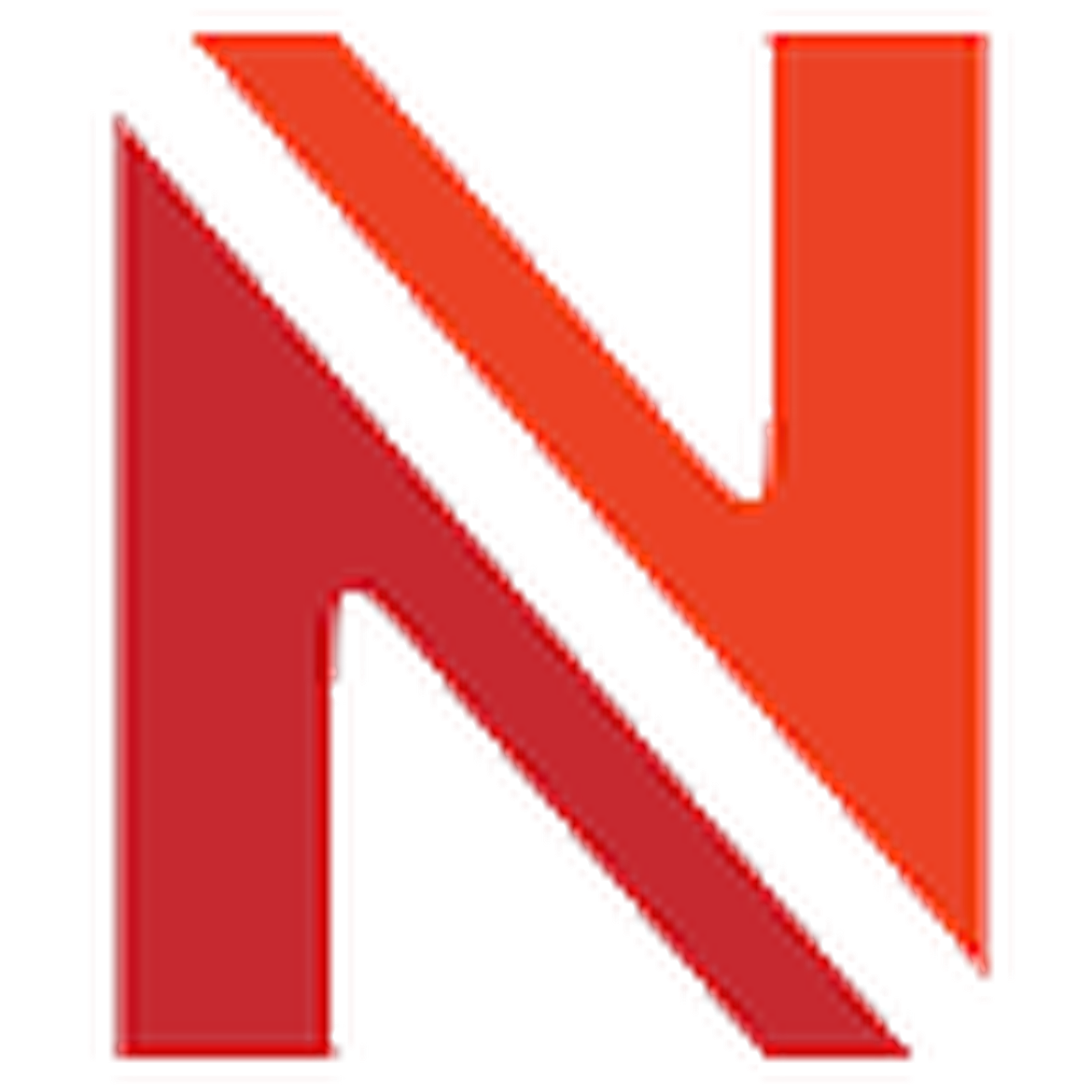
In interactive nesting the user selects an object, nested on a plate or in the nesting Queue. The selected object appears under the mouse cursor and can be dragged, pushed and rotated near the desired location on the plate.
After clicking the right mouse button NESPERT CAM nests the object tightly to the already nested objects. The system performs on-line control against overlapping and does not allow nesting the object over already nested objects.
Matrix nesting
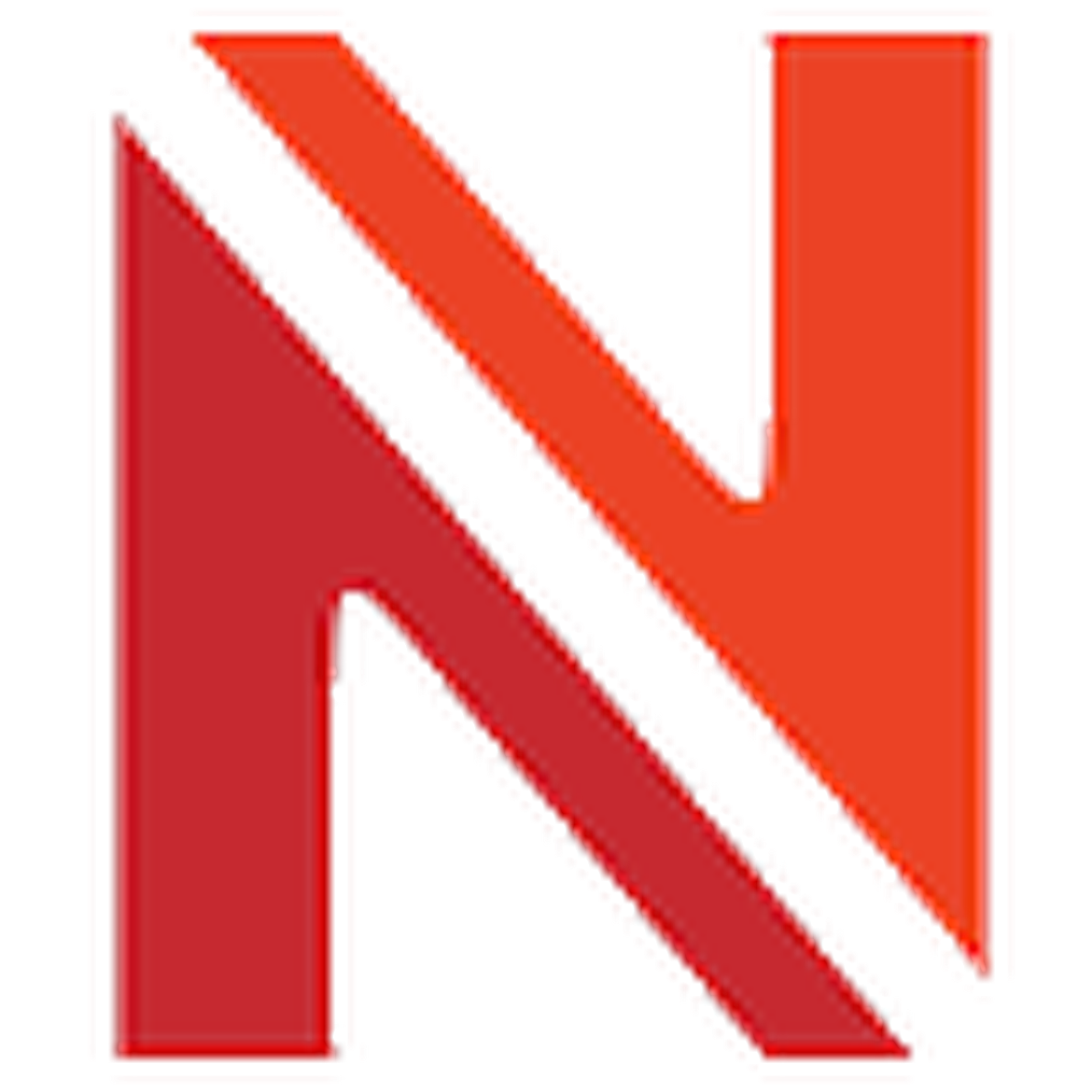
The matrix (regular) nesting is a version of the interactive nesting where the user chooses object - part or group of nested parts and specifies the number of lines and columns where the object is to be nested. The matrix of parts that is created appears under the mouse cursor and can be dragged and rotated with the instruments for interactive nesting. After finishing the function the system removes those matrix objects that overlap the already nested objects and nest the ones for which there is place.
Manual nesting
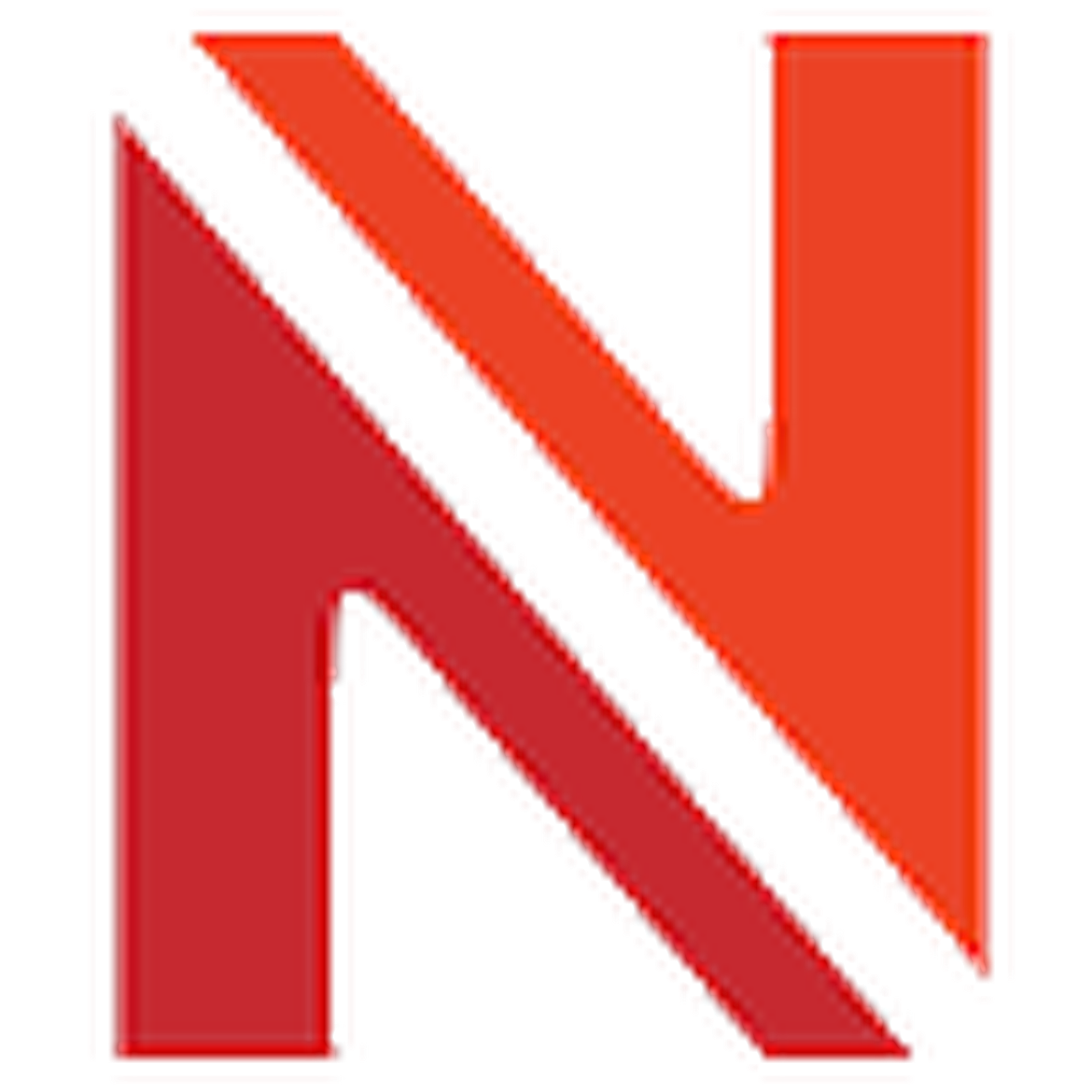
The manual nesting is to deliberately disable the on-line control against overlapping and to drop the object on the location on the plate under the mouse cursor. The manually nested objects can be outside the plate limits or can overlap already nested objects on the plate.
True shape nesting technology
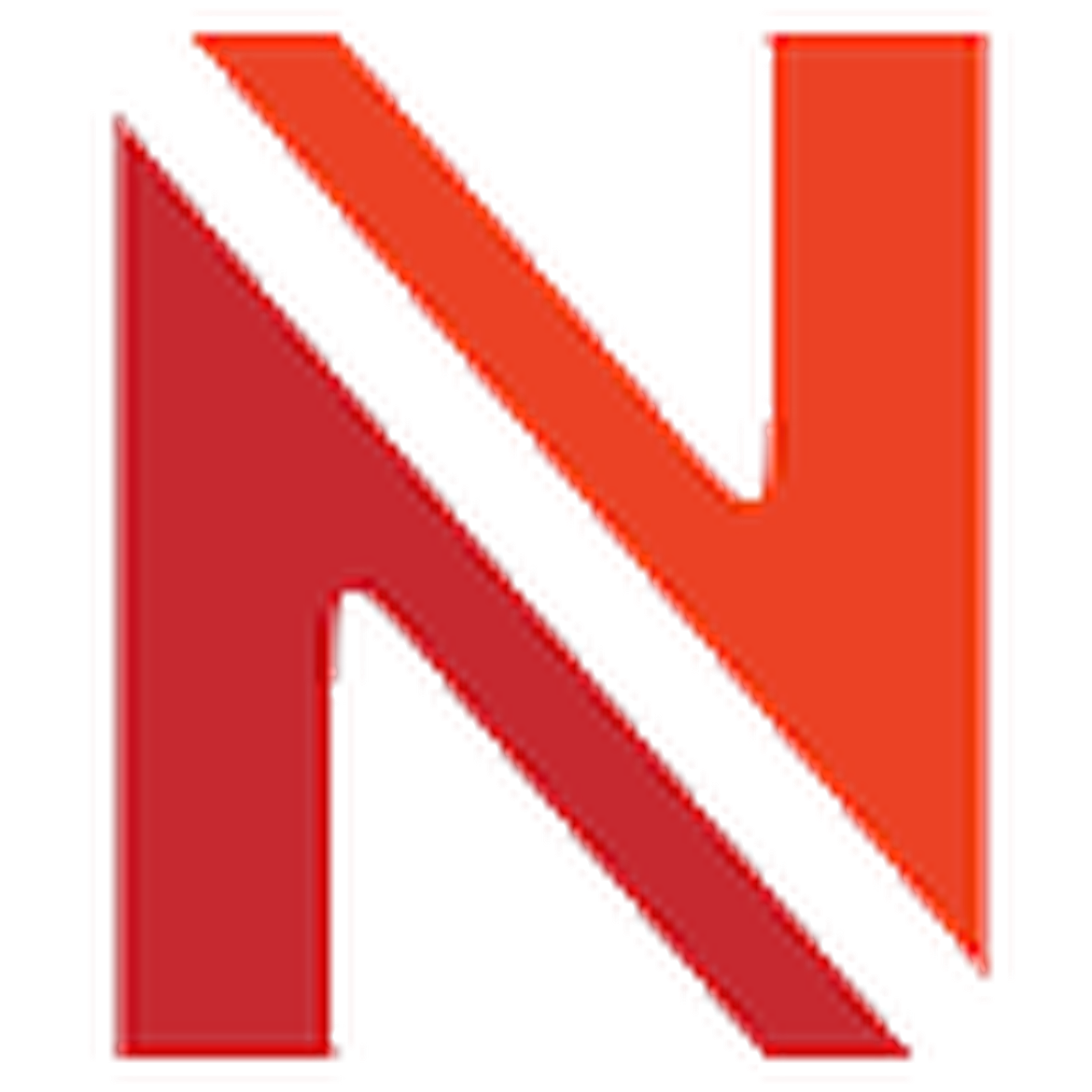
The true shape nesting technology is determined by the ongoing physical and chemical processes inside the cut, by the type and thickness of the material and by the type of the processed contour.
Each type of thermal and jet cutting – laser, plasma, oxy-fuel, water-jet, has its own specifics and requirements.
The true shape nesting technology is determined by the cutting path, the cutting/nesting regime, the set of path elements for each path or group of paths, rapid moves, specifying the sequence for processing the paths and the specific groups of preliminary-final set of commands for each machine.
Technological Datasets Base (TDB)
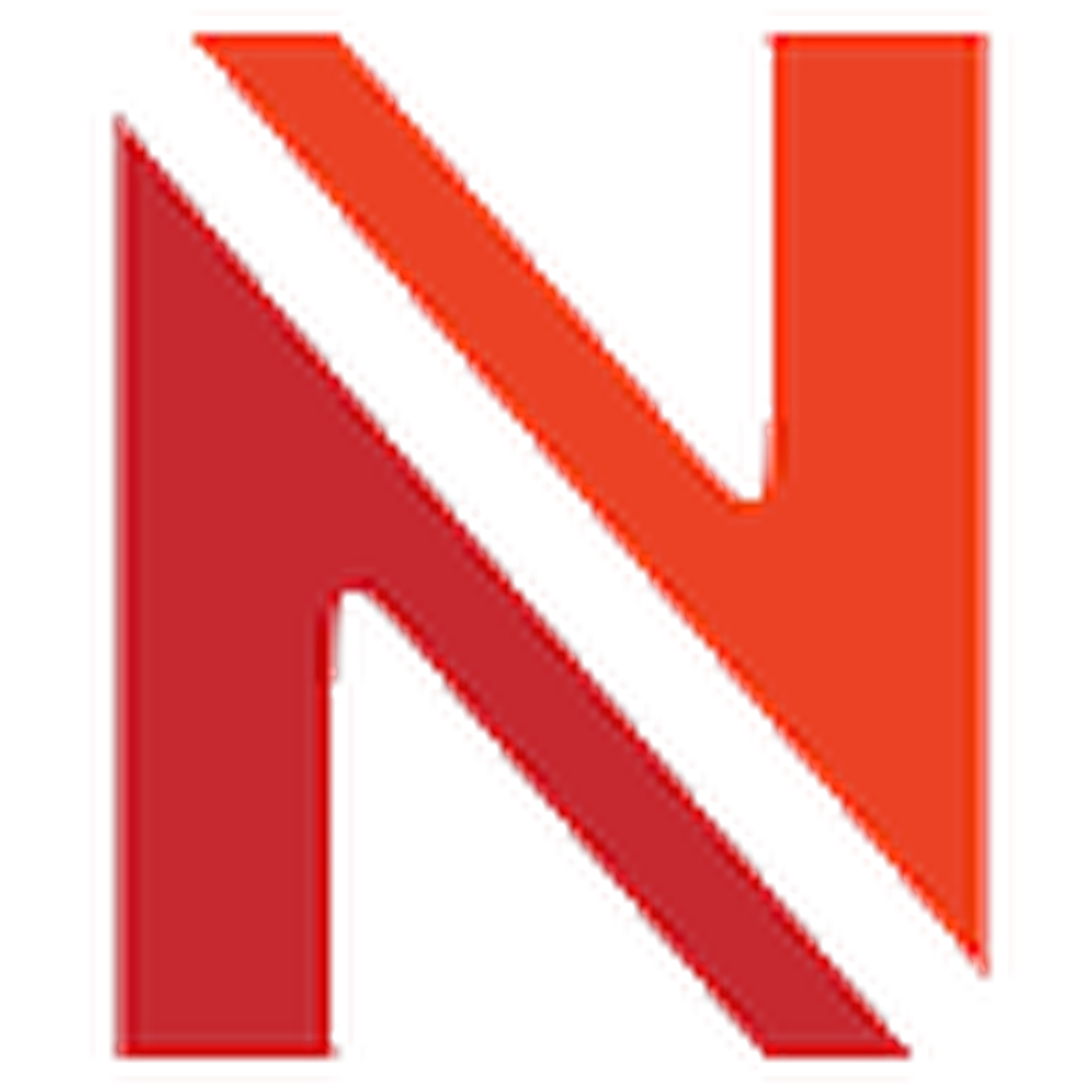
NESPERT CAM supports the specific technology knowledge as tabular rules in datasets, stored in the SQL database of the system, called Technological Datasets Base (TDB).
The system uses TDB to determine what Processing technology to implement on the nesting layouts in the project. The user can always change a technological parameter, assigned by the system.
Route
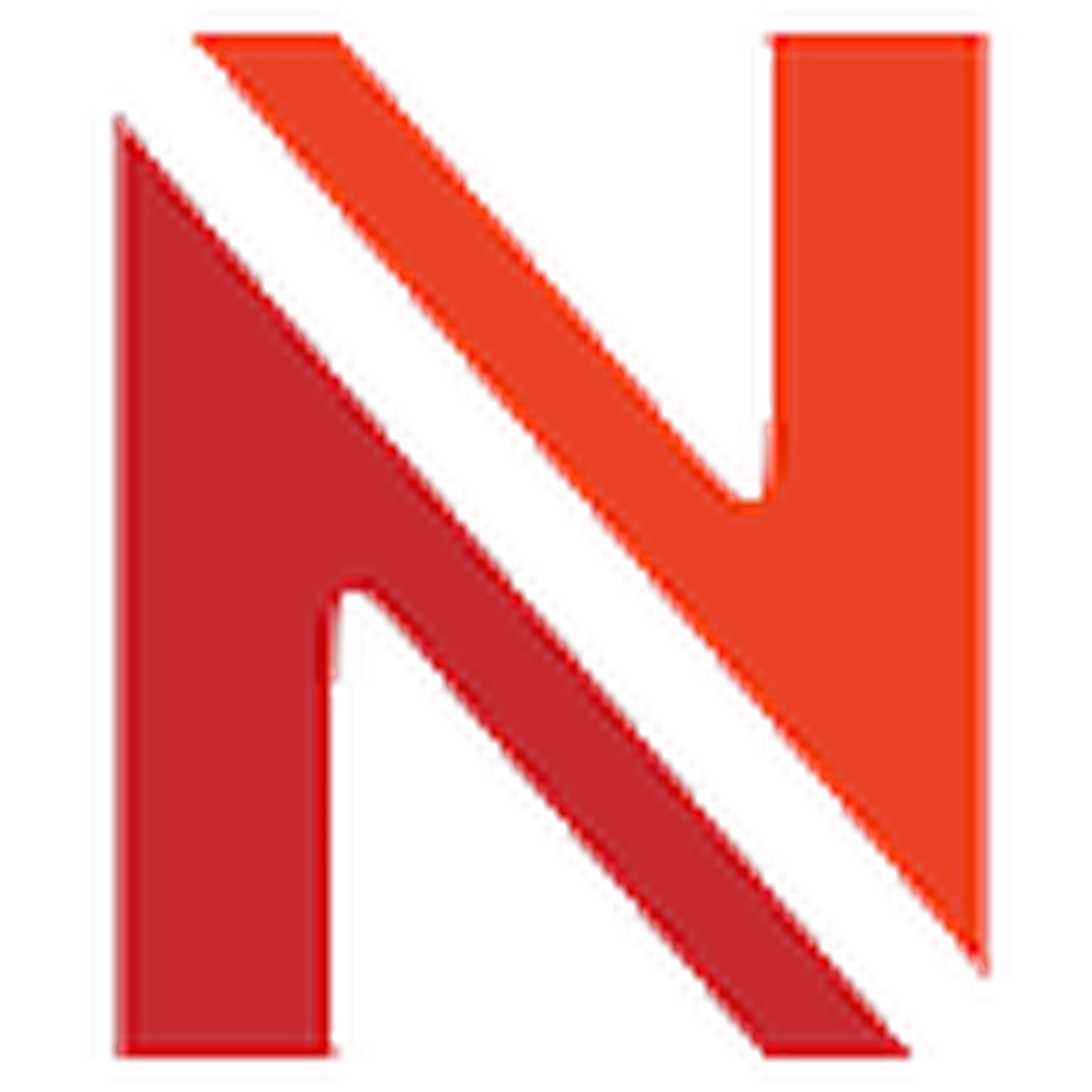
The route is a sequence of rapid moves between Lead-ins and Lead-outs of paths.
The route of rapid moves defines the processing sequence of paths. The rapid moves exist only as connecting objects between the separate paths. When a path is deleted, the rapid moves, connecting it with the nearby paths, are deleted too.
NESPERT CAM automatically classifies the rapid moves as inner, outer and short.
The system creates a route automatically or interactively.
Automatically a route is created in accordance with specified parameters and optimization of the minimal length of the rapid moves.
Interactively the route connects start and end points of paths that are near the cursor. Each move of the route can be selected, deleted or transformed by the user. There is a complete set of functions developed in the system for interactive work with routes.
A route, which connects all paths in the Zone is called a full route. A sequence of rapid moves for a part of the paths is called а partial route. Each partial route can be finished using the functions for automatic or interactive route.
A selected rapid move of a route can be converted to a rapid move without turn-off, rapid move with tracking, chain-cut with circumventing or chain line. A route can be automatically analysed and transformed to a route with circumventing of the cut areas of the plate.
Route optimisation
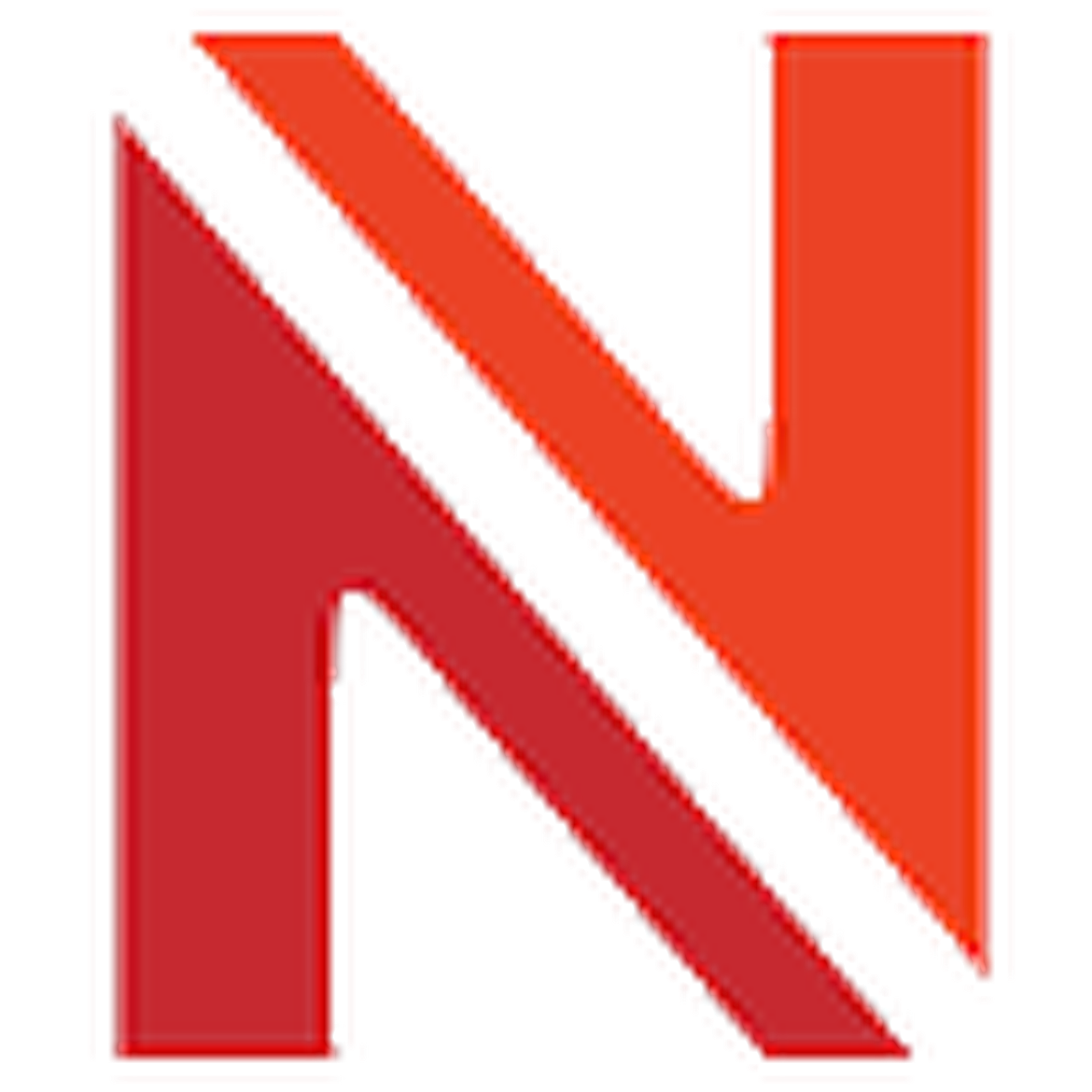
NESPERT CAM automatically or interactively creates route of rapid moves. The system allows working with partial routes. When creating a route the system minimizes the route length taking into account constraints such as part-by-part and part-in-part nesting. The control for part-by-part and part-in-part nesting can be disabled.
Part-in-part nesting
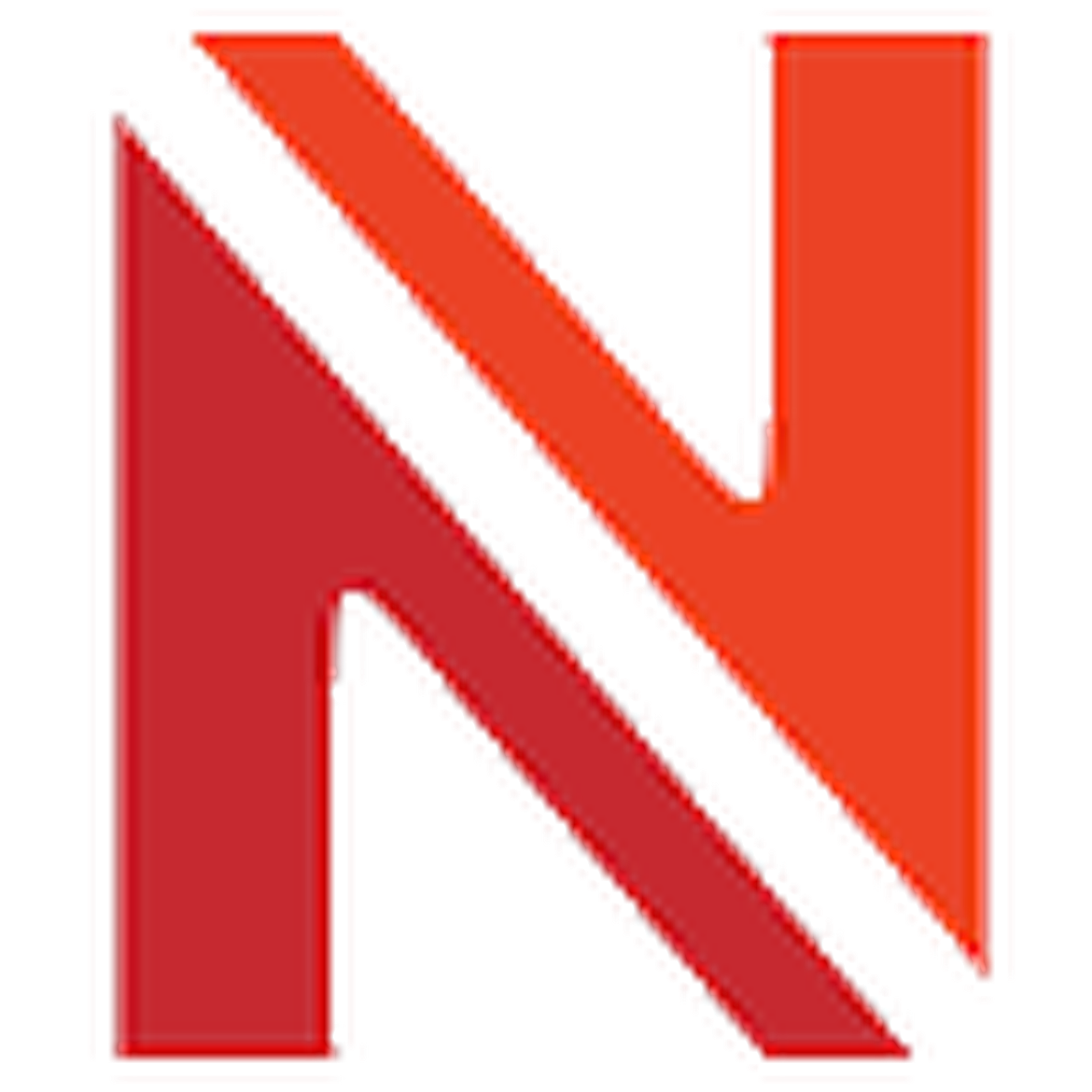
The part-in-part nesting is a characteristic of NESPERT CAM for nesting a part in the hole of another part.
The nesting levels in the system are unlimited.
NESPERT CAM automatically programs the processing of the nested contour before the one enclosing it.
Regime
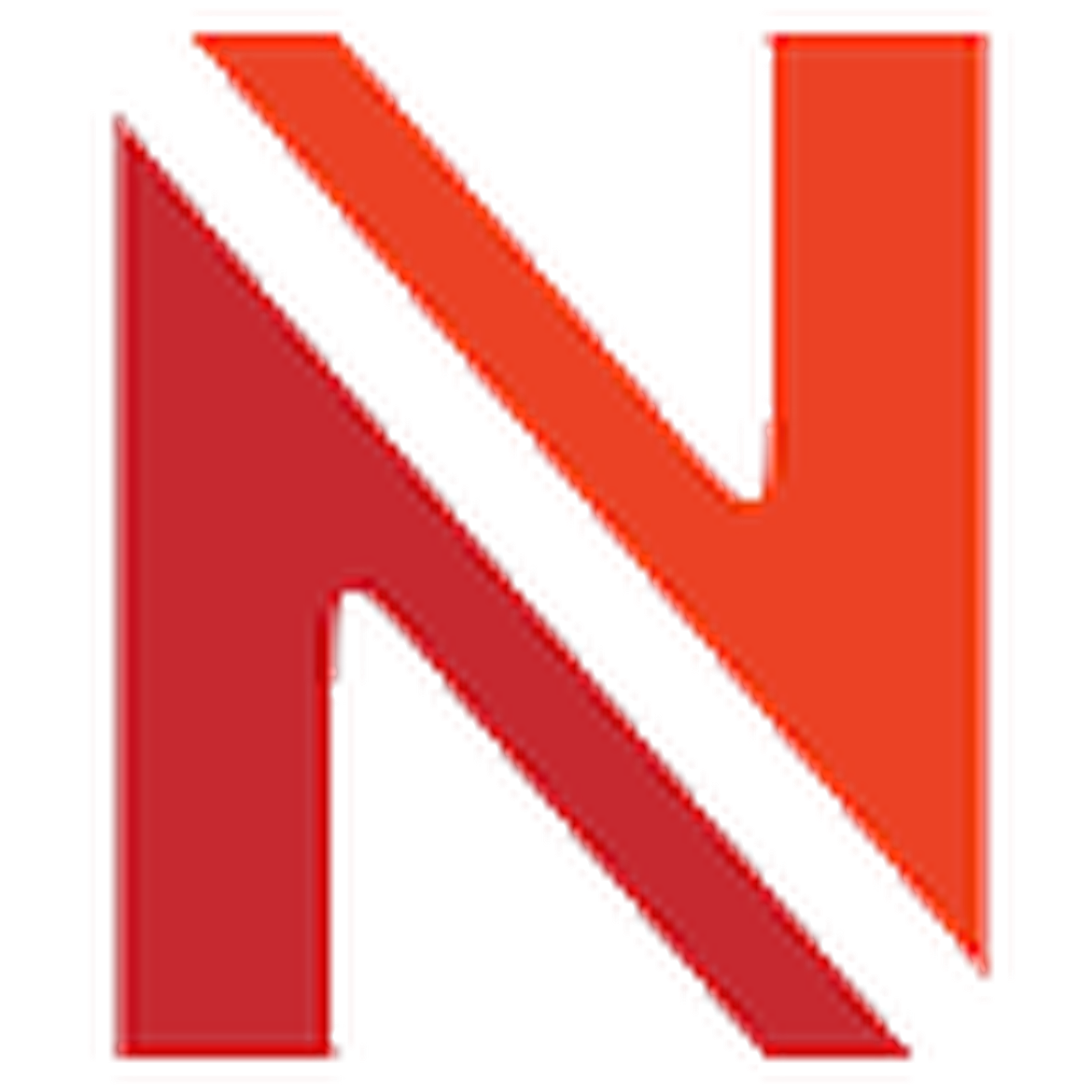
The regime of processing is determined according to the requirements of the energy source, the path type, the thickness and the type of the material, the used torches and gases for thermal cutting. The regimes of the thermal cutting are recommendatory or obligatory. Observing the cutting regimes, specified by the manufacturer, generally is a prerequisite for obtaining quality of the processed parts and for effective usage of the energy and the materials, and in some cases – for failure free work of the machine and a prerequisite for maintaining the equipment guarantee.
NESPERT CAM has full functionality for assigning and setting the cutting regimes. The parameters of the cutting regime are defined in the Technological Dataset Bases and are part of the Processing Technology.
Cutting diameter (kerf)
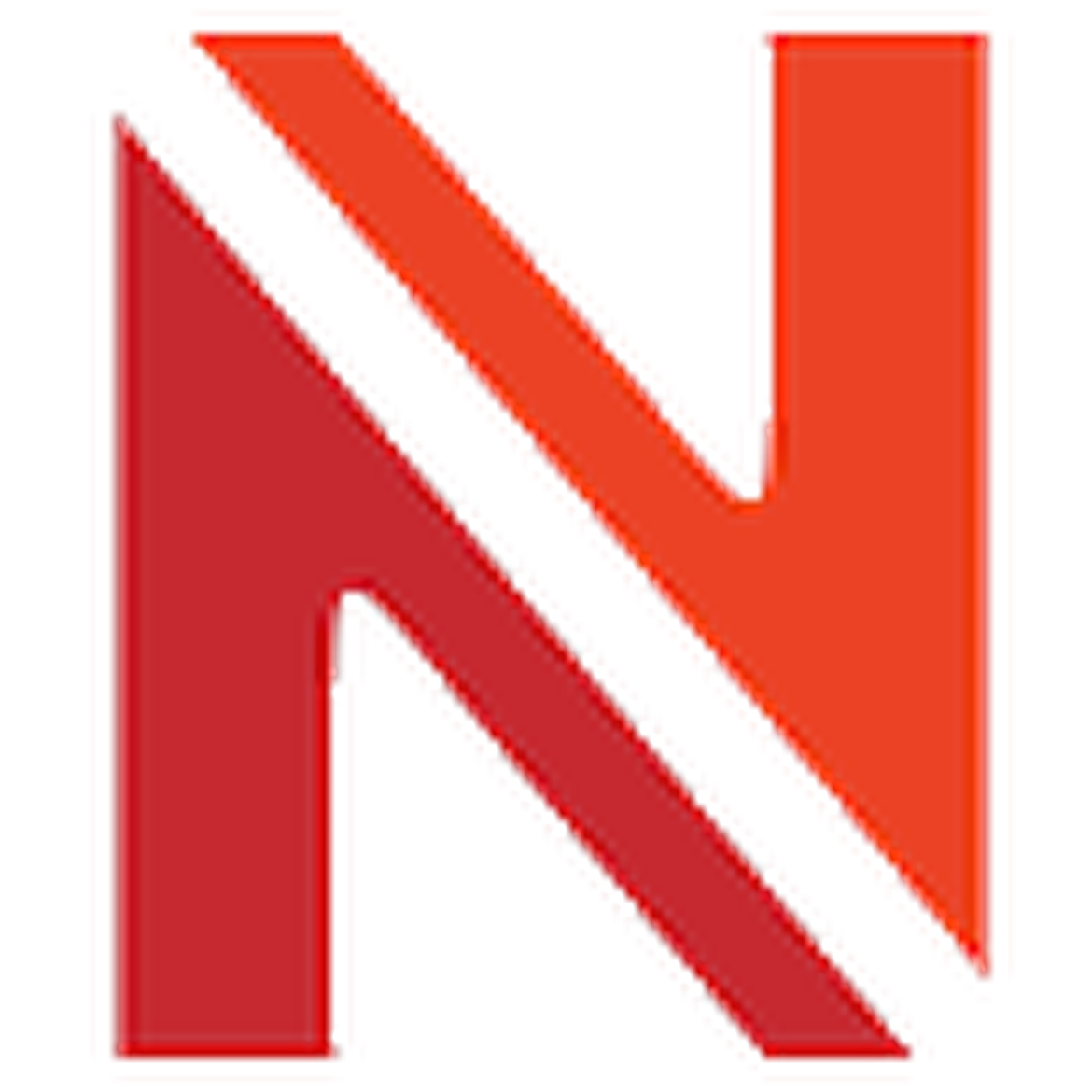
The cutting diameter is a basic parameter for accuracy of the dimensions in NESPERT CAM and there are three options for its controlling:
1. Cutting diameter = 0 and generating commands for non-equidistant programming. NESPERT CAM generates nesting paths on the contours of the parts, with NC commands for control of the equidistant offset of the torch, and the equidistant correction ½ of the cutting diameter is set in the respective register of the CNC system.
2. NESPERT CAM creates paths that are equidistantly offset in relation to the contours of the part to ½ of the cutting diameter, includes NC commands for controlling the equidistant offset and sets a correction of ½ of the error in the sizes in the respective register of the CNC system. When the cutting diameter is set with adequate tolerance in NESPERT CAM the value of the correction = 0 in the CNC system.
3. NESPERT CAM creates paths that are equidistantly offset to ½ of the cutting diameter in relation to the contours of the part and disabled kerf programming. In this way the precision of the dimensions is controlled only by the CAM system.
The choice of a control method of the cutting precision is defined as per the capabilities of the CNC machine and the approved manufacturing practice for providing accurate machining.
The parameters for controlling the cutting diameter are a part of the Processing technology in the CAM system.
Envelope
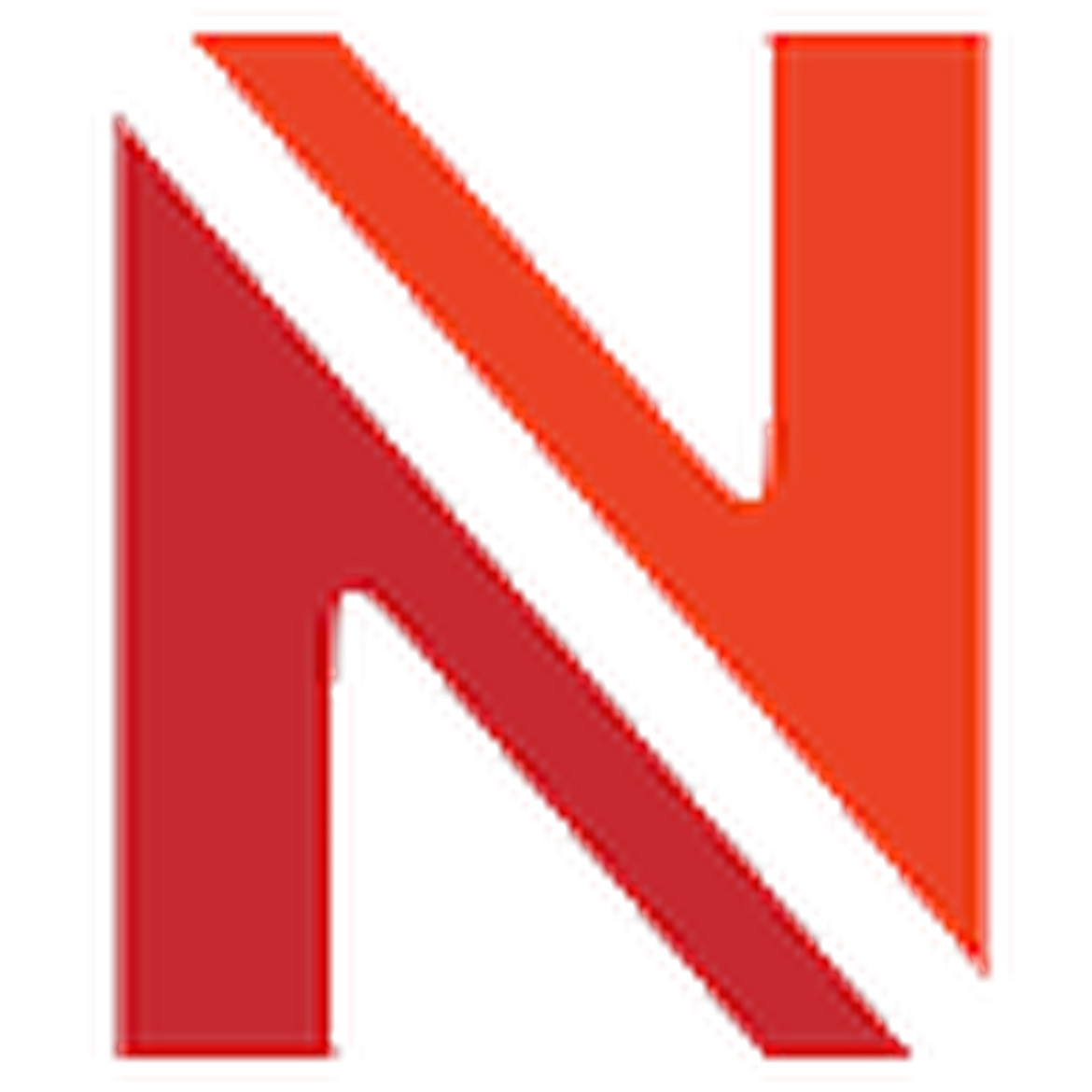
The envelope is a part of each block. It is a safety area around the part, which is automatically added not only to the outer contour, but also to holes and slots.
The envelope is designed for ensuring the opportunity for creating cutting paths of the part.
- The envelope is limited by a closed linear contour that is offset at least at a specified distance from the contour of the part,
- The envelope of the circular arcs are approximated with segments. The approximation error is in direction away from the material.
The term „envelope diameter“ is used instead of „specified distance“ in NESPERT CAM. The distance between adjacent parts and between a part and the plate border is defined by the envelope diameter.
Two adjacent parts are placed at a distance of at least 2 * the envelope diameter, and towards the plate border – at one “envelope diameter”.
Path
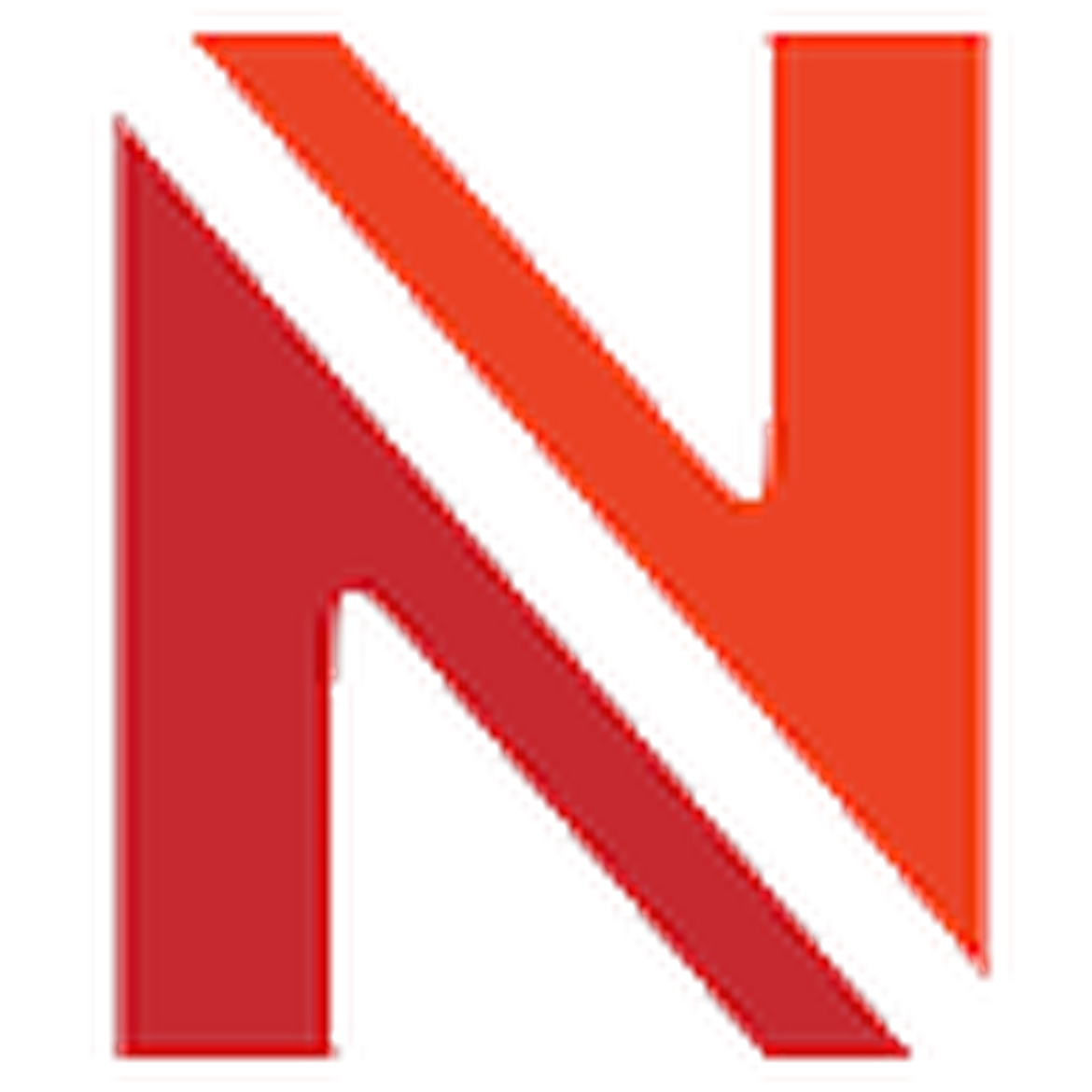
NESPERT CAM creates a path as a sequence of cutting moves of the centre of the torch for processing a contour.
The path consists of: pierce point, lead-in, cutting moves along a contour, optional path elements, cutting gap, lead-out, turn-off point. The path has a direction – from the pierce point to the turn-off point.
The path is equidistantly offset from the processed contour. The offset direction is defined automatically according to the type of the part's contour. The offset size is set in the Processing technology.
The path type is determined automatically by the type of the geometry of the contour: outer, open, inner, marking. The path can be: outer, open, marking, inner (any big hole), small holes 1.group (the smallest holes), small holes 2.group, small holes 3.group. Each path type has its own parameters, determined in the Processing technology, depending on the technological environment and the material.
The path can be created interactively or automatically. In both cases NESPERT CAM performs on-line control against overlapping of the path with itself or with already nested objects. When the system does not find a place to build the path elements with the values of the parameters specified in the Processing technology, while creating or editing a path, the path is not created on the contour. The user can change the parameters and to create again the remaining paths.
All parameters of a Path can be edited at any time.
Path optimisation
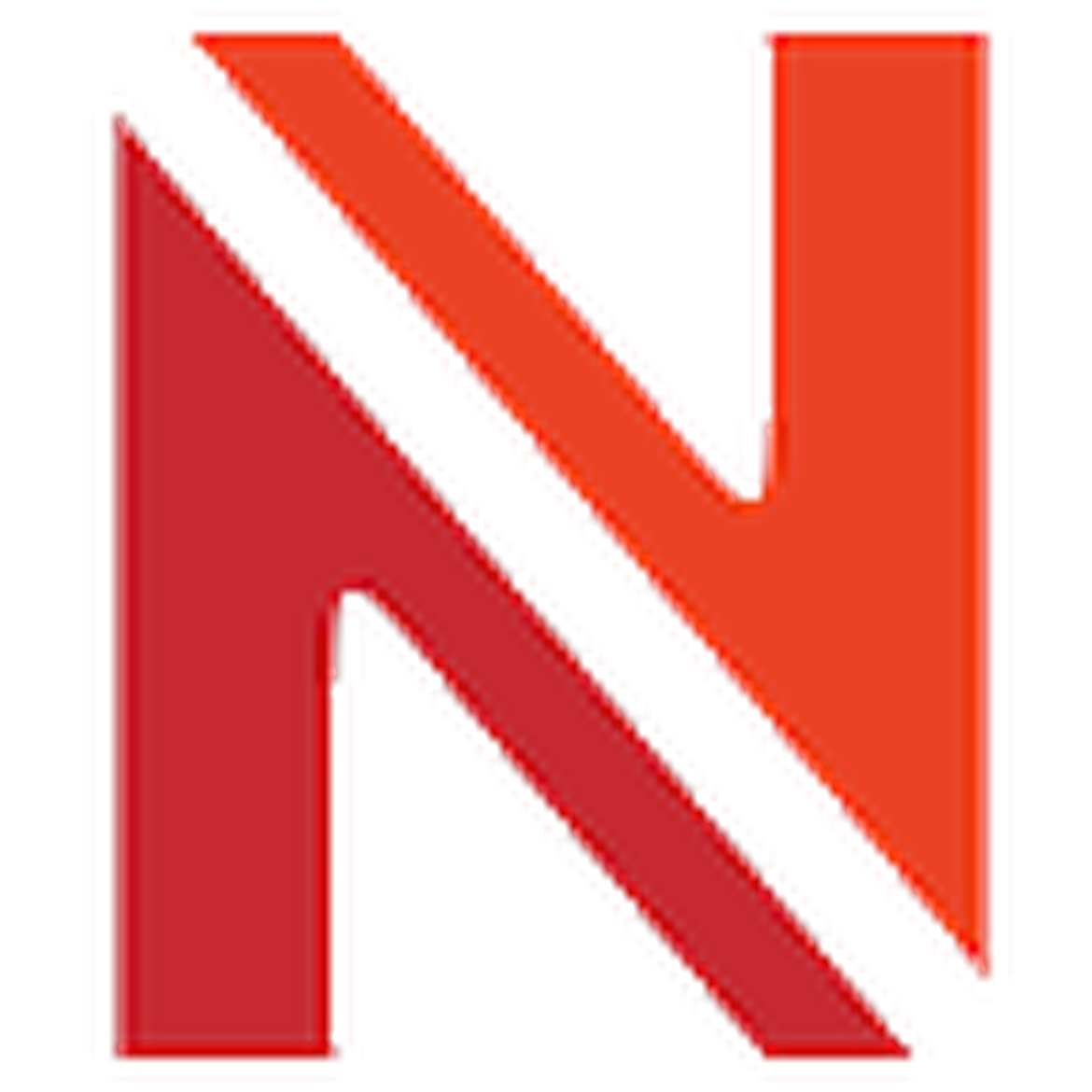
NESPERT CAM performs on-line control at any moment and avoids placing a path and path elements on already nested objects or other paths.
Part-by-part nesting
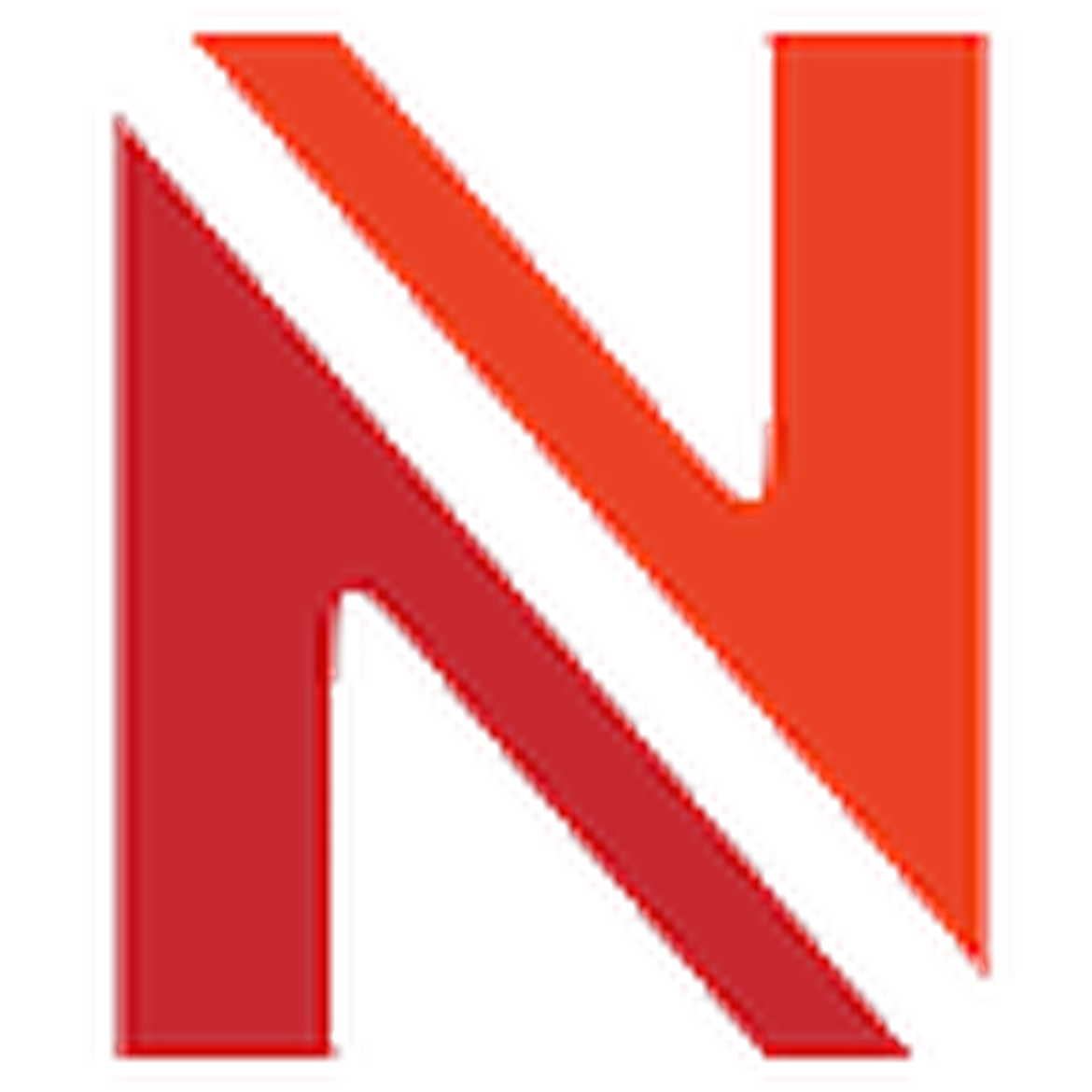
NESPERT CAM creates a processing route according to the parameter Part-by-part nesting – processing all contours of a single part before moving on to the processing of the next part. The Part-by-part nesting can be disabled.
Path elements
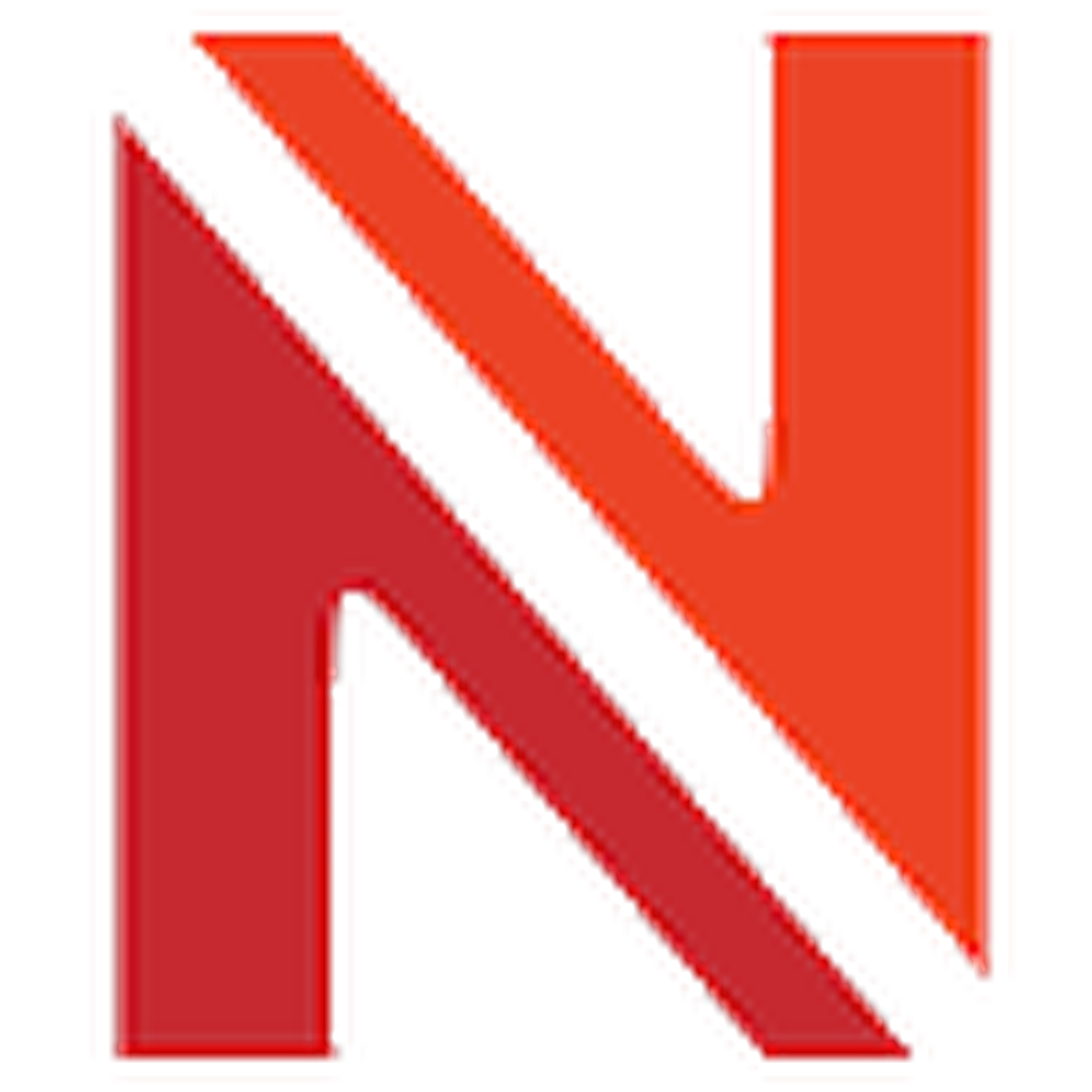
NESPERT CAM allows creating different types of path elements over paths: Start/End point, Gap, Lead-in from an adjacent path, Eyelet, Lead-in from the edge of the plate, Segment, Bridge, Pseudo-bridge, Chain-cut, Chain-cut with circumventing, Corner processing, L-lock, Path direction, Regime, Common cut.
NESPERT CAM automatically creates path elements, outside of the material. Each path element is created as a result of the on-line control against overlapping with adjacent objects.
Start/End point
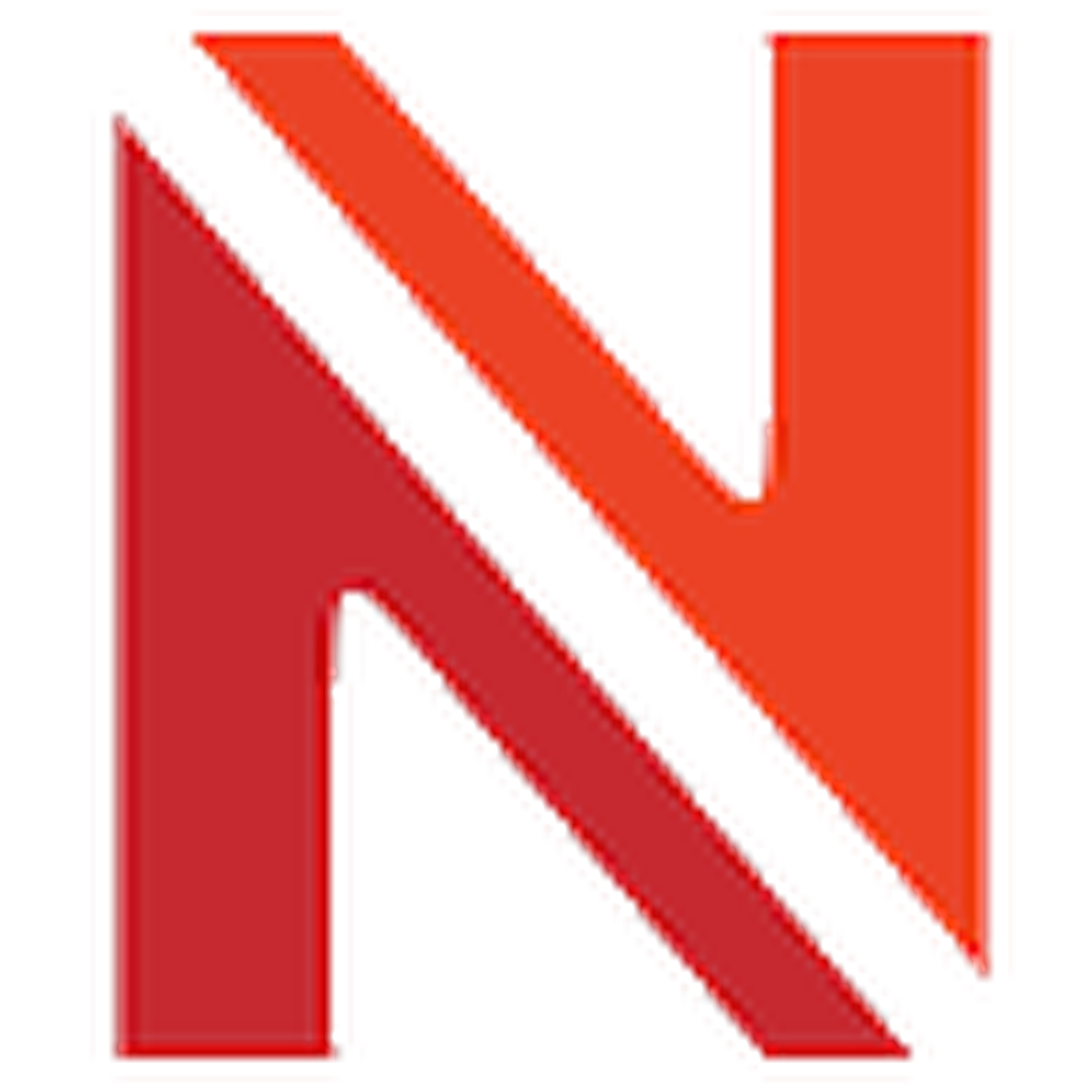
Start/End point of the path is an oriented path element, composed of a pierce point, lead-in, lead-out, turn-off point and distance between lead-in and lead-out (cutting gap).
The type and place of the start/end point are set in the settings or interactively, and NESPERT CAM automatically calculates and assembles the Start/End point to the cutting moves along the contour.
On slots and marking paths the Start/End point are automatically “dissembled”.
Gap
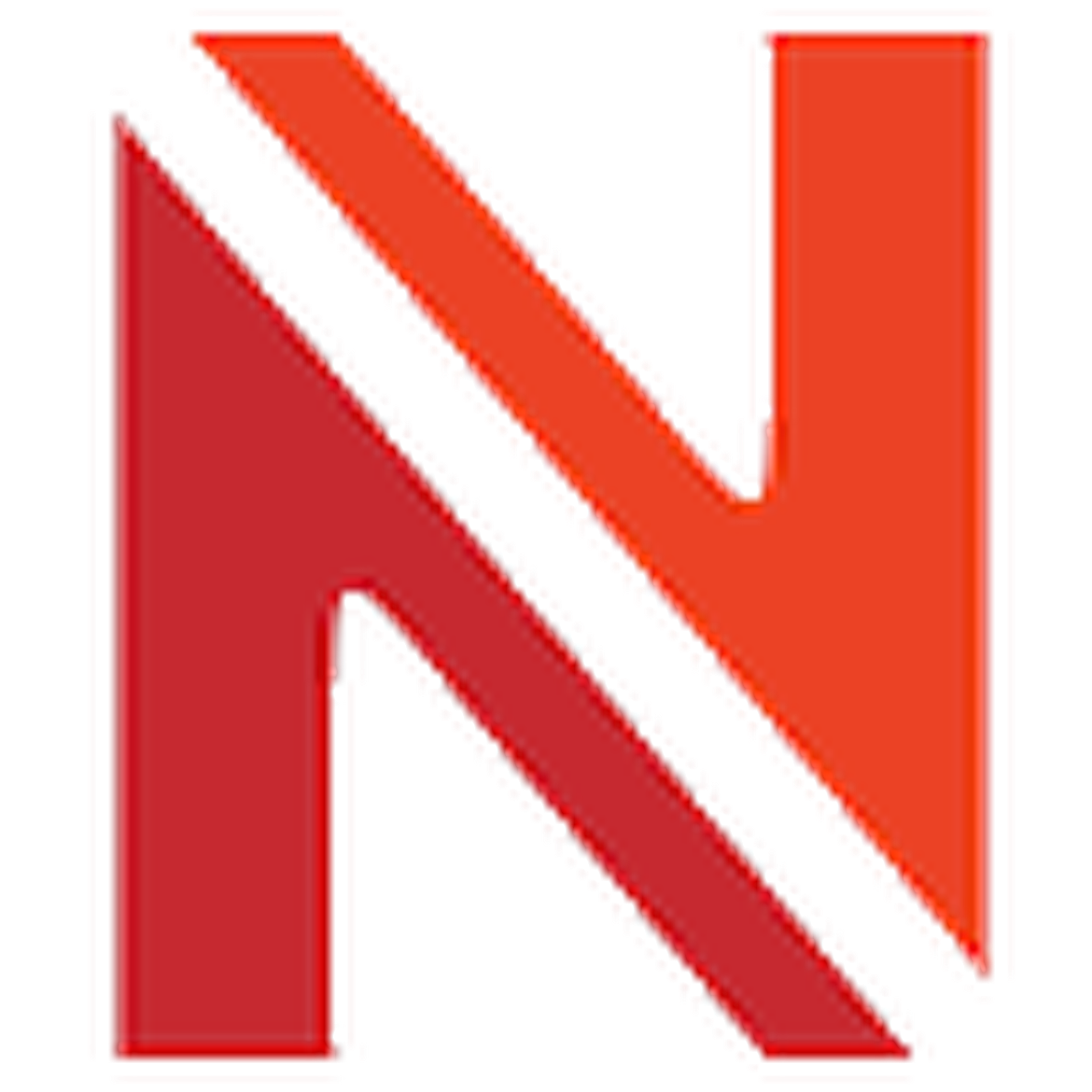
The gap is an oriented sequence of lead-out, turn-off point, cutting gap, pierce point and lead-in. There can be multiple Gaps on a single path. Each path must have one Start/End point. If there isn't such, but gaps are defined, the first created gap is a Start/End point. If the Start/End point and all gaps are removed from the path, the path is deleted.
Lead-in from an adjacent path
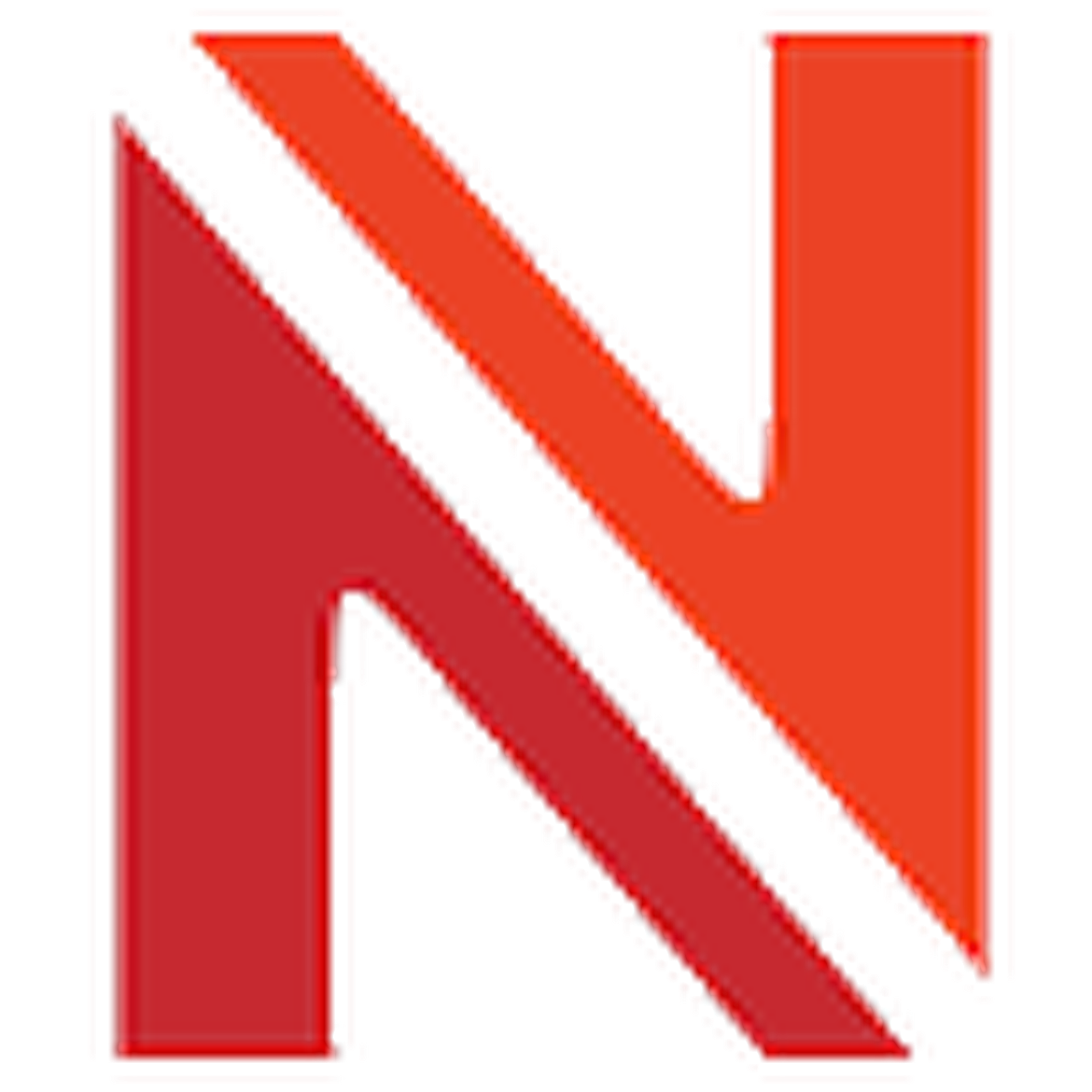
Lead-in from an adjacent path is a lead-in, for which the pierce point lies on an adjacent existing path.
Eyelet
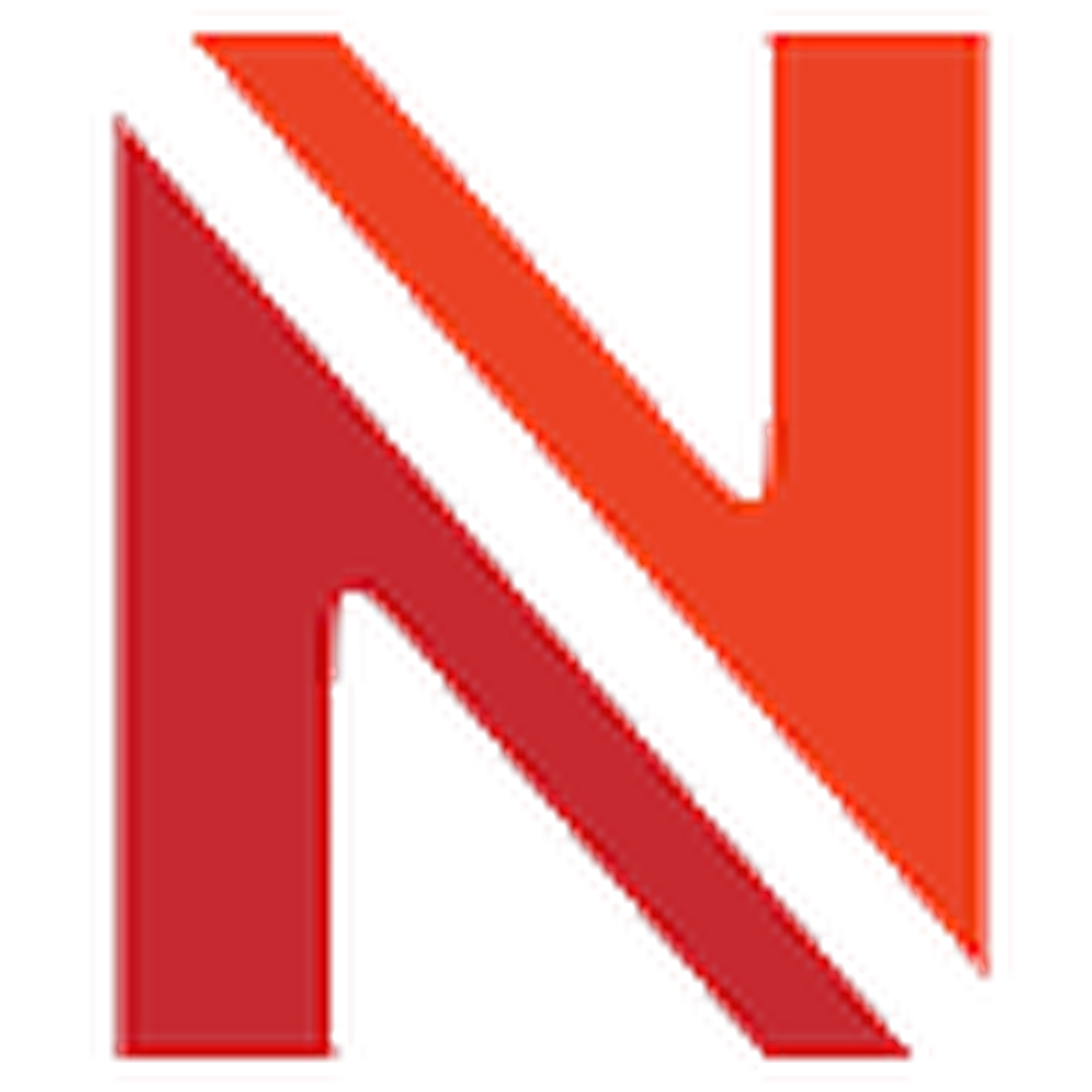
The eyelet is a subtype of a Lead-in from an adjacent path. It is composed of two parts: eyelet in the first path and lead-in from the eyelet to the second path. It allows cutting of parts with short piercing time.
Lead-in from the edge of the plate
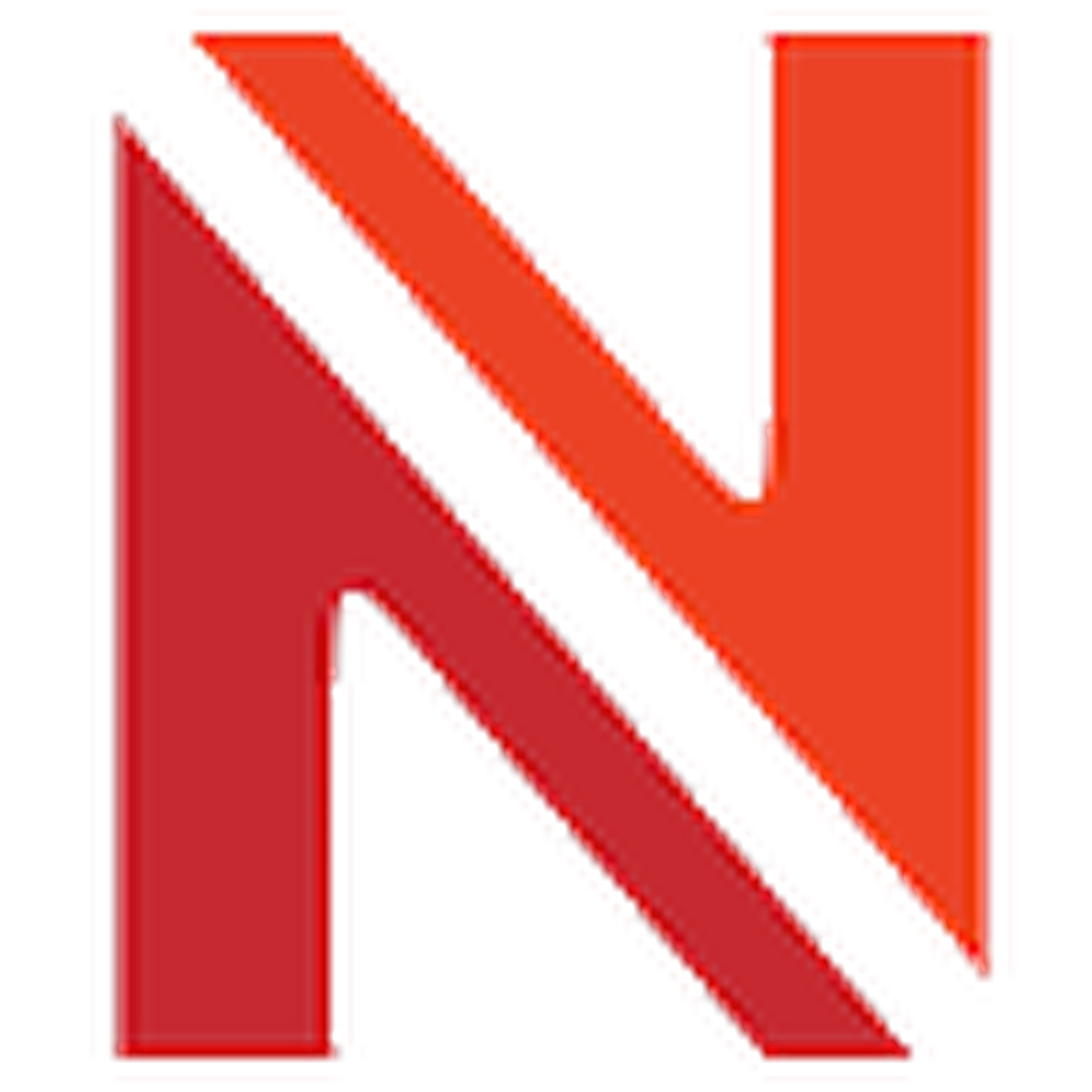
The lead-in from the edge of the plate is a path element, for which the pierce point is on the border of the plate. It is used for decreasing the pierce time and decreasing the amount of heat in the metal.
Path direction
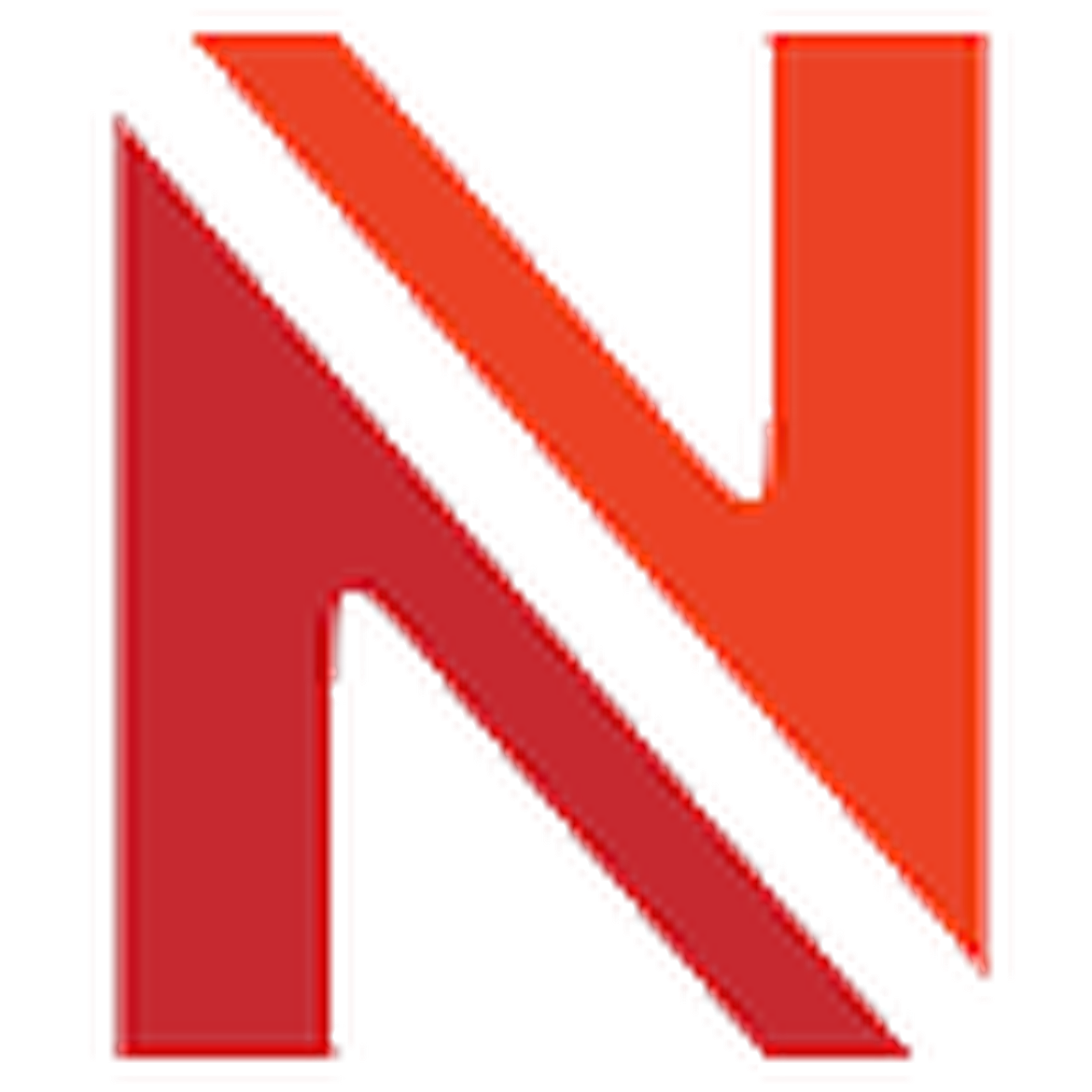
The path direction depends on the type of the part's contour and the Processing technology. The path direction can be reversed, at which the system automatically replaces and orients Start/End points, Gaps and Corner processing.
Segment
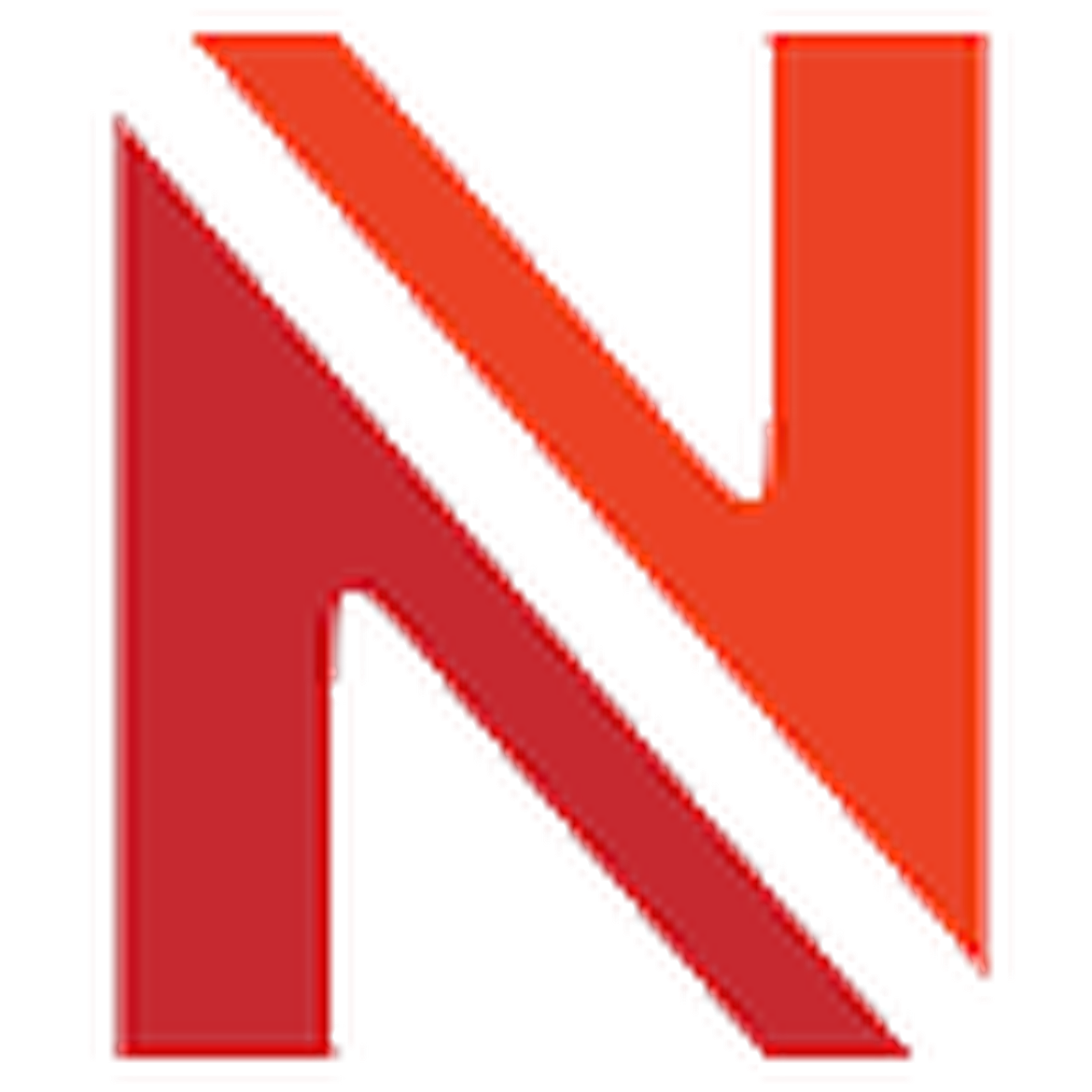
A segment is part of path, limited between two gaps or between a Start/End point and a gap. The segment can be deleted or an allowance can be added to it.
Bridge
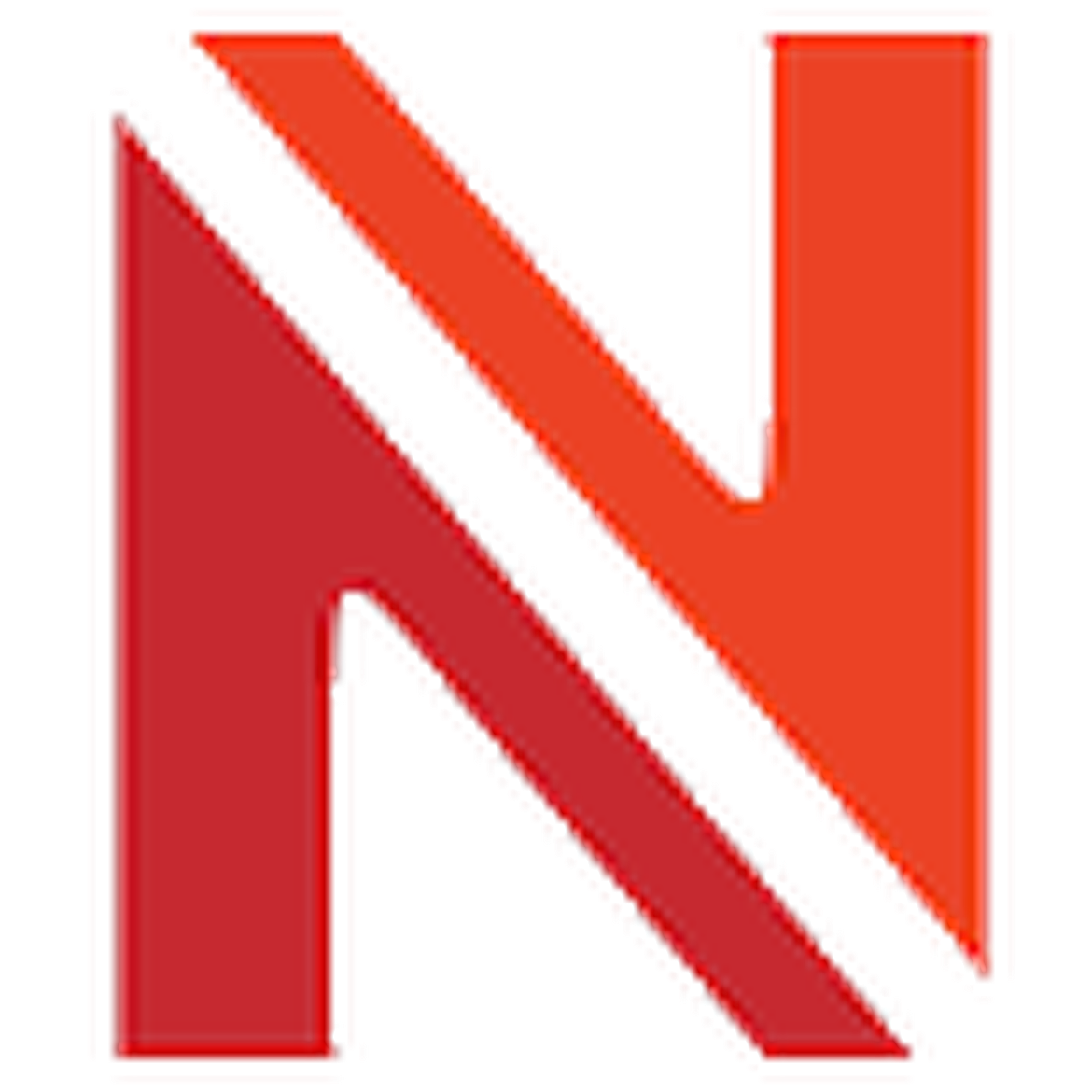
The bridge is a path element, that connects two paths. After the bridge is created both paths join automatically. Placing more than one bridge on two paths changes the topology of these paths.
A separate case of a bridge is an angular negative bridge.
Pseudo-bridge
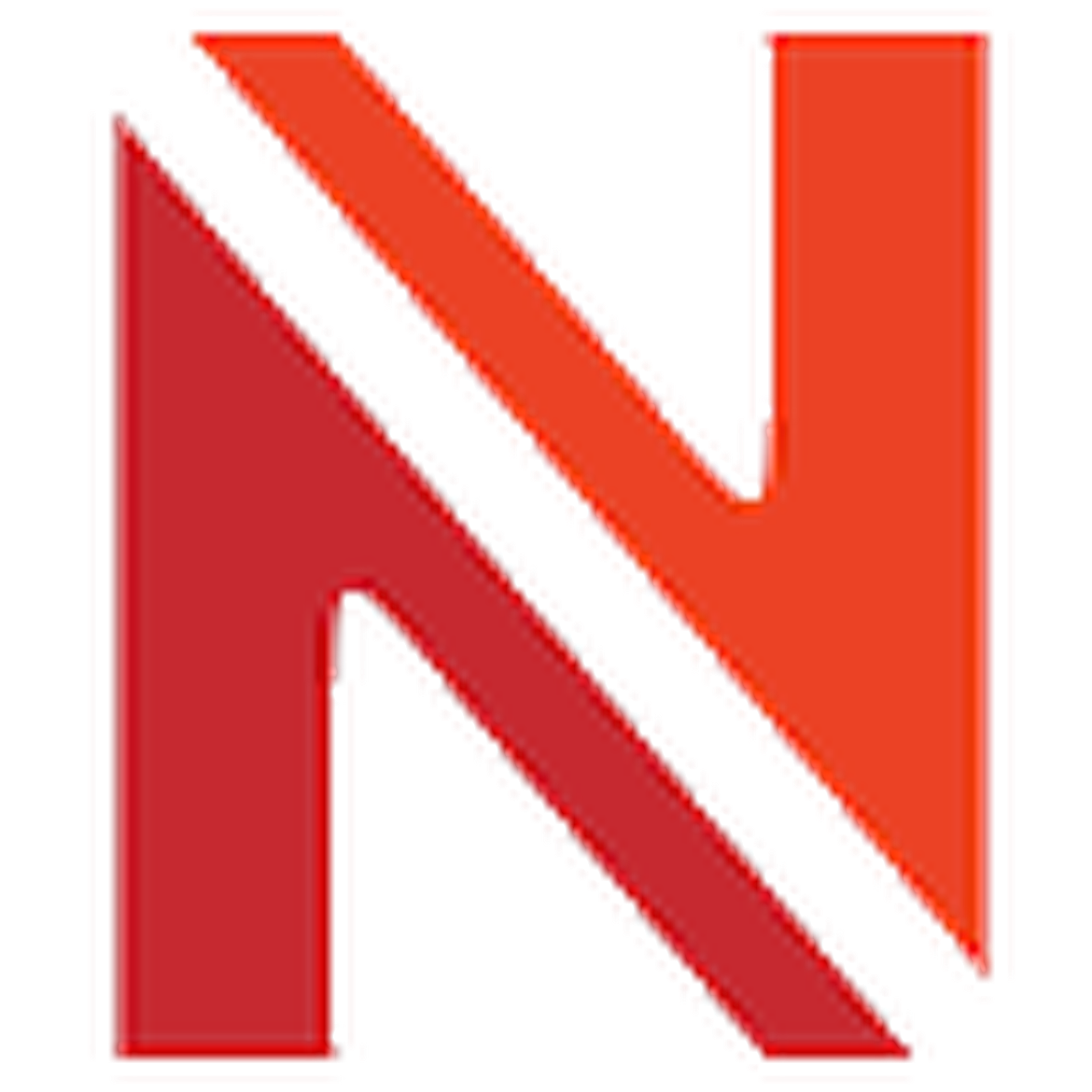
The pseudo-bridge is a path element that is placed on two or more paths without joining them. The pseudo-bridge creates simultaneously mutually oriented gaps on the paths.
Chain-cut
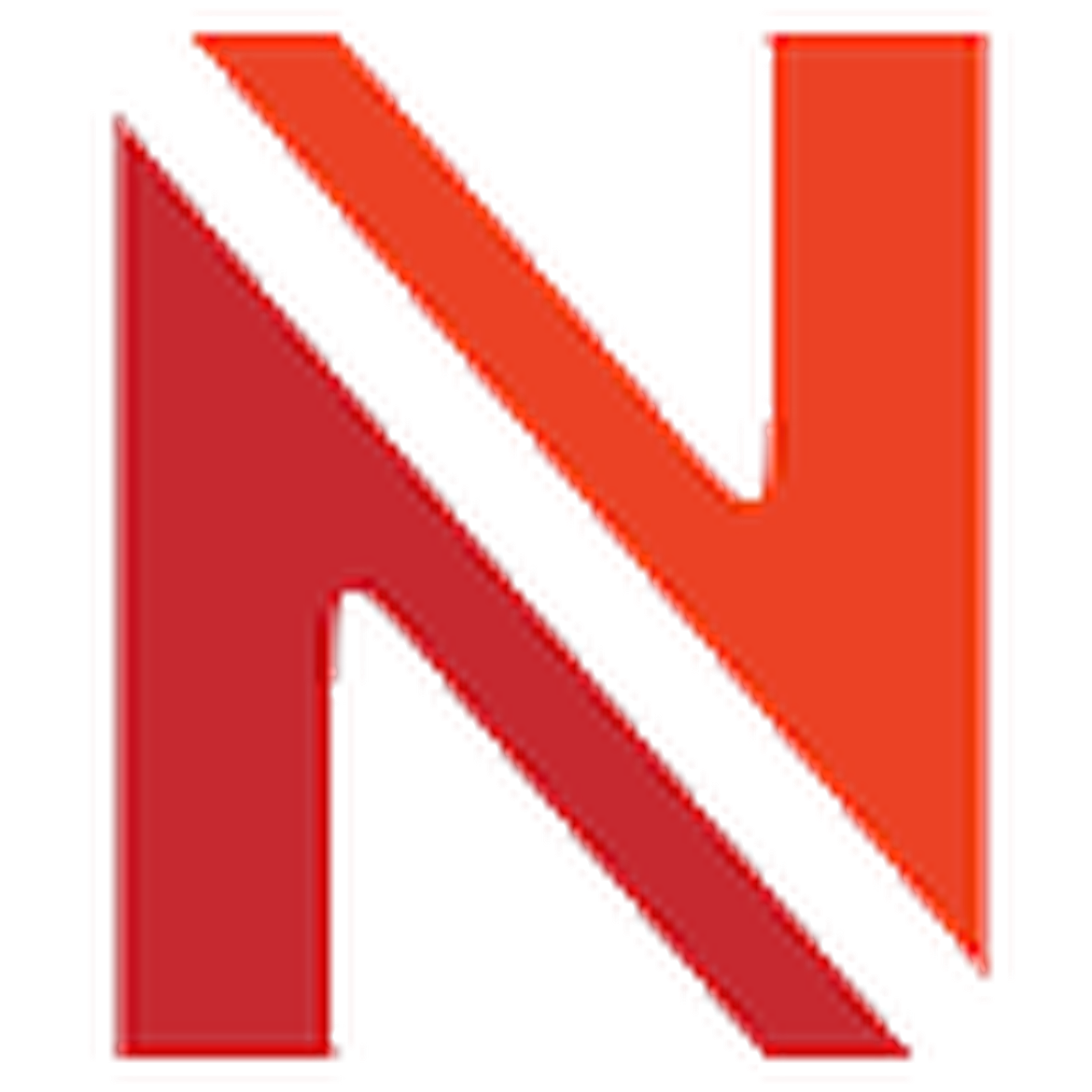
A path element that is interactively placed and which creates a fixed sequence of cutting moves, joining the end and start point of two paths. The chain-cut provides realisation of continuous part-by-part cutting.
Chain-cut with circumventing
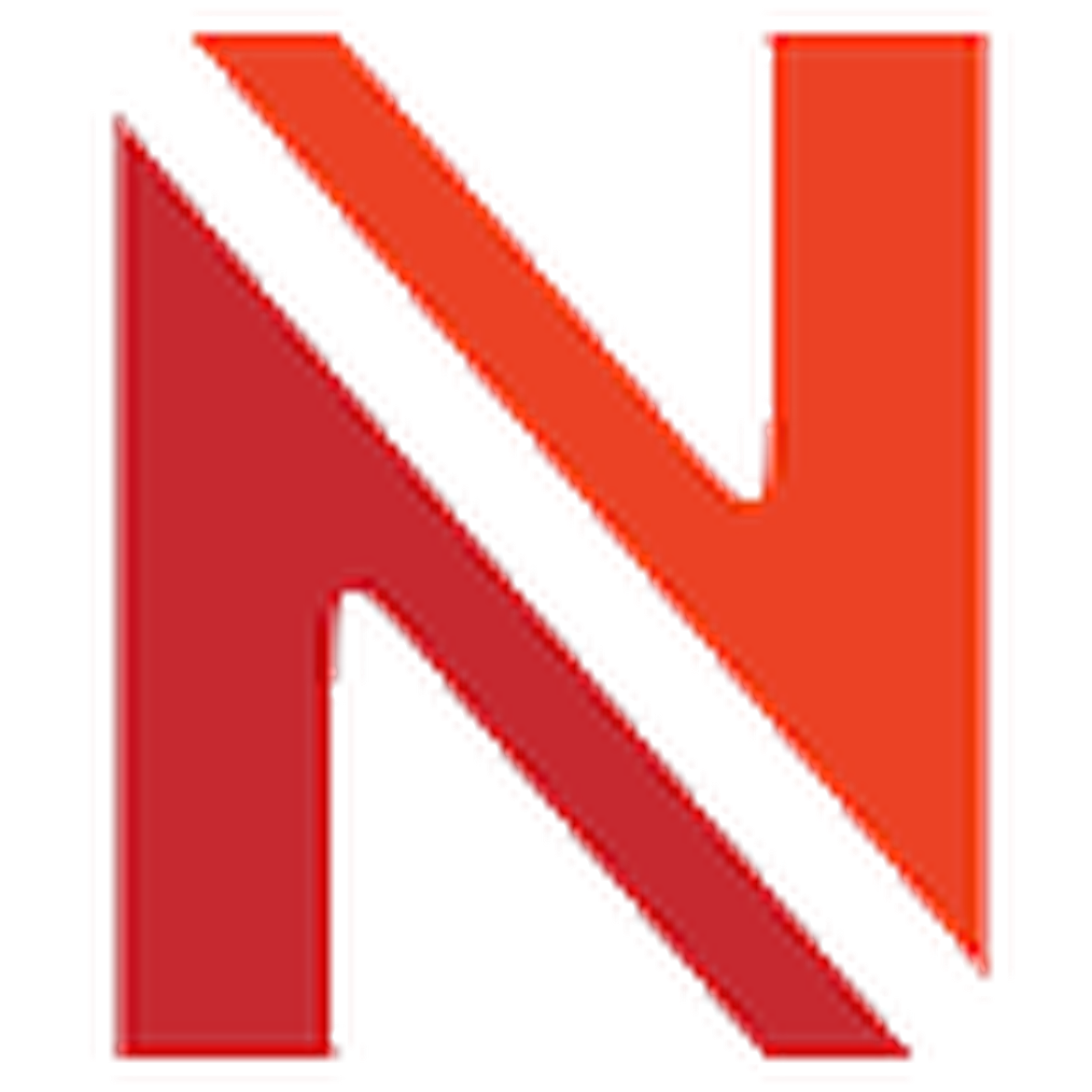
A path element that is interactively and semi-automatically placed which joins two paths with a cutting move without turning-off the cutting. NESPERT CAM calculates a curved path at a minimum distance between the nested objects.
Corner processing
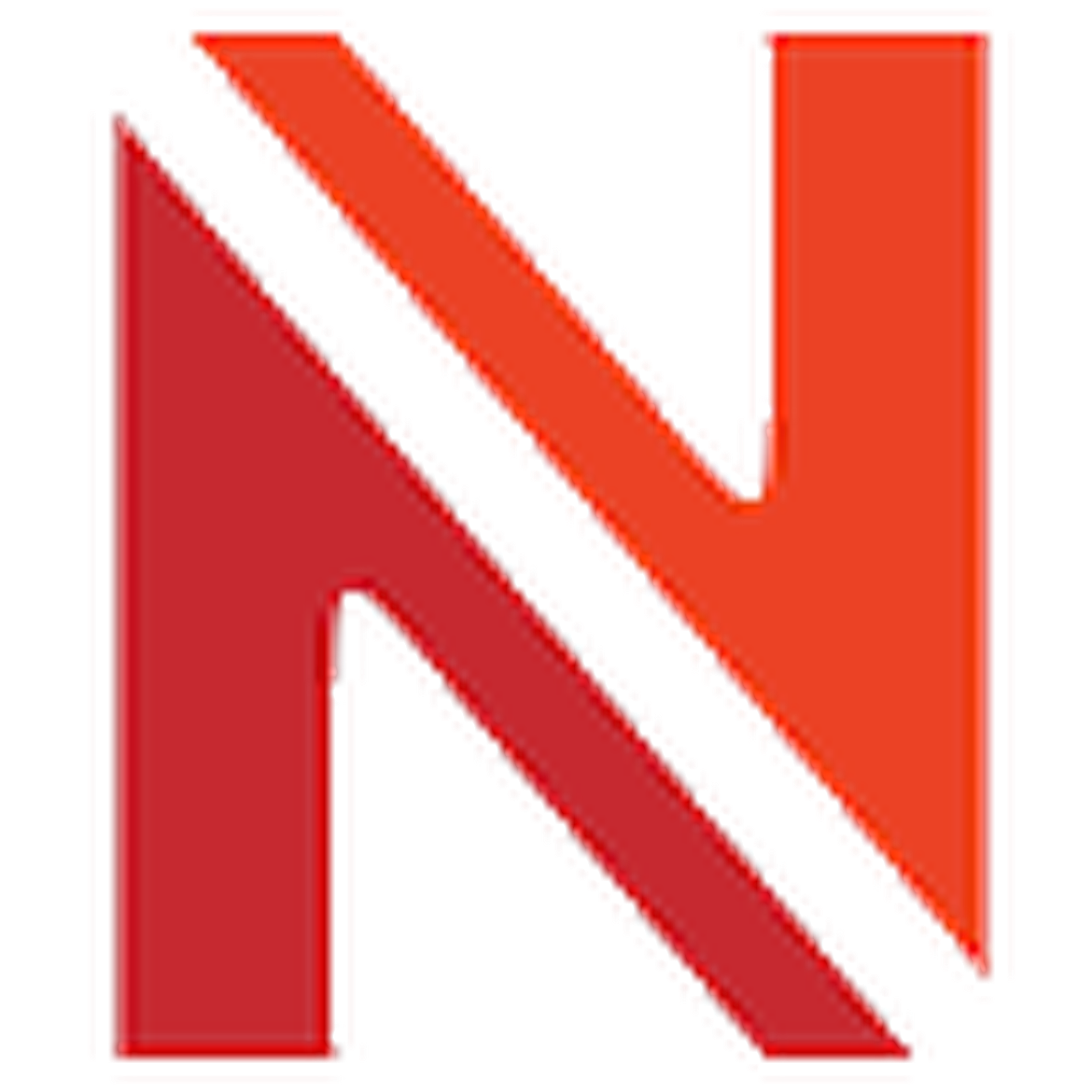
A path element that is interactively and automatically placed on paths for processing of sharp corners in the contours, also called “a loop”.
A corner processing is created to the path in the places where the angle for changing the direction of movement is greater than a parameter. The types of corner processing are: loops, roundings and pauses.
L-lock
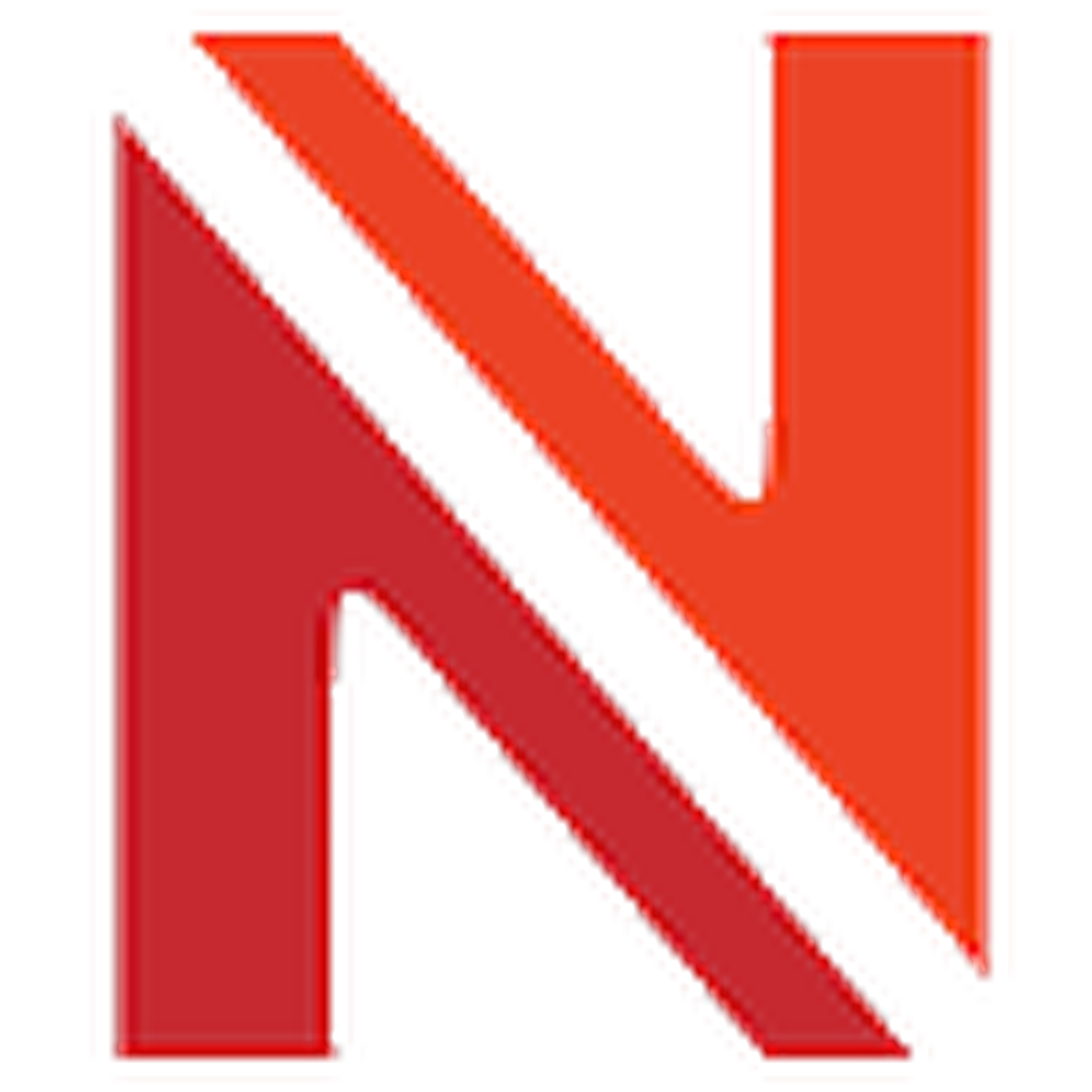
A path element that is interactively placed on the path similarly to a gap. It is used for locking the part to the grid, for limiting the deformation of the part or the scrap during cutting.
Common cuts
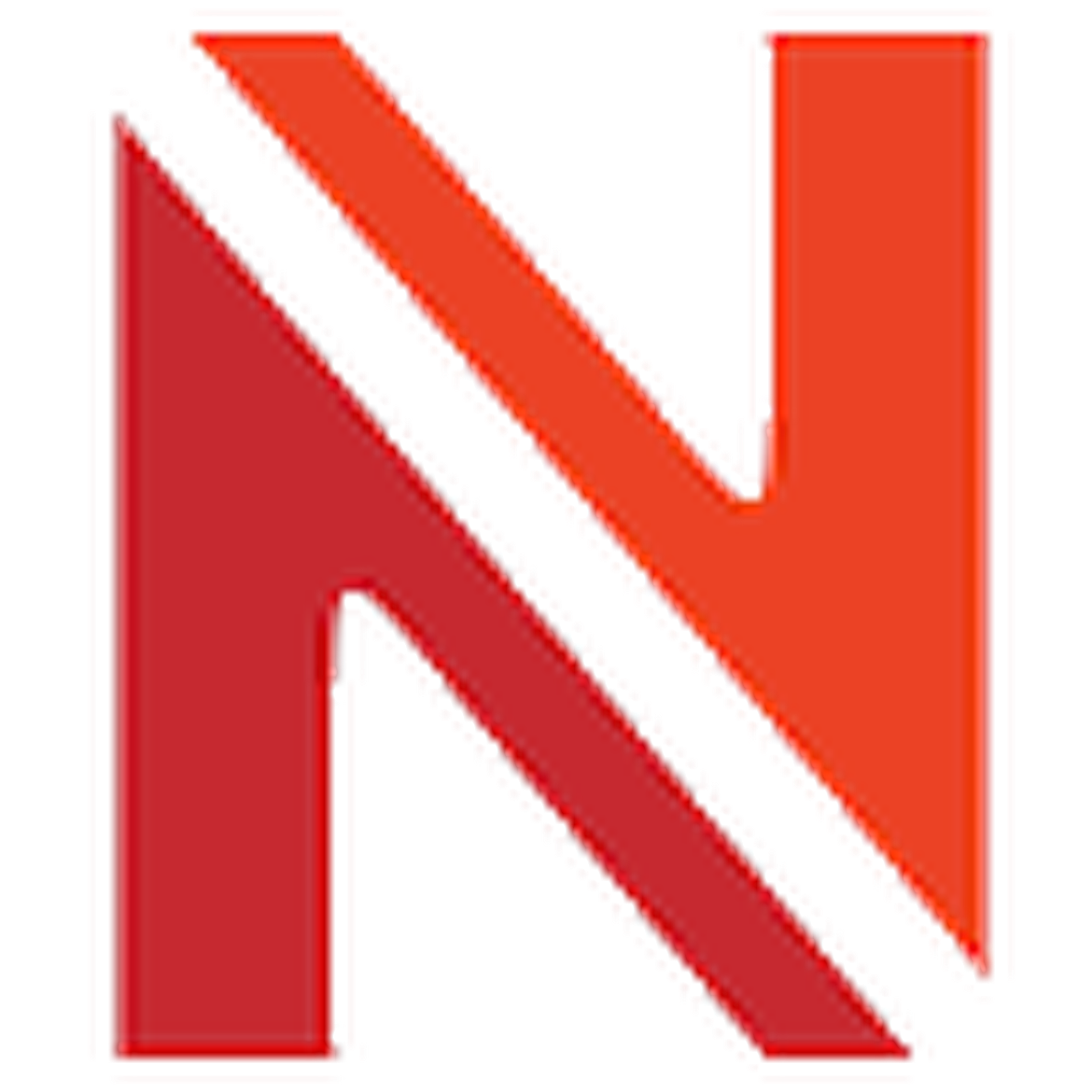
NESPERT CAM creates common cuts by joining common paths with rapid moves. Common paths and common cuts can be joined via manual, interactive and automatic methods of the system.
Control against formation of islands of uncut paths
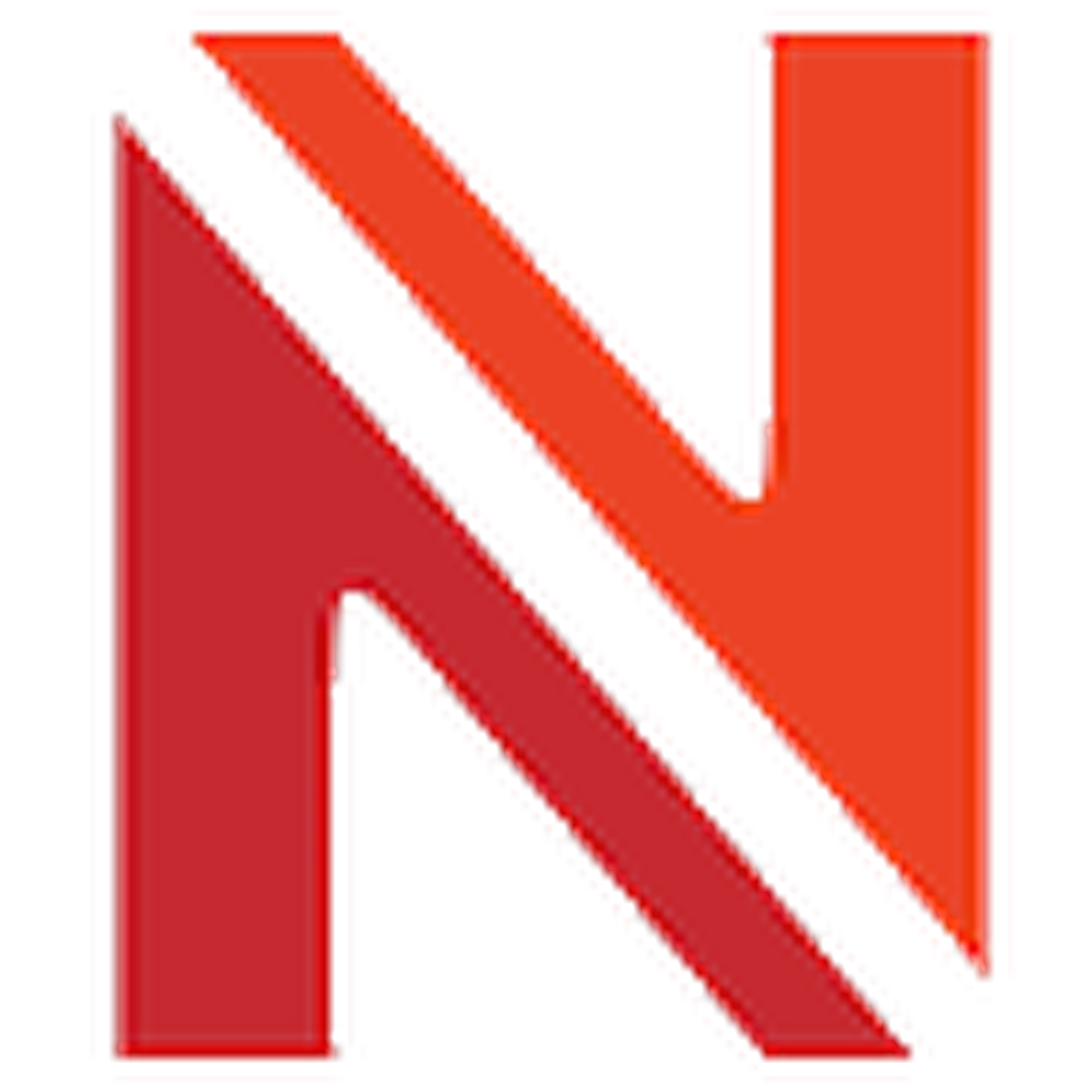
NESPERT CAM allows building bridges between nested parts, for which a cutting technology has not been assigned (parts without paths and route). By automatically creating a cutting technology, the system does not allow the formation of islands of uncut paths.
Control of the sequence when cutting with common cuts
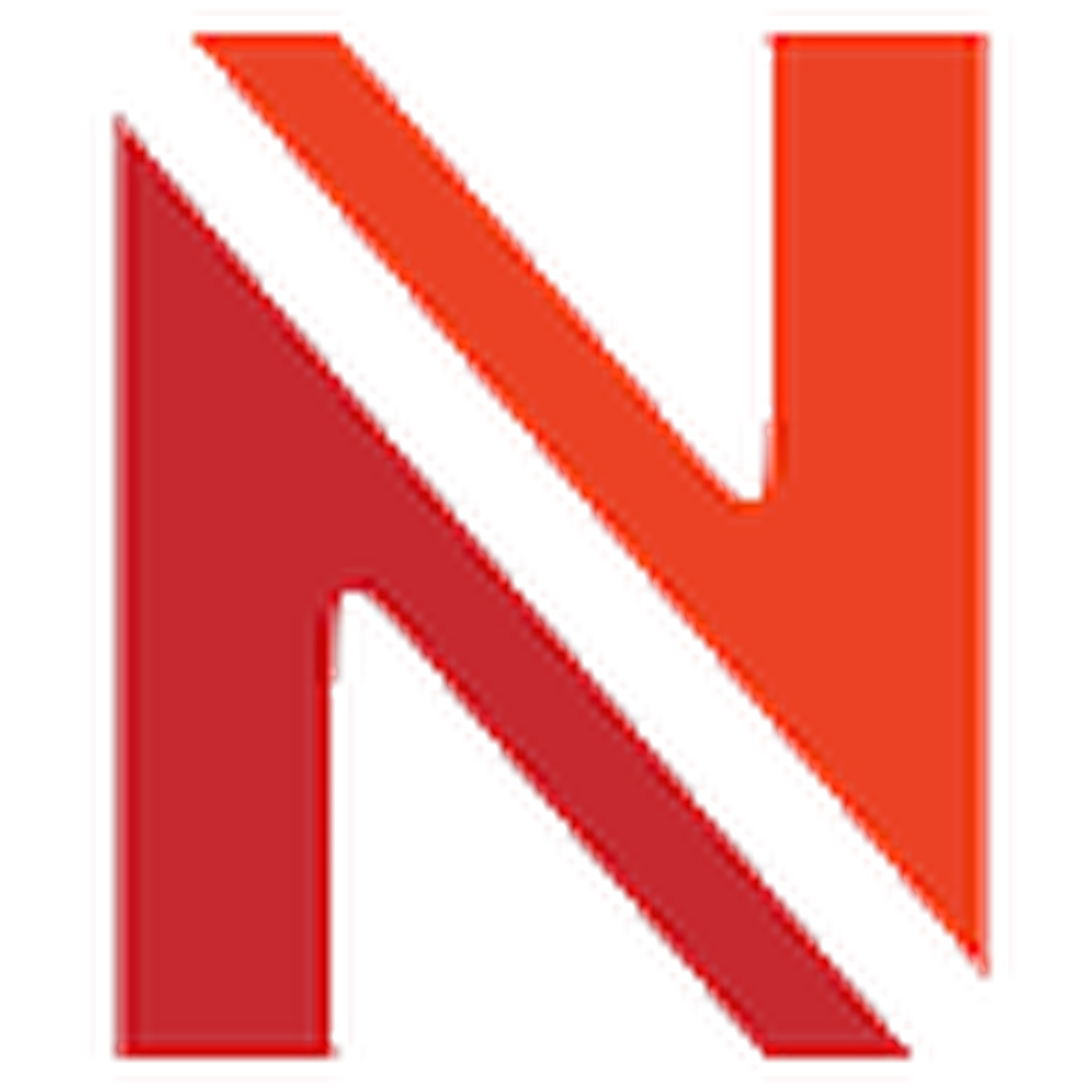
NESPERT CAM creates sequence of common cuts, ensuring the proper processing of the contours of parts with common cuts. In nesting layouts with common cuts, the system automatically sets the cutting of the inserted contours and holes before the enclosing contour of the common cut.
Control of the sequence in chain cutting
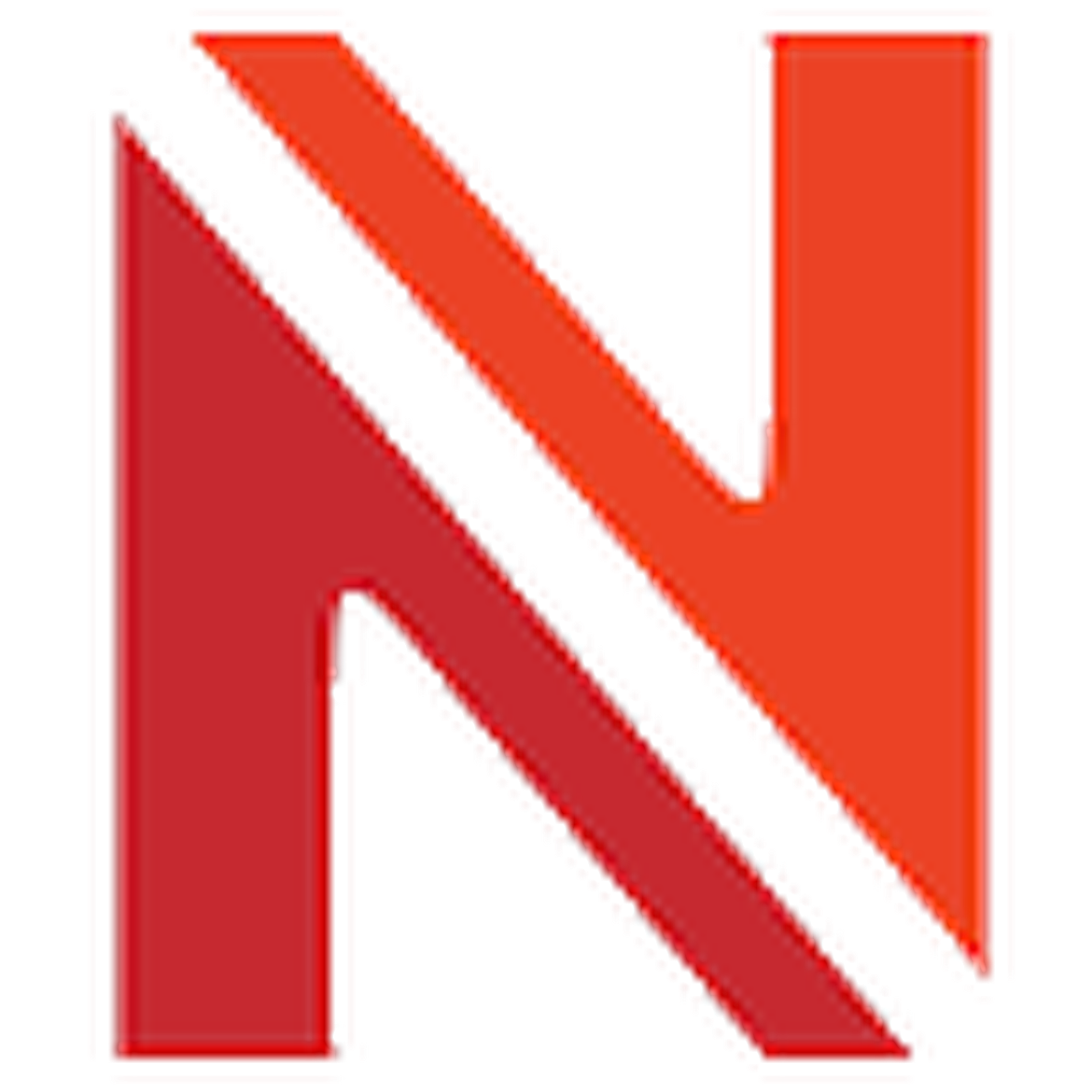
When chain cutting, the system automatically sets the cutting of the nested contours and holes before the enclosing contour with chain cutting.
NC program
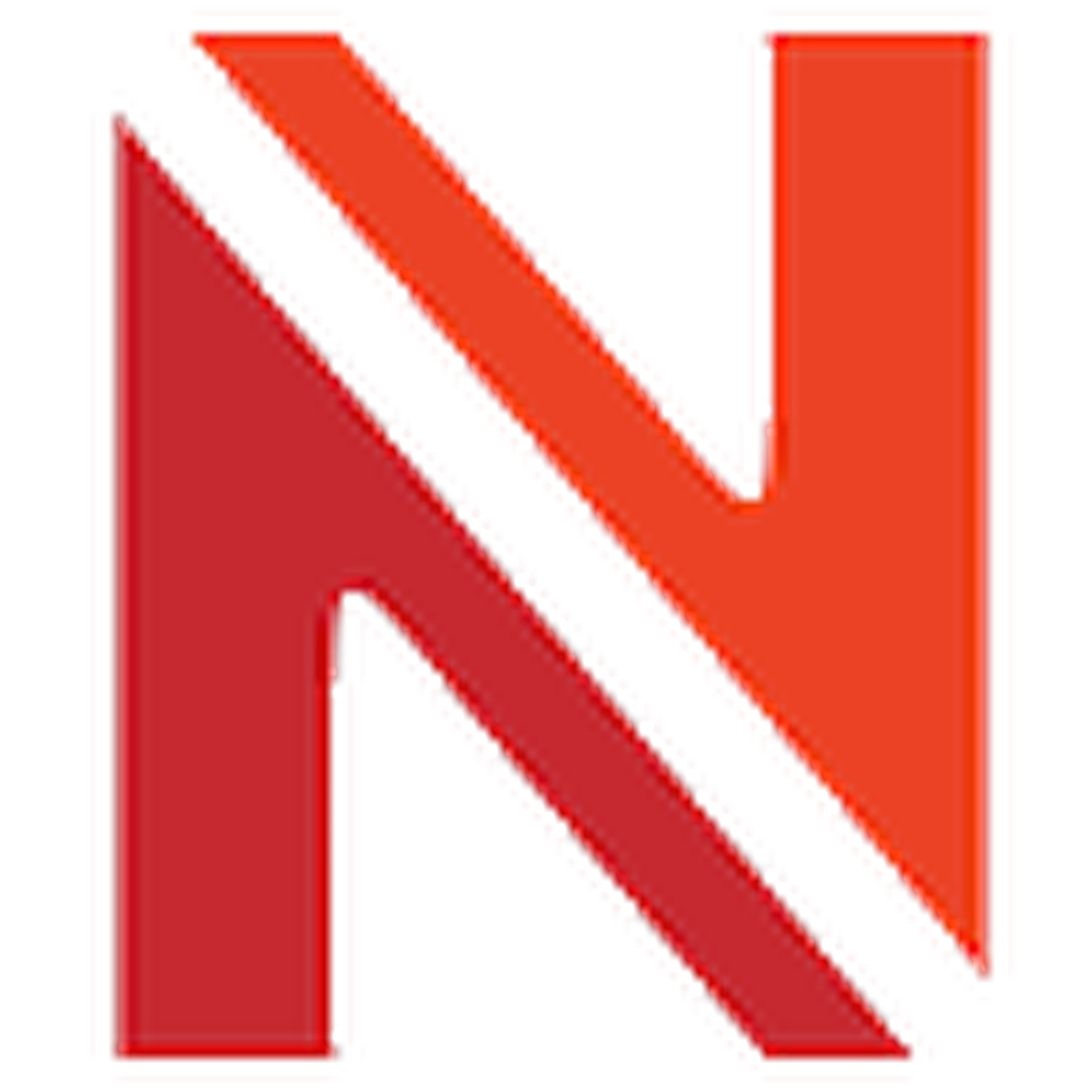
NESPERT CAM generates NC programs from Nesting Layouts with paths and a full route.
NESPERT CAM saves the information about the movement of the tool in a machine-independent description – an XML file. The structure and content of the XML file are defined by VINTECH.
The generation is performed using an external program, called Postprocessor. The Postprocessor reads the XML file and translates the processing from the Nesting Layout to the program language of the specific CNC machine, in an NC program.
The Postprocessors in NESPERT CAM are open and customisable. The requirements for the postprocessor are determined by the capabilities of the machine, the CNC controller and the cutting equipment. The Postprocessor for the specific machine is set once, usually by the supplier of the decision for thermal cutting.
NC programs with option for control of the course of processing (block search)

In different cases the operator of the CNC machine needs performing actions connected with measuring separate parts, assessment of the cutting quality, change of the cutting regime, continuing of the work after interruption of the cutting, etc.
The functionality to quickly and safely control the running of the NC program is specific and especially important for the CNC machines for thermal cutting.
The contemporary CNC machines program the processing with NC programs with complex structure, with sub-routines, with system parameters and allow easy control over the running of the NC program by the operator console.
It is possible: running back through the program, combined with turning-on on or outside the contour, choosing and processing of a selected contour and/or a part; automatically engraving instead of cutting; preliminary drilling of the initial holes without special NC program; running the NC program in test or working mode.
NESPERT CAM allows adjusting for generating NC programs with a structure according to the resources of the CNC system.
NC programs with automatic control of the cutting regime
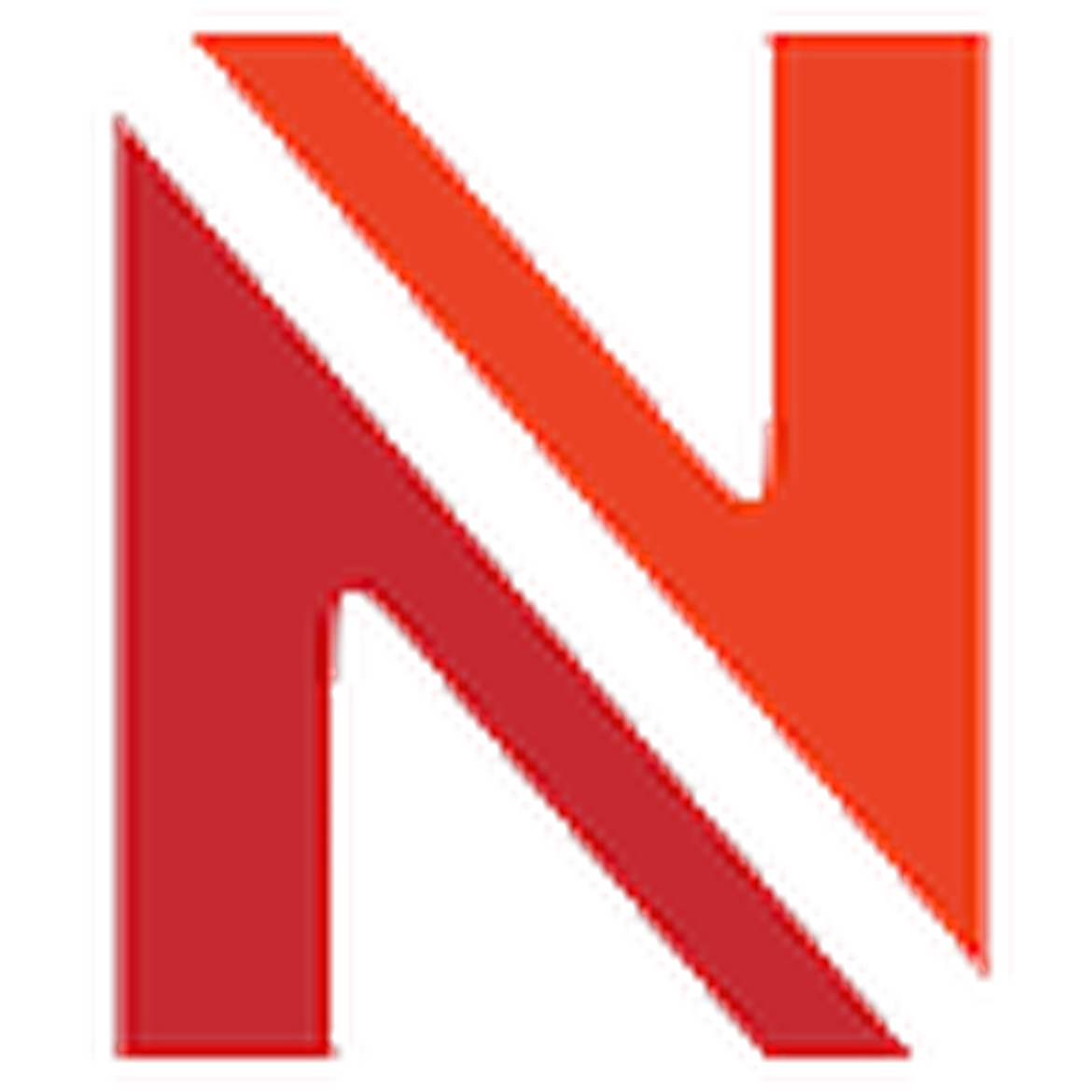
NESPERT CAM reports to the CNC system the material and the thickness of the nested material for some thermal cutting machines by the NC program.
The CNC controller supports technological tables where machine settings of the cutting regime are stored for each material, thickness and path type.
When running the NC program the CNC system analyses the length and the shape of each cutting path and chooses from its Database the machine settings and the cutting regimes for each type of cutting path.
NESPERT CAM easily adjusts to generate NC programs, that control various sets of parameters for water-jet, oxy-fuel, laser or plasma sources.
NC programs with technological tables
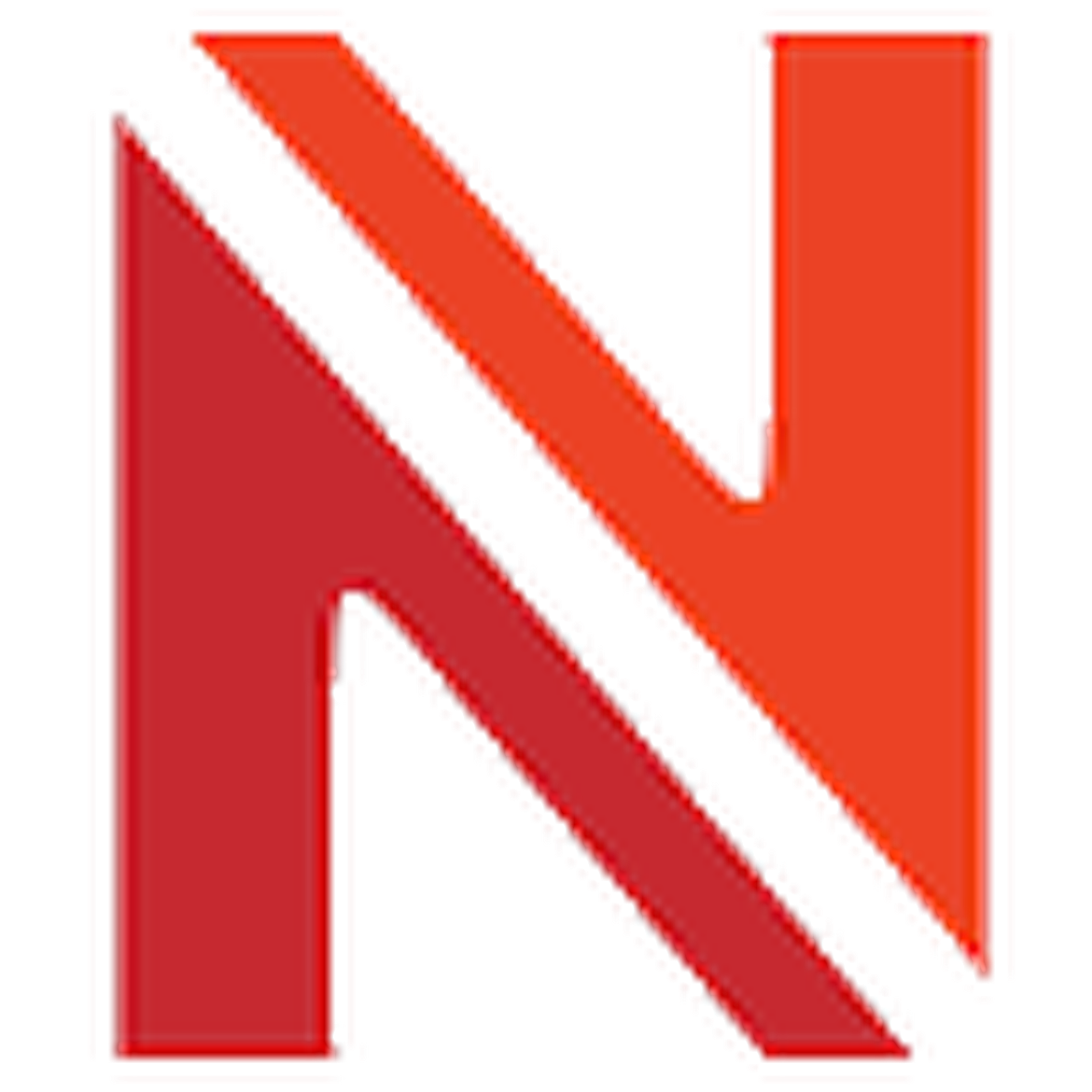
The CNC controller of some laser cutting machines supports technological tables where machine settings of the cutting regime are stored for each material, thickness and path type.
NESPERT CAM analyses the length and the shape of each cutting path in the block and according to the material and the thickness of the plate chooses from the TDB and sends to the NC program the number of the technological table for processing each contour.
In other laser cutting machines the technological tables can be loaded in the CNC controller by the NC program.
NESPERT CAM supports redefinable technological tables in its database and allows easy adjustment to generate NC programs with technological tables.
Reports
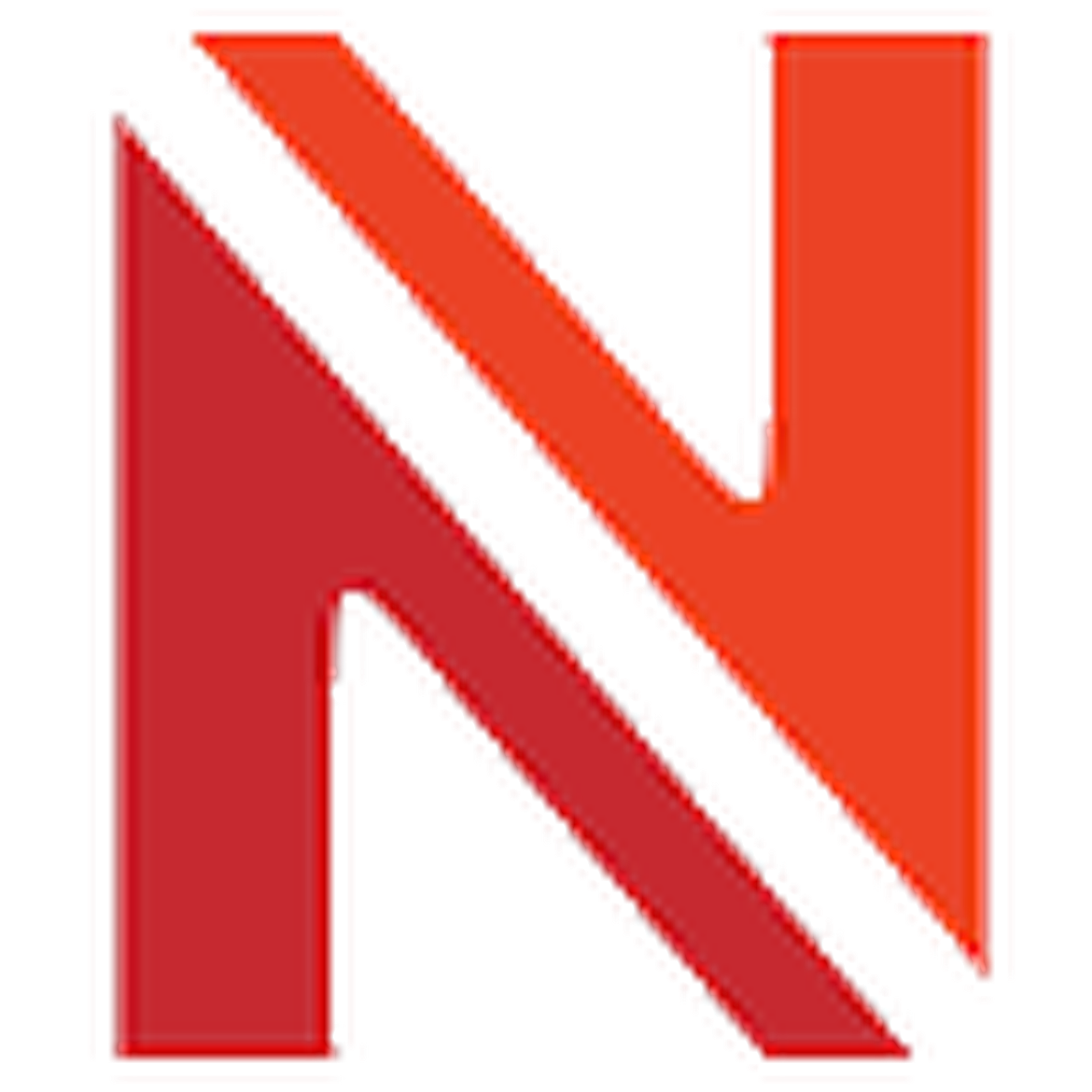
NESPERT CAM generates reports and documents, including technological, organisational and commercial on the base of open and accessible for editing document templates.
They are created for each Layout individually or summarised for all layouts in a project.
They are saved in PDF, DXF or HTML.
The language of the documents matches the localisation language of the system.